I developed a compact vestibular chair for clinical research applications, focusing on reducing cost while maintaining reliable mechanical and electrical performance. The design required continuous rotation of a seated individual at controlled speeds and directions, wireless control functionality, and a robust construction suitable for long-term hospital use. The objective was to produce a significantly less expensive solution than existing products while meeting operational and safety standards.
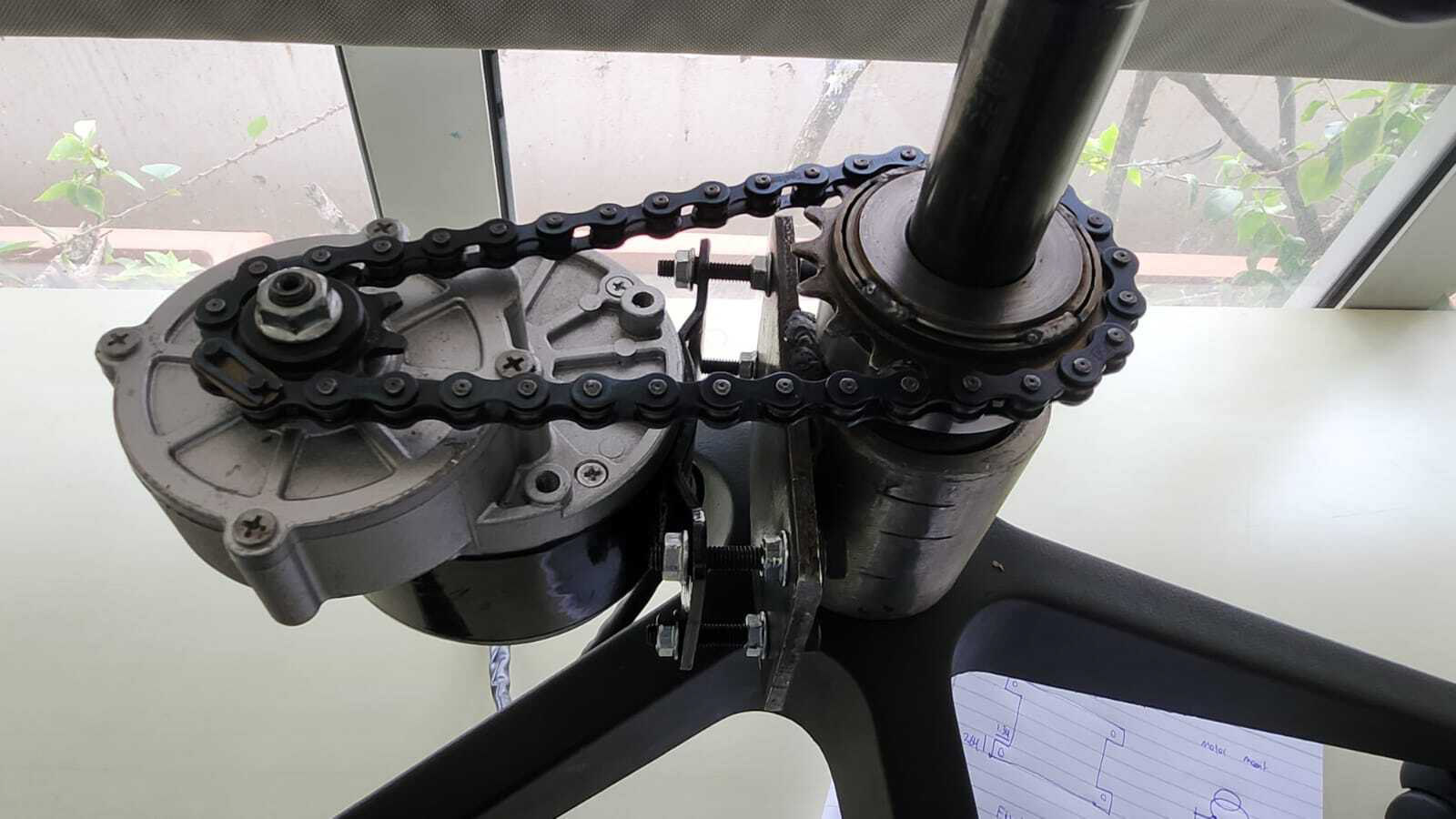
Structural and Mechanical Design
The foundational design utilized an existing office chair base and integrated a motorized rotation mechanism. The chair’s height-adjustable pneumatic cylinder was retained to preserve seating ergonomics, but the standard rotating interface between the seat and base was modified to transmit motor-driven motion effectively.
A 350 W DC motor served as the primary actuator. It was mounted to the chair’s base and connected to the pneumatic cylinder via a chain and sprocket transmission. Brass sprockets and stainless steel structural components were chosen for durability and corrosion resistance. The sprocket assembly was attached directly to the chair’s shaft with a set of grub screws, and the chain length was carefully selected to achieve proper tension and alignment. A custom metal fitting was welded to the motor housing and press-fit into the chair base, minimizing vibration and ensuring stable operation. Adjustable positioning of the sprocket along the shaft enabled realignment after any height adjustments, ensuring that the system maintained proper engagement without compromising the user’s ability to raise or lower the seat.
A custom enclosure made from clear acrylic was fabricated around the chain and sprocket assembly to enhance safety. This guard prevented accidental contact and allowed visual inspection of the drive components. All primary load-bearing elements and the seat support structure were stainless steel, chosen for their mechanical robustness and resistance to wear over repeated use cycles.
A 350 W DC motor served as the primary actuator. It was mounted to the chair’s base and connected to the pneumatic cylinder via a chain and sprocket transmission. Brass sprockets and stainless steel structural components were chosen for durability and corrosion resistance. The sprocket assembly was attached directly to the chair’s shaft with a set of grub screws, and the chain length was carefully selected to achieve proper tension and alignment. A custom metal fitting was welded to the motor housing and press-fit into the chair base, minimizing vibration and ensuring stable operation. Adjustable positioning of the sprocket along the shaft enabled realignment after any height adjustments, ensuring that the system maintained proper engagement without compromising the user’s ability to raise or lower the seat.
A custom enclosure made from clear acrylic was fabricated around the chain and sprocket assembly to enhance safety. This guard prevented accidental contact and allowed visual inspection of the drive components. All primary load-bearing elements and the seat support structure were stainless steel, chosen for their mechanical robustness and resistance to wear over repeated use cycles.
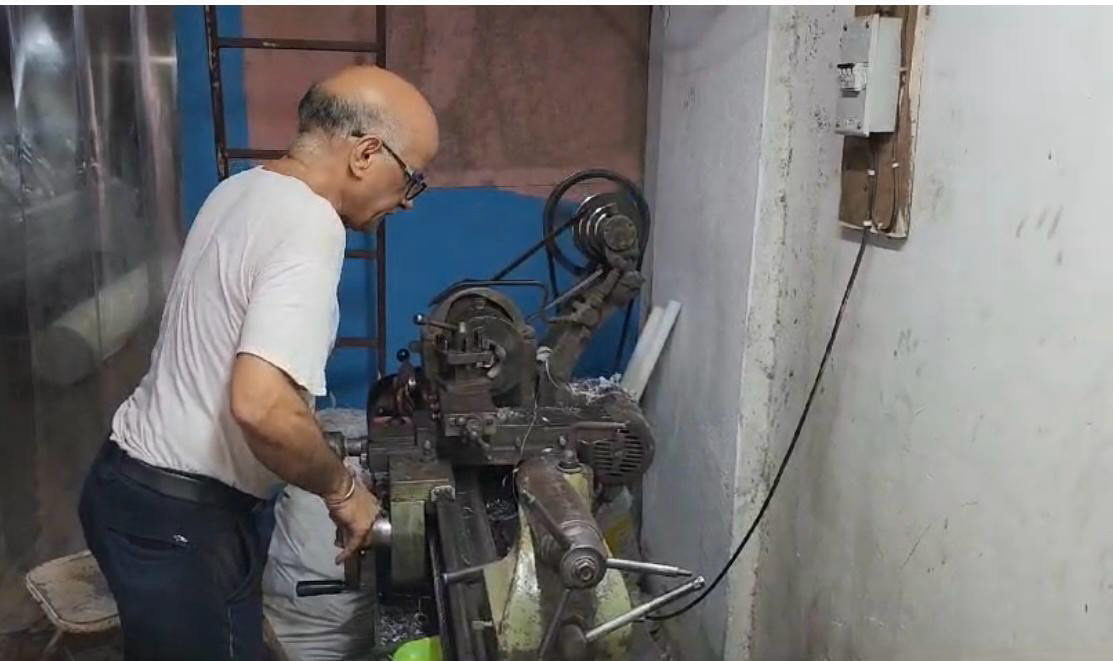
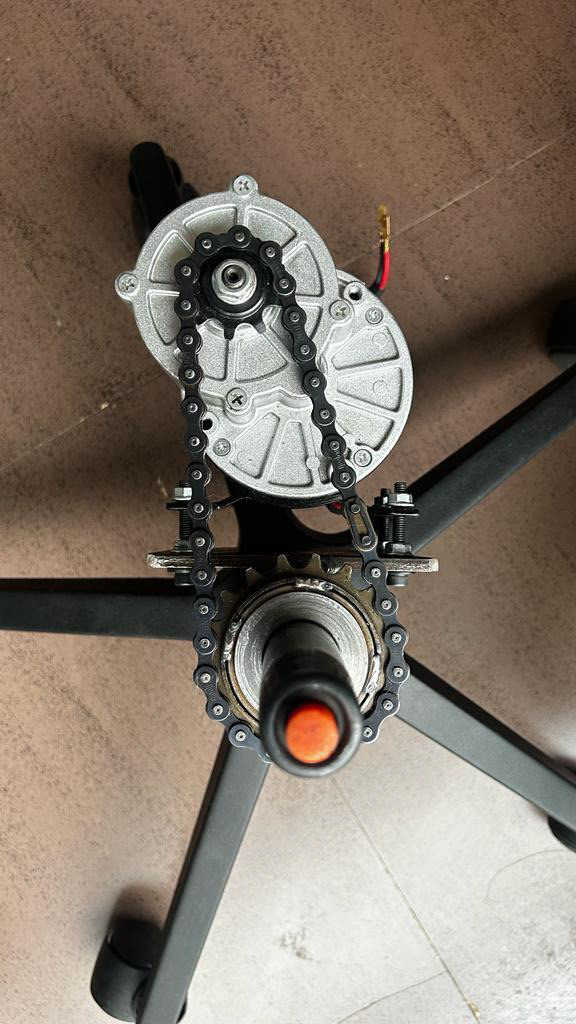
Motor Control and Electrical Configuration
Wireless operation was essential to allow continuous rotation without entangling cables. A wireless current reversing unit, likely employing an H-bridge or equivalent commercial module, enabled the operator to switch motor polarity and thus reverse the rotational direction. This functionality ensured that both clockwise and counterclockwise motions could be selected as required by clinical protocols.
Speed regulation was achieved through incremental supply voltage adjustments using multiple resistor values connected via a multi-channel wireless relay module. Each relay channel introduced a different series resistance path, allowing eight discrete speed settings. The chair achieved approximately 1–1.5 rotations per second at the highest setting, while the lowest setting produced about 0.2–0.5 rotations per second. The resistors used were high-wattage power resistors rated for continuous dissipation to accommodate the motor’s current draw without overheating. Their values were determined through iterative testing with a tachometer to correlate applied voltage levels with the actual angular velocity at the seat.
Care was taken to clamp the battery firmly at the chair's base, ensuring a stable power source and simplifying the charging process—a dedicated adaptor allowed for easy recharging of the onboard battery system.
Speed regulation was achieved through incremental supply voltage adjustments using multiple resistor values connected via a multi-channel wireless relay module. Each relay channel introduced a different series resistance path, allowing eight discrete speed settings. The chair achieved approximately 1–1.5 rotations per second at the highest setting, while the lowest setting produced about 0.2–0.5 rotations per second. The resistors used were high-wattage power resistors rated for continuous dissipation to accommodate the motor’s current draw without overheating. Their values were determined through iterative testing with a tachometer to correlate applied voltage levels with the actual angular velocity at the seat.
Care was taken to clamp the battery firmly at the chair's base, ensuring a stable power source and simplifying the charging process—a dedicated adaptor allowed for easy recharging of the onboard battery system.
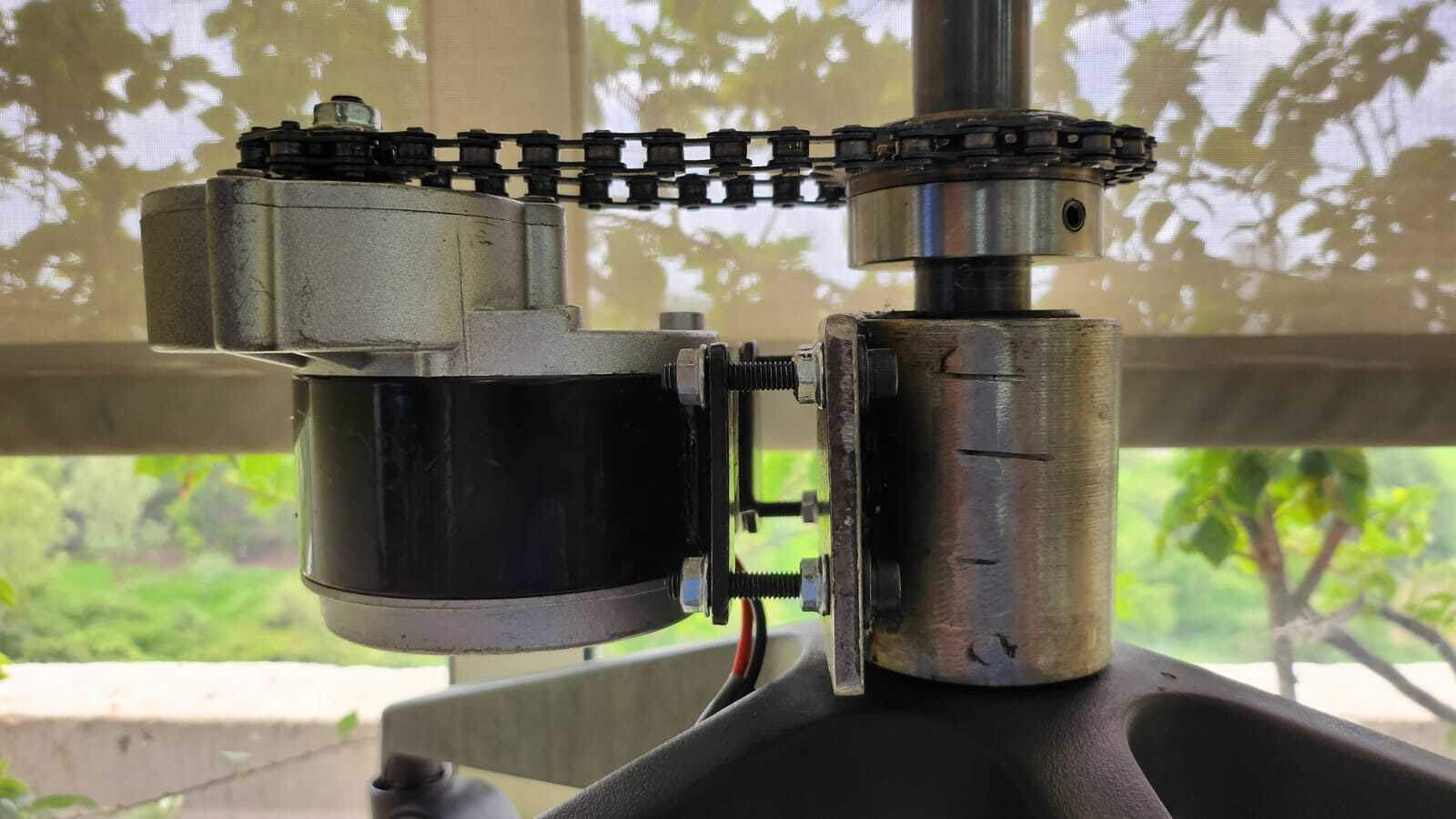
Testing and Verification
Initial testing included verifying motor speed increments, aligning the chain and sprockets, and evaluating load performance under varying patient weights. The rotational speed remained consistent and was not significantly affected by patient mass within typical clinical usage ranges. Testing with a multimeter, tachometer, and controlled loading scenarios helped define the resistor values and confirm that the motor’s output matched expected performance targets.
During the testing phase, adjustments were made, including improving the chain alignment, refining the tensioning mechanism, and ensuring the wireless control signals remained reliable over extended operational periods. The enclosure and guard systems were inspected to confirm that all moving parts were inaccessible to the user, thus mitigating safety risks.
During the testing phase, adjustments were made, including improving the chain alignment, refining the tensioning mechanism, and ensuring the wireless control signals remained reliable over extended operational periods. The enclosure and guard systems were inspected to confirm that all moving parts were inaccessible to the user, thus mitigating safety risks.
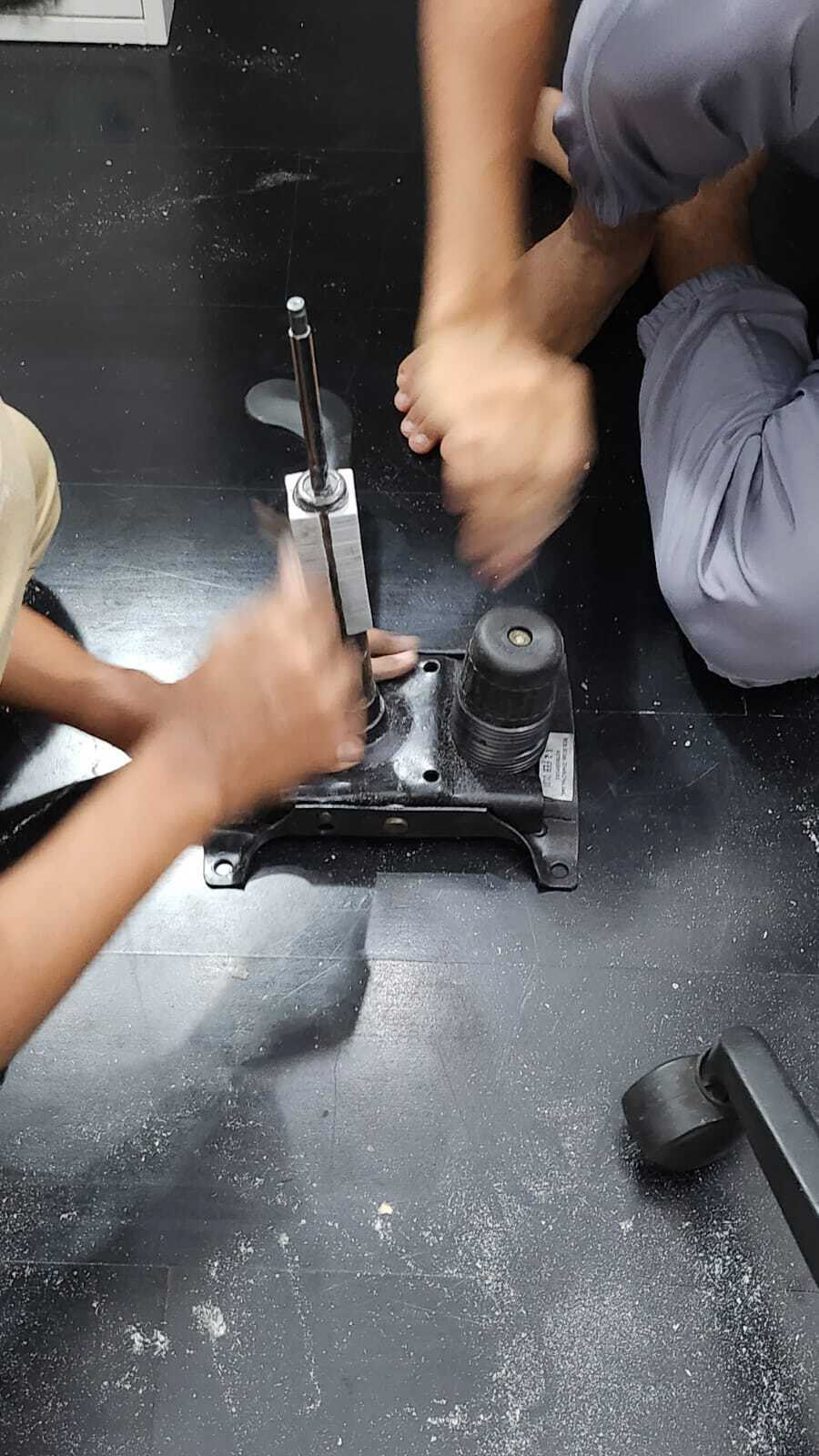
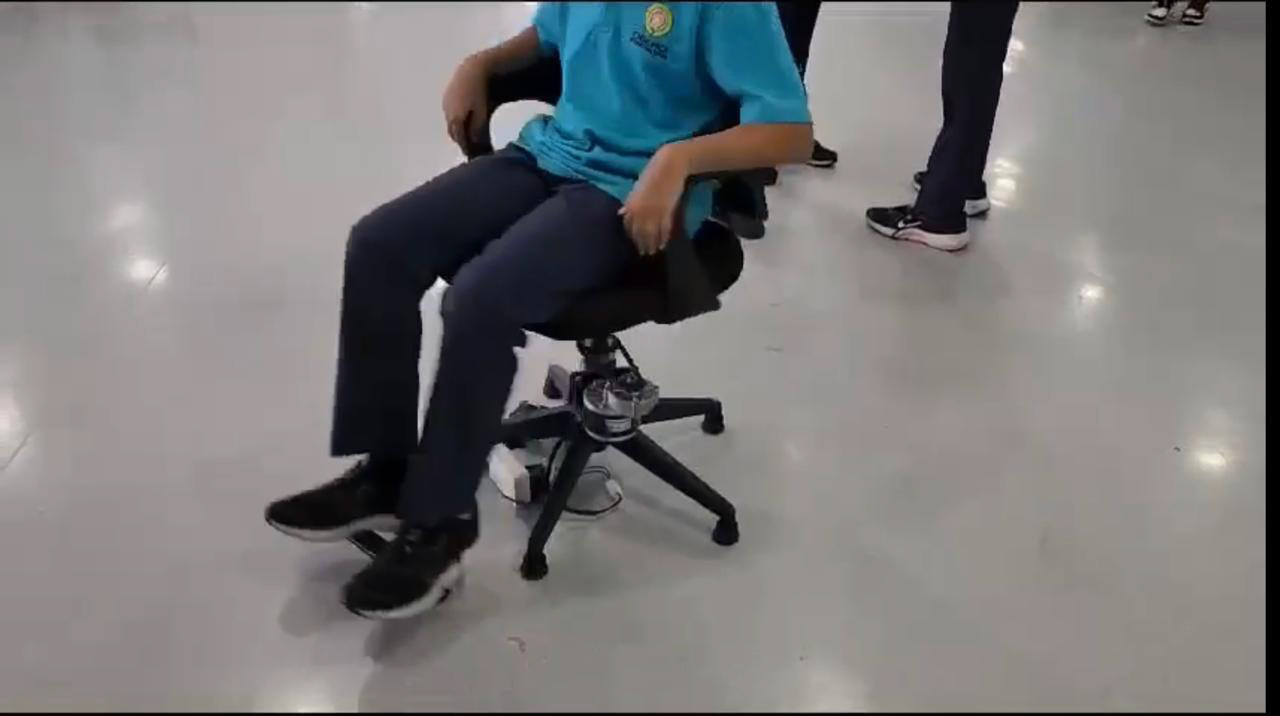
From this project, I gained experience in integrating mechanical and electrical subsystems to achieve precise motion control. The development process refined my skills in selecting appropriate drive components, implementing robust coupling methods, and performing iterative testing with measurement tools to correlate design parameters with operational outcomes. In future work, pursuing more advanced electronic controls, such as closed-loop feedback systems, could enable automatic speed regulation and improve user interface options. Additionally, exploring alternative motor technologies or modular drive components might reduce maintenance requirements and enhance overall system reliability.
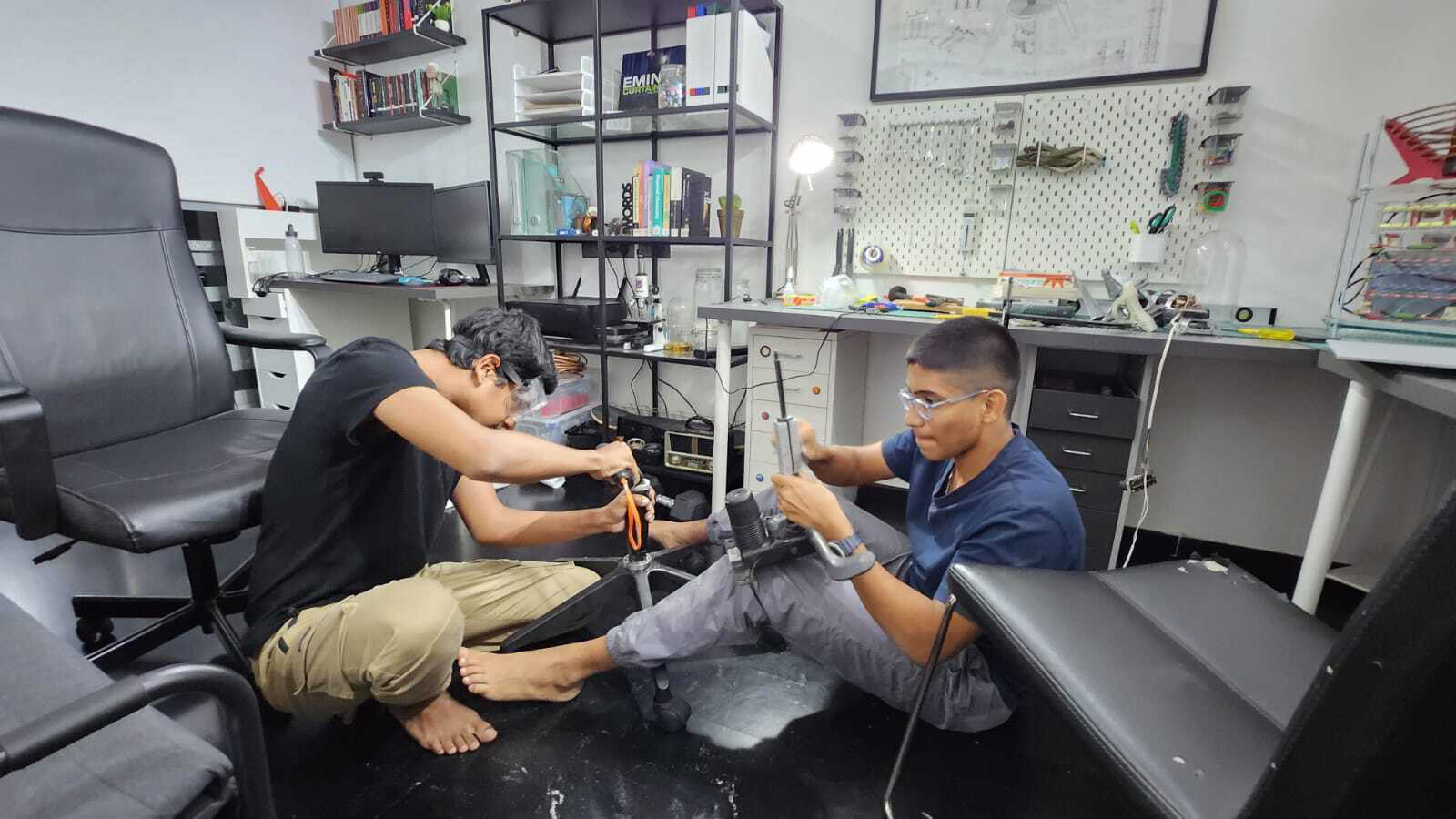
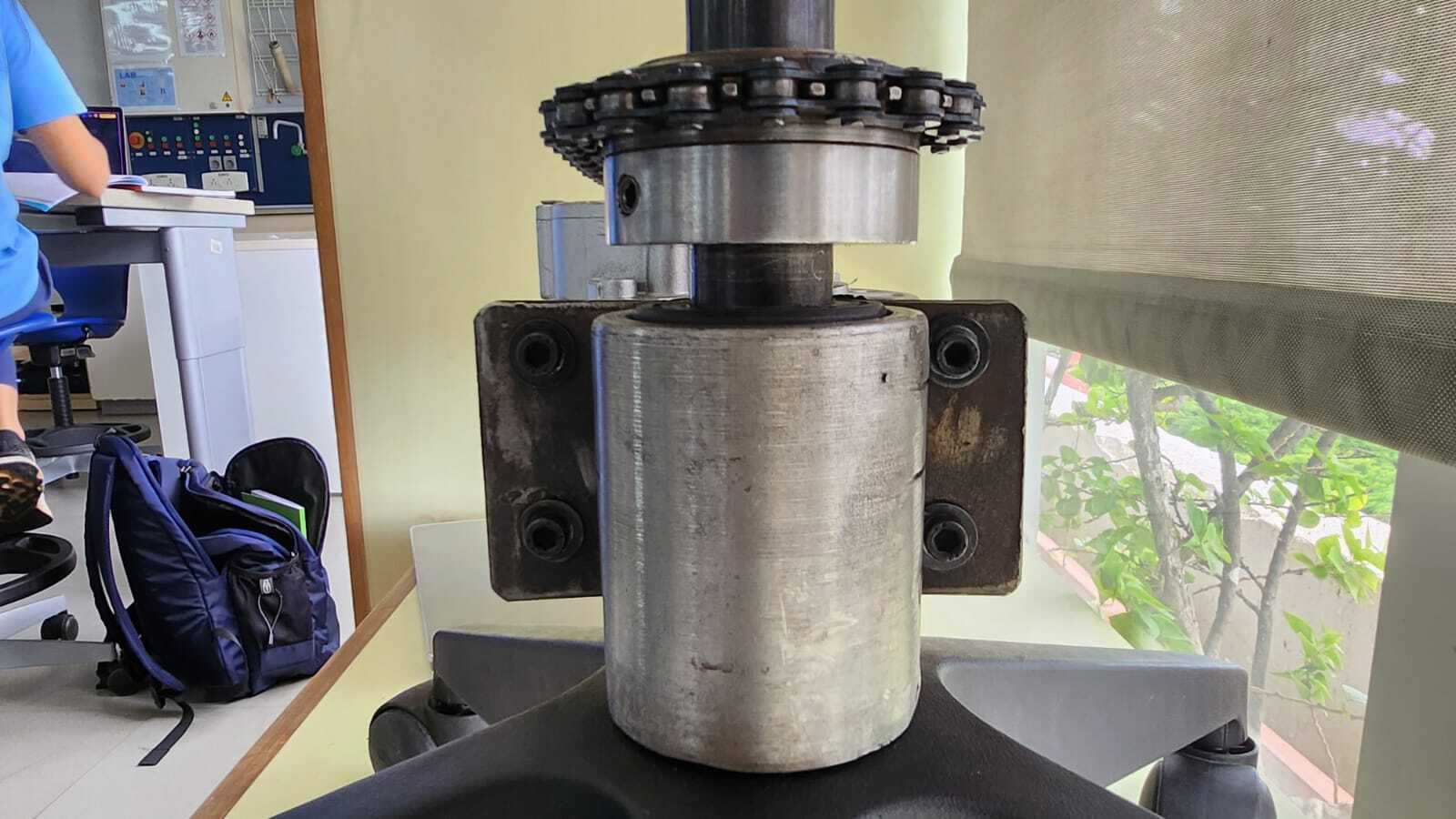
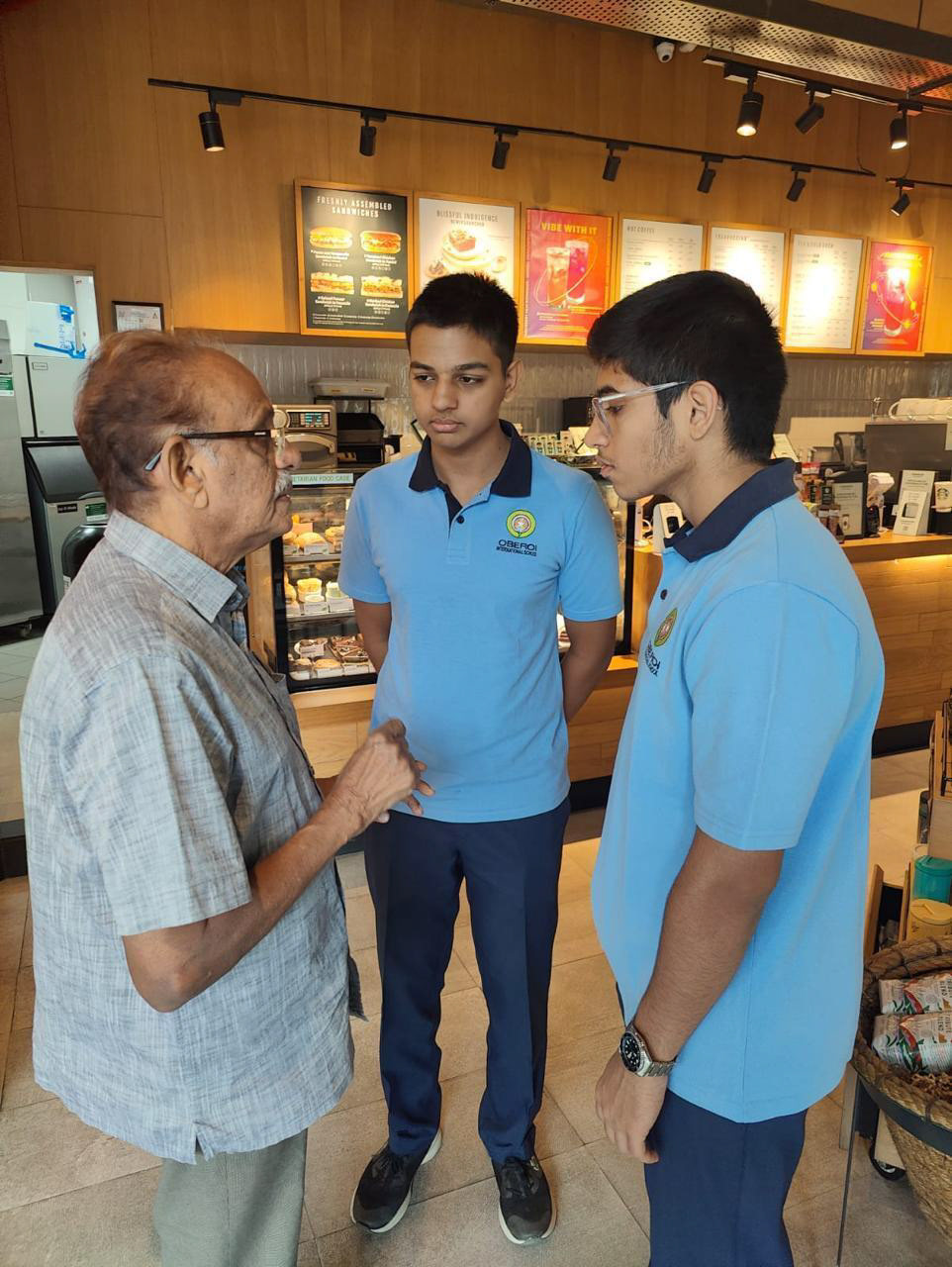
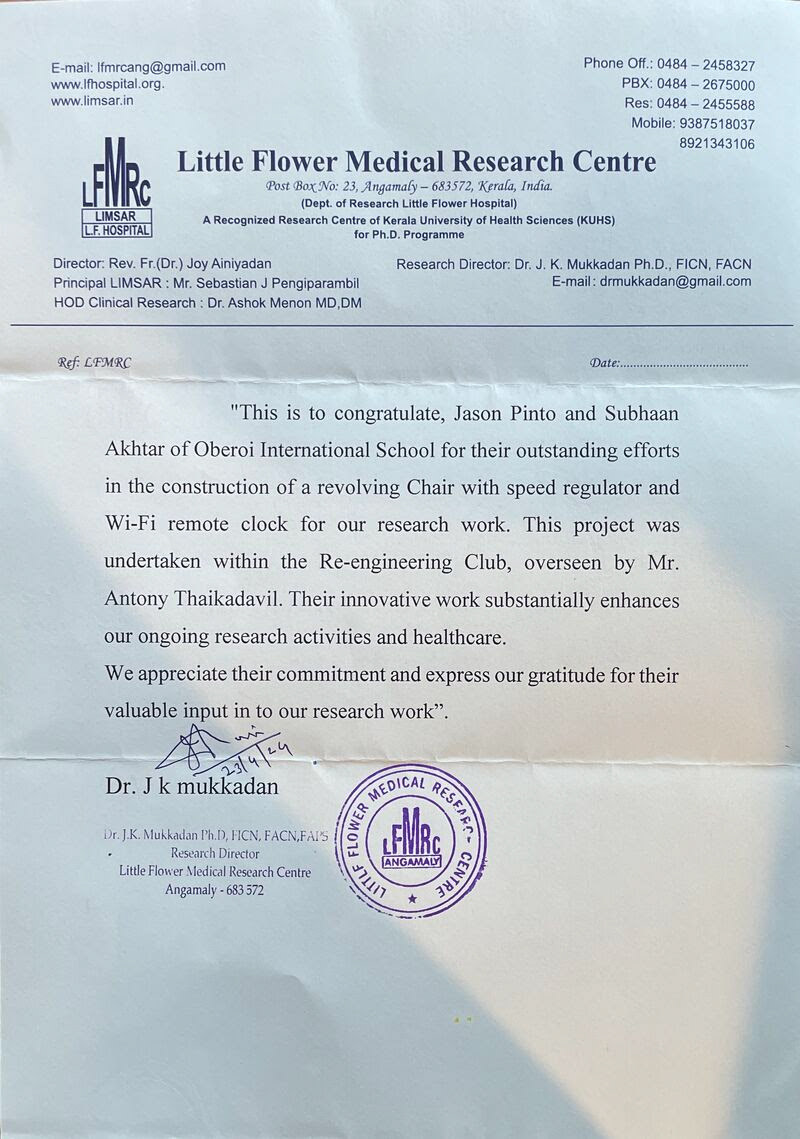