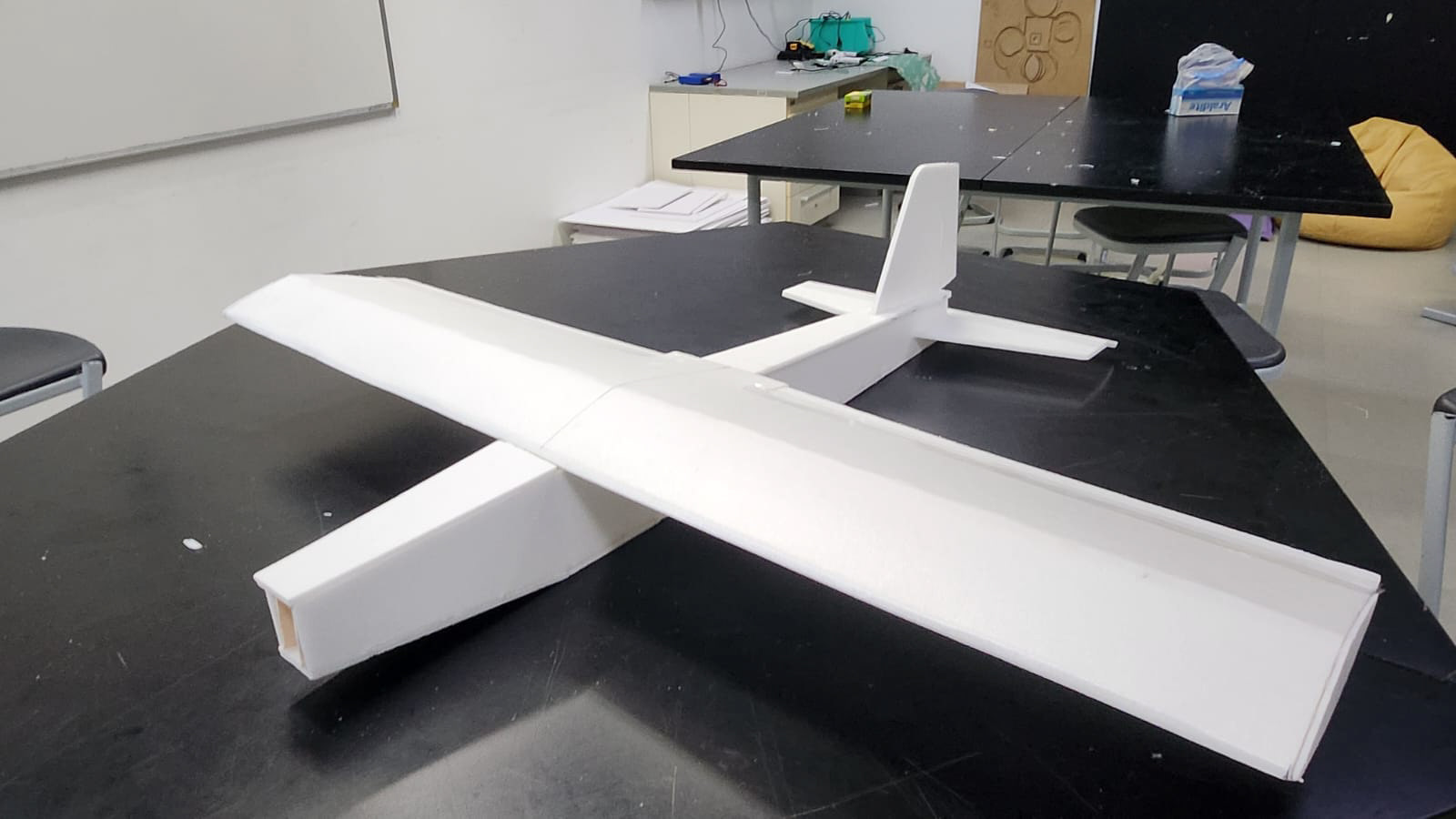
Our objective for the IIT Boeing Aeromodelling competition was to design, fabricate, and operate a radio-controlled (RC) aircraft capable of meeting specific competition criteria. The plane needed to maintain a high thrust-to-weight ratio, carry a defined payload, and remain controllable across pitch, roll, and yaw axes. We aimed to optimize aerodynamic efficiency, structural integrity, and power management to ensure stable flight and consistent performance during the three-round event.
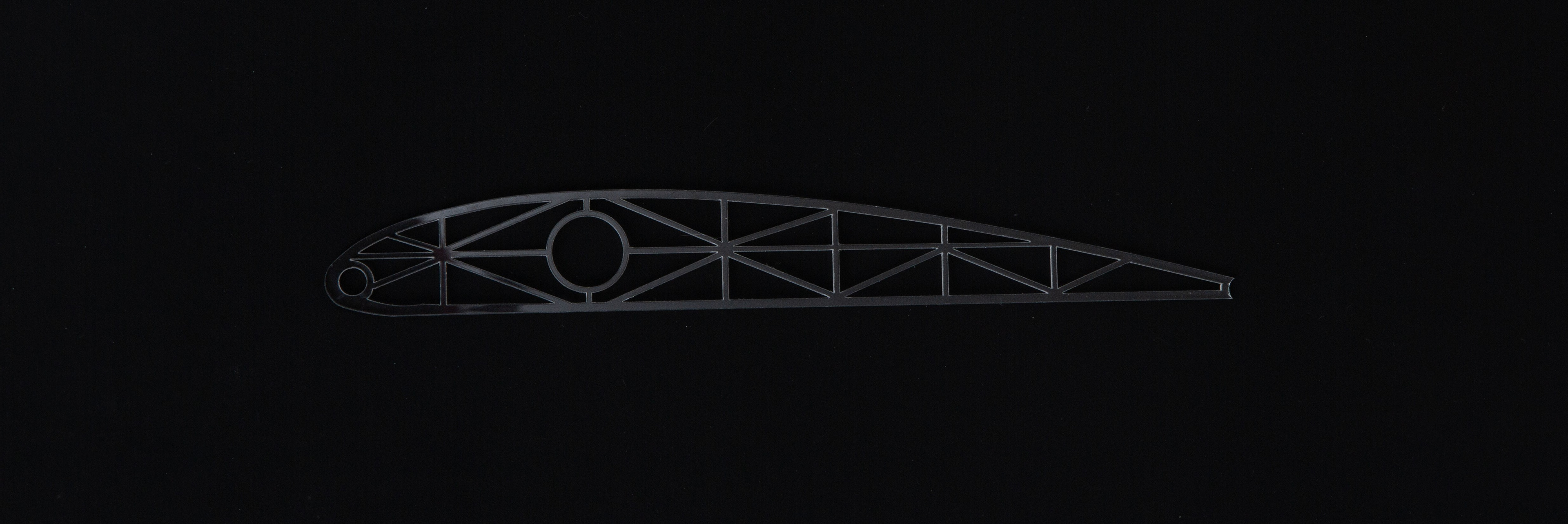
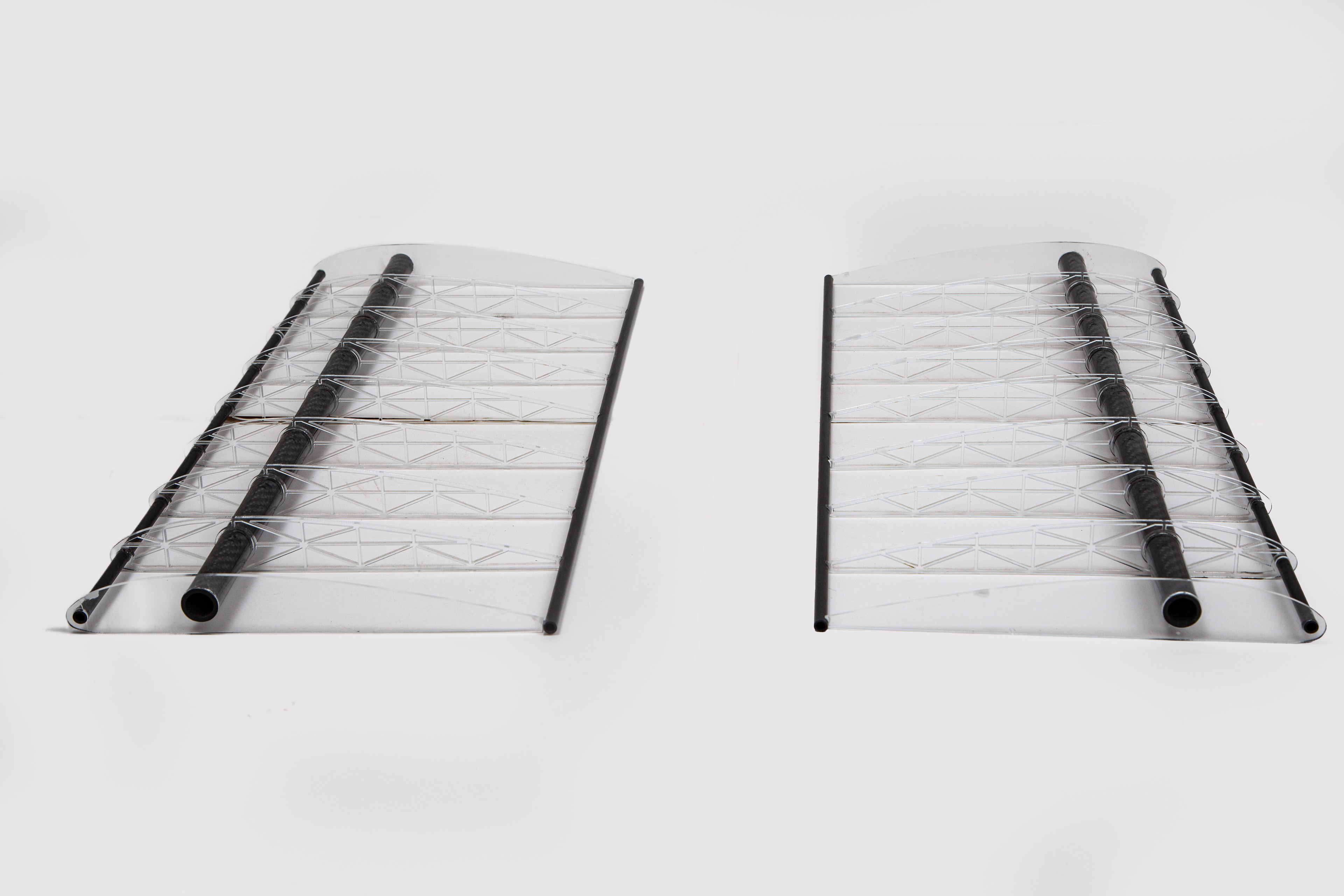
Aerodynamic Design and Structural Configuration
We selected a NACA 4412 airfoil due to its favorable lift characteristics and forgiving stall behavior under low Reynolds number conditions, typically around 100,000–200,000 for model-scale flight. The wing design incorporated a slight washout at the wingtips and smooth, low-drag surfaces to maintain controlled airflow. We fine-tuned wing incidence angles and adjusted thrust lines after initial test flights to enhance stability and performance.
The fuselage was constructed primarily from high-density EPP foam for its lightweight, durable properties and energy absorption during hard landings. Internal plywood formers (approximately 3 mm birch) provided structural rigidity for critical mounting points, such as the motor mount and wing attachment areas. The wing featured balsa wood ribs and a carbon fiber spar to minimize flex under load. At the same time, the tail surfaces integrated depron foam layered with thin carbon rods to maintain torsional stiffness.
Rubber-band-based wing mounting allowed quick adjustments and damage mitigation. We used CA hinges and careful hinge-line alignment for all control surfaces, ensuring full deflection without introducing flutter. Control linkages included metal gear micro servos (around 9g class, e.g., MG90S) with Z-bends and clevises, ensuring precise response and adjustable deflections (approximately ±15° elevator, ±20° ailerons).
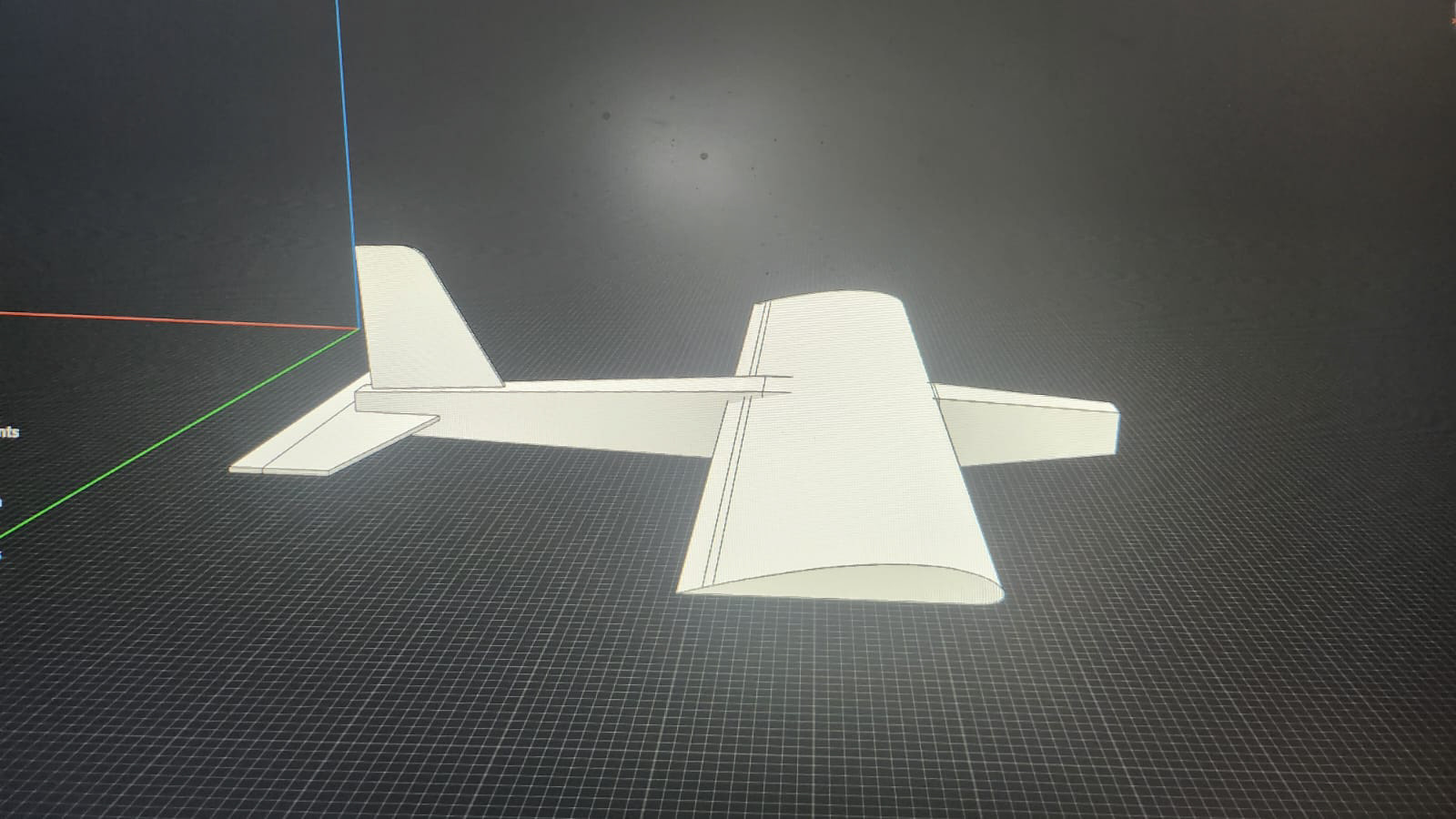
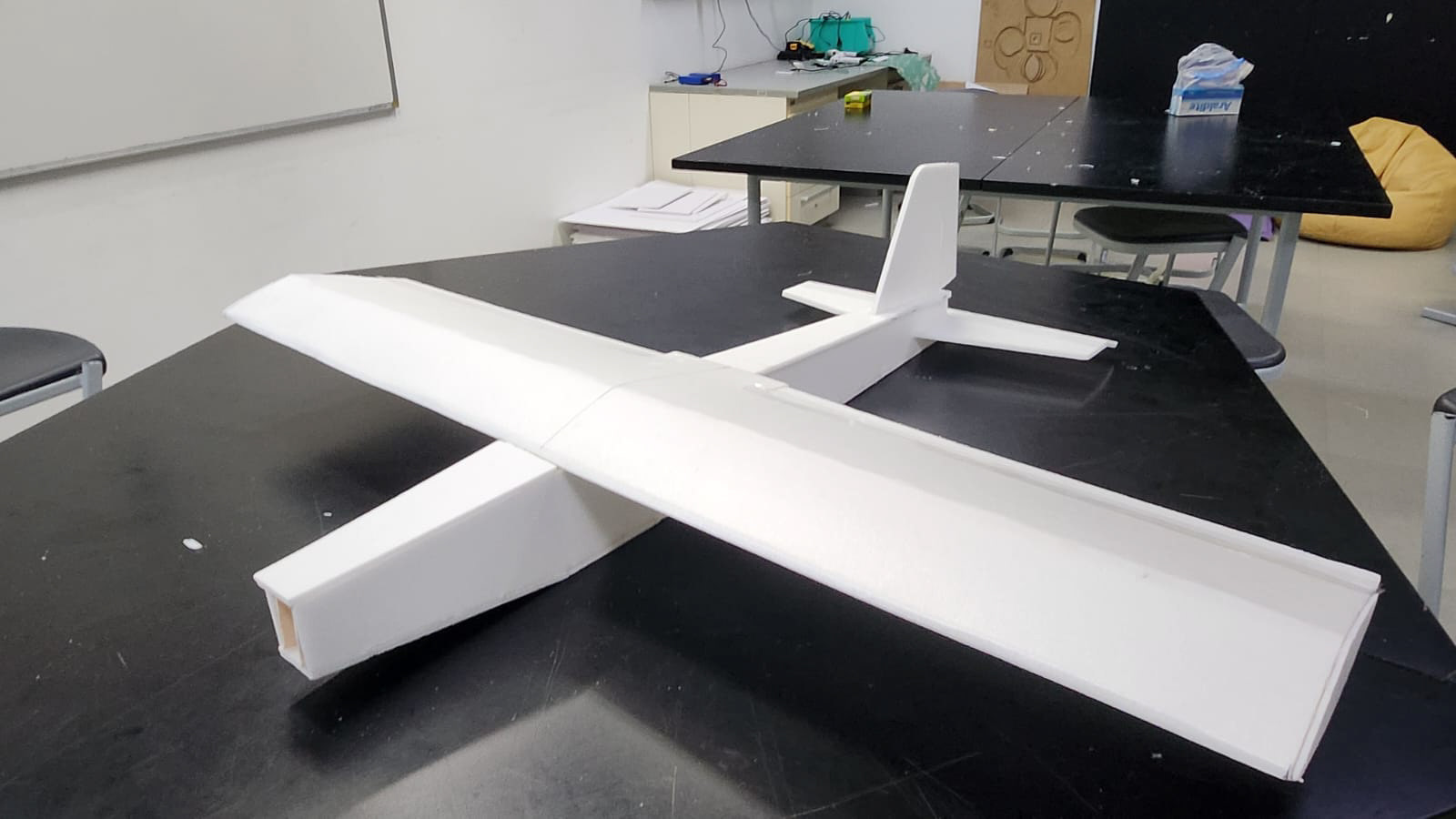
Electronics, Powertrain, and Control Integration
The powertrain comprised a 2212-size BLDC outrunner motor rated about 1000 KV, paired with a 30A ESC and running on a 3S (11.1V) 2200mAh LiPo battery. This setup offered around a 1.2:1 thrust-to-weight ratio, providing a performance margin for takeoffs, climbs, and stable cruises under payload conditions. A wattmeter verified the current draw and ensured we remained within ESC and motor limits, while a digital scale confirmed that the all-up weight aligned with our design targets.
Servo motors controlled ailerons, elevators, and payload-release hatch. Control linkages used low-friction guide tubes, and servo horns were positioned to minimize mechanical slop. Transmitter-receiver calibration ensured seamless RC input response. After initial test flights revealed a slight roll tendency and thermal issues at high throttle, we introduced a 2° proper thrust offset and limited throttle to prevent ESC overheating and foam damage.
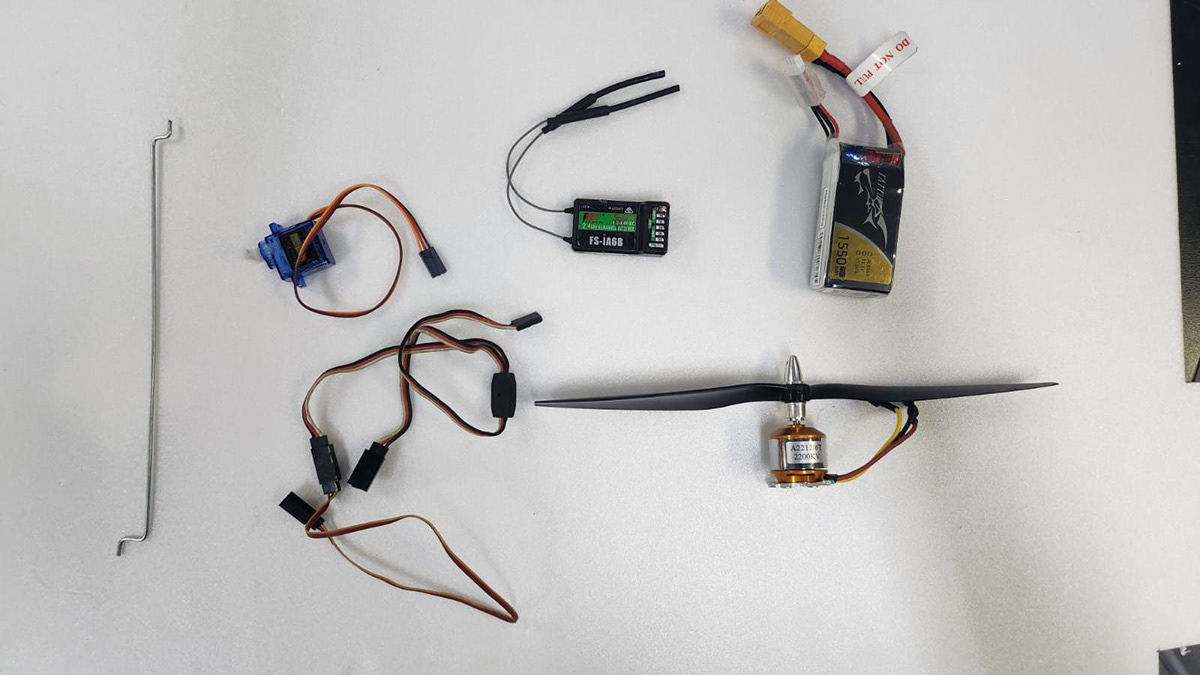
Testing and Iteration
Initial ground tests with a thrust stand confirmed motor output and power draw. Subsequent field tests, recorded on HD video, guided incremental refinements. Adjusting CG placement by shifting the battery location improved balance while fine-tuning thrust angles enhanced longitudinal stability. Repeated test flights allowed us to verify flight handling, stall characteristics, and control responsiveness under varying load conditions.
Although we did not employ advanced telemetry in this phase, combining visual footage, structural inspections, and iterative adjustments to geometry, thrust angle, and servo endpoints steadily improved flight quality. Our testing approach balanced simplicity and reliability, ensuring incremental performance gains before competition day.
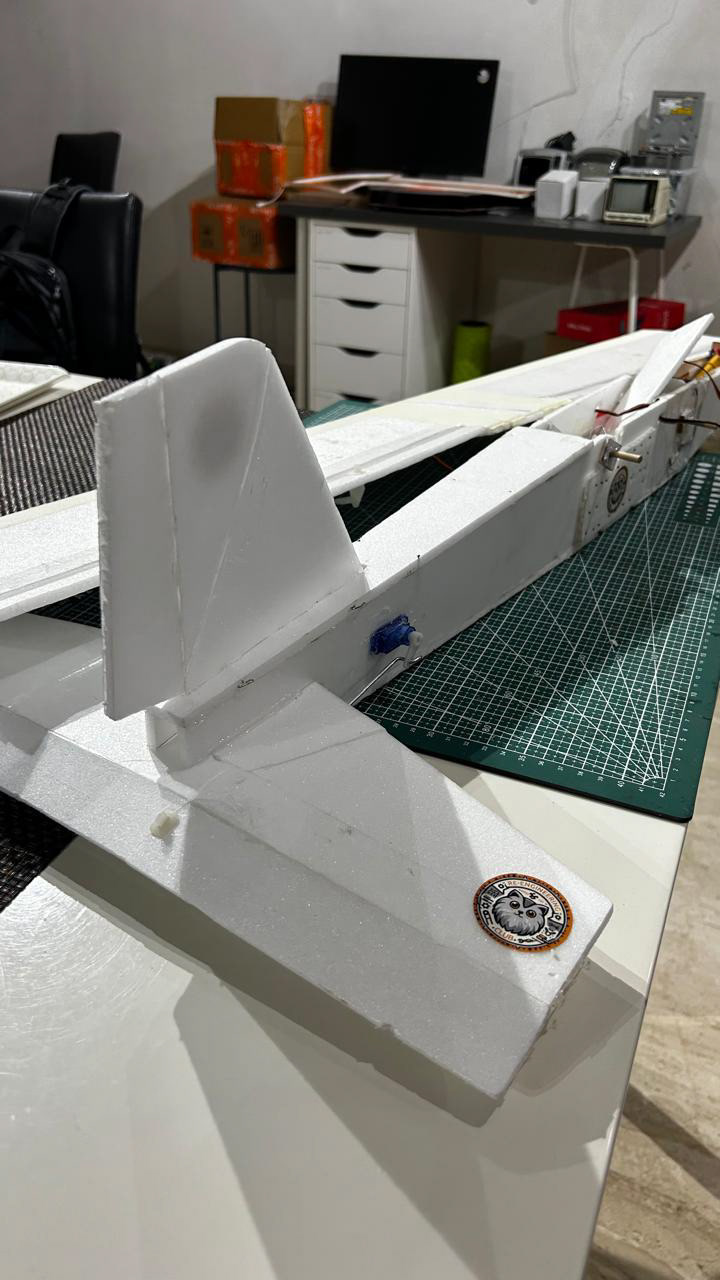
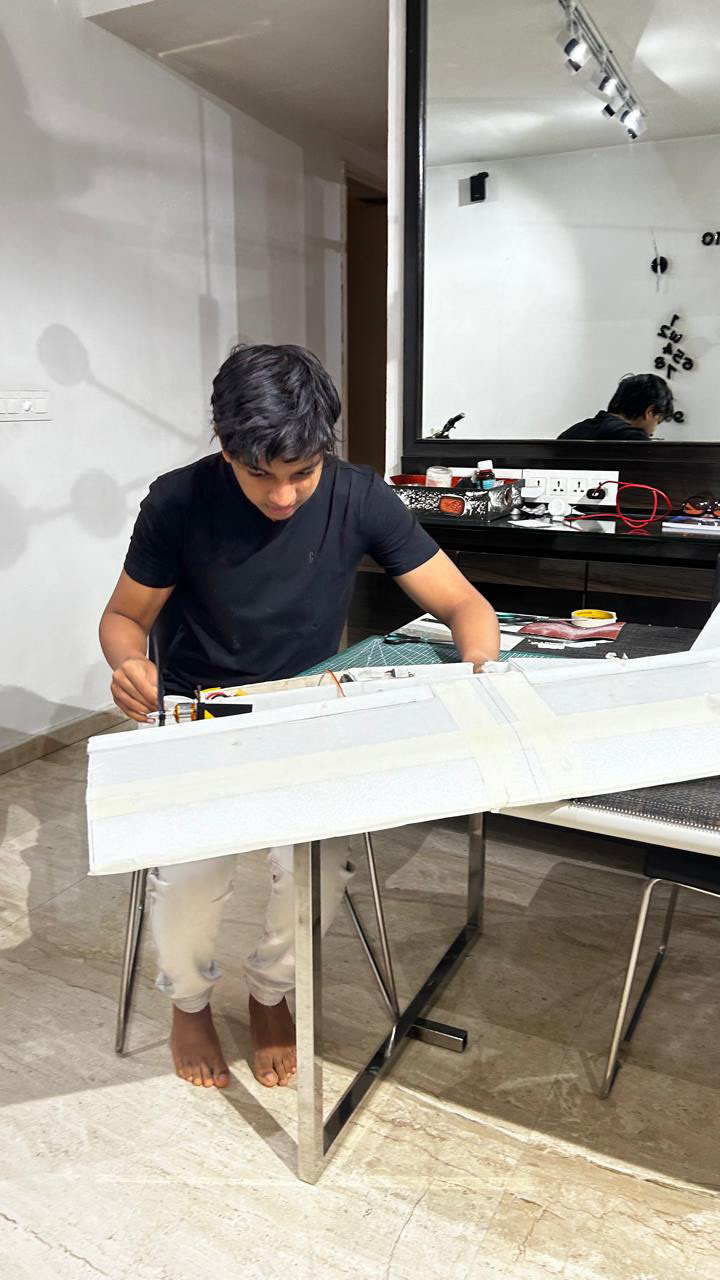
Designing, assembling, and testing this RC aircraft demanded substantial technical skills, including aerodynamic profiling, structural engineering, materials selection, and electronics integration. Beyond the technical dimension, this experience also required effective team collaboration, careful project management, and resilience in the face of setbacks. We learned the importance of iterative testing, data-driven improvements, and strategic adaptation under competition constraints. While the final competition outcome challenged our expectations, it ultimately reinforced our understanding that engineering success relies as much on persistent problem-solving and teamwork as it does on sound technical principles.
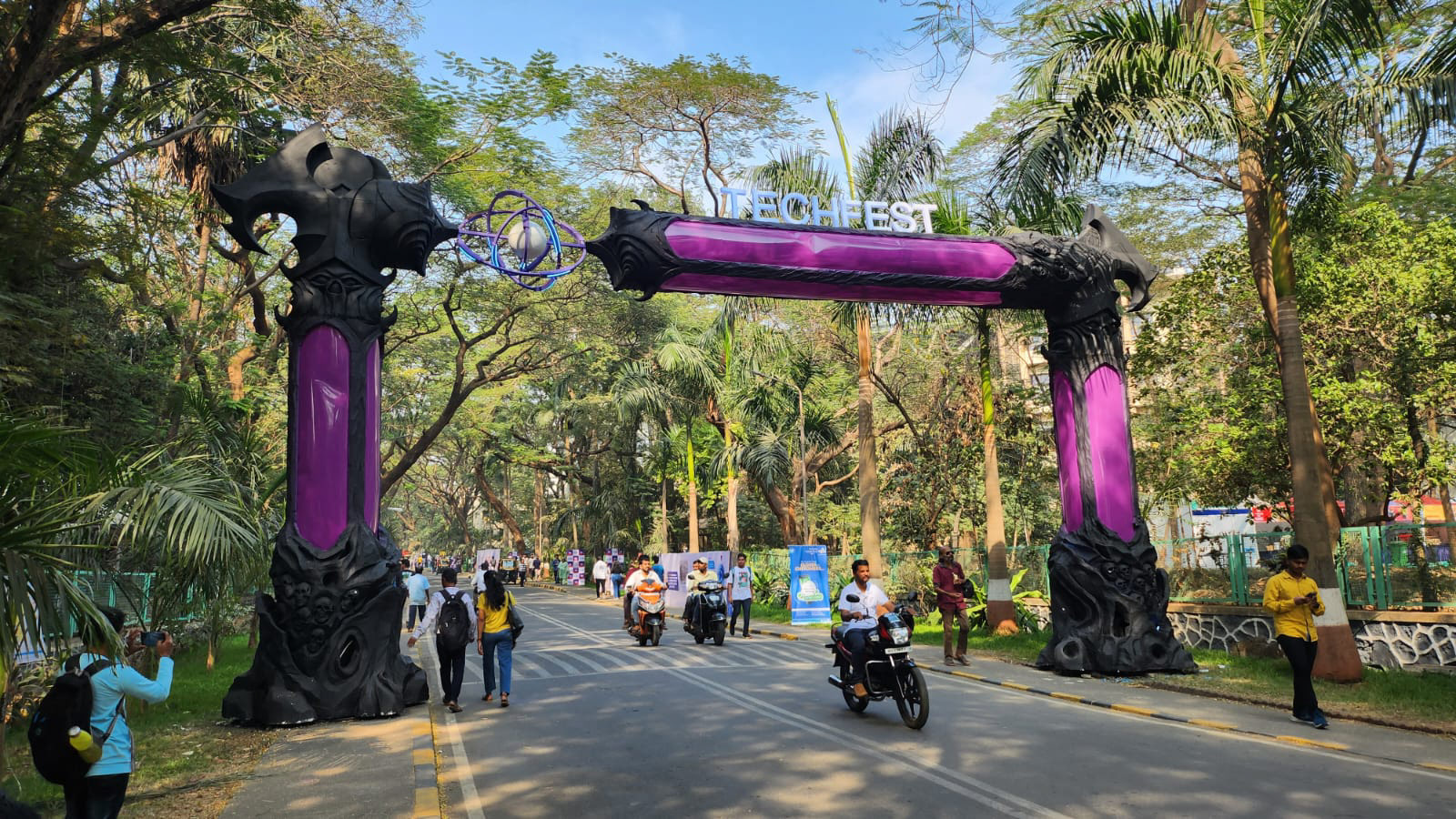
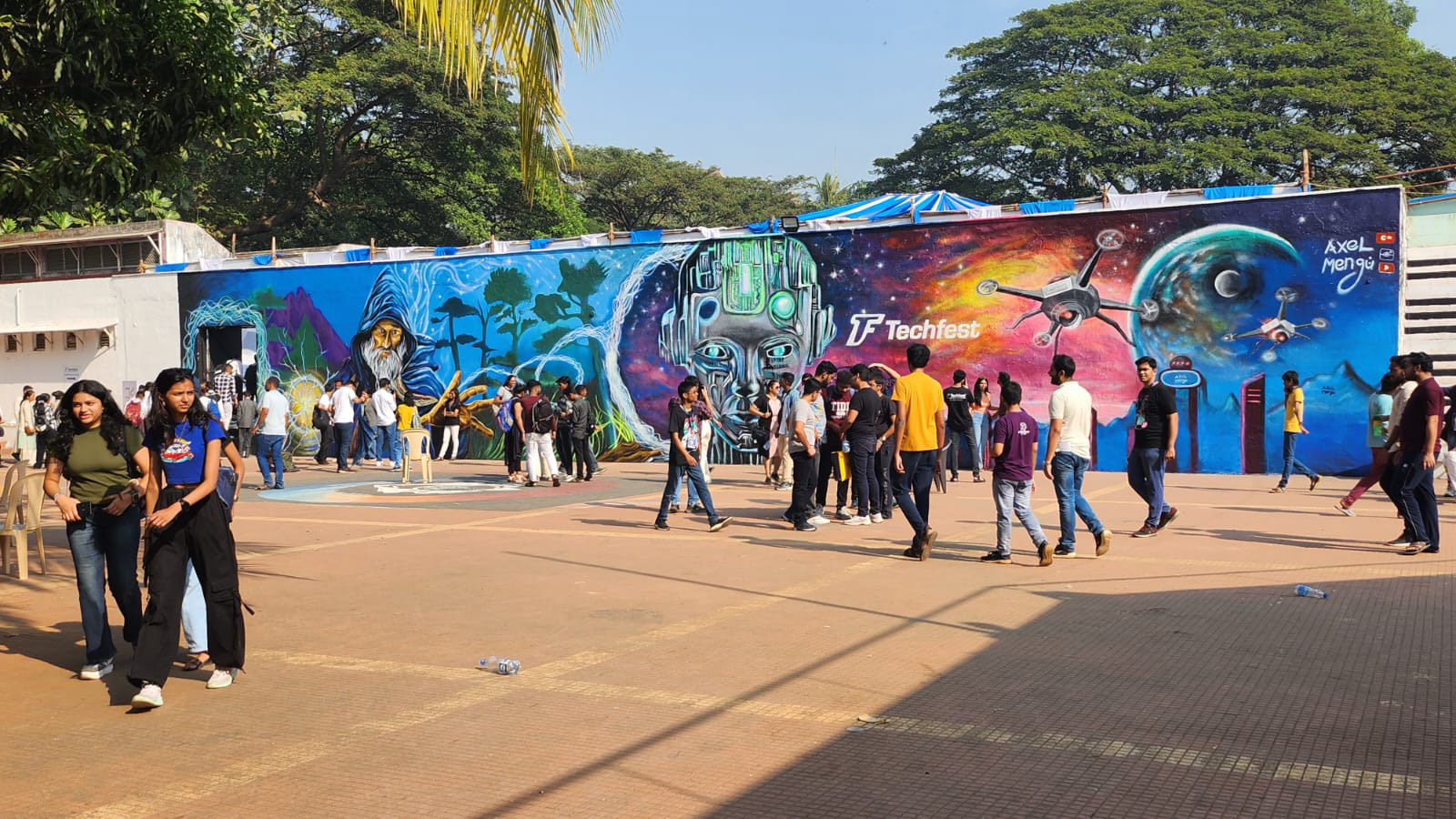
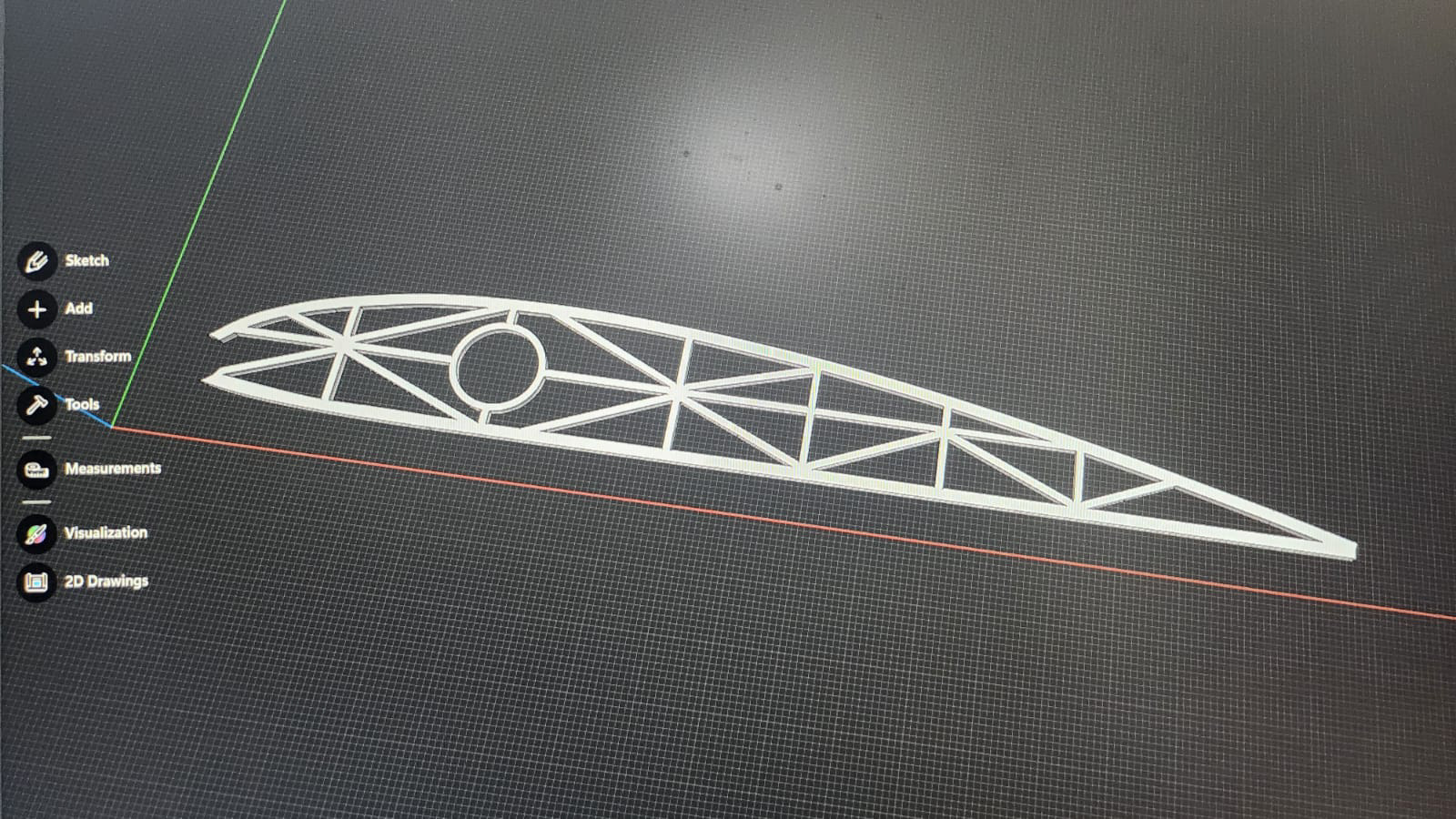
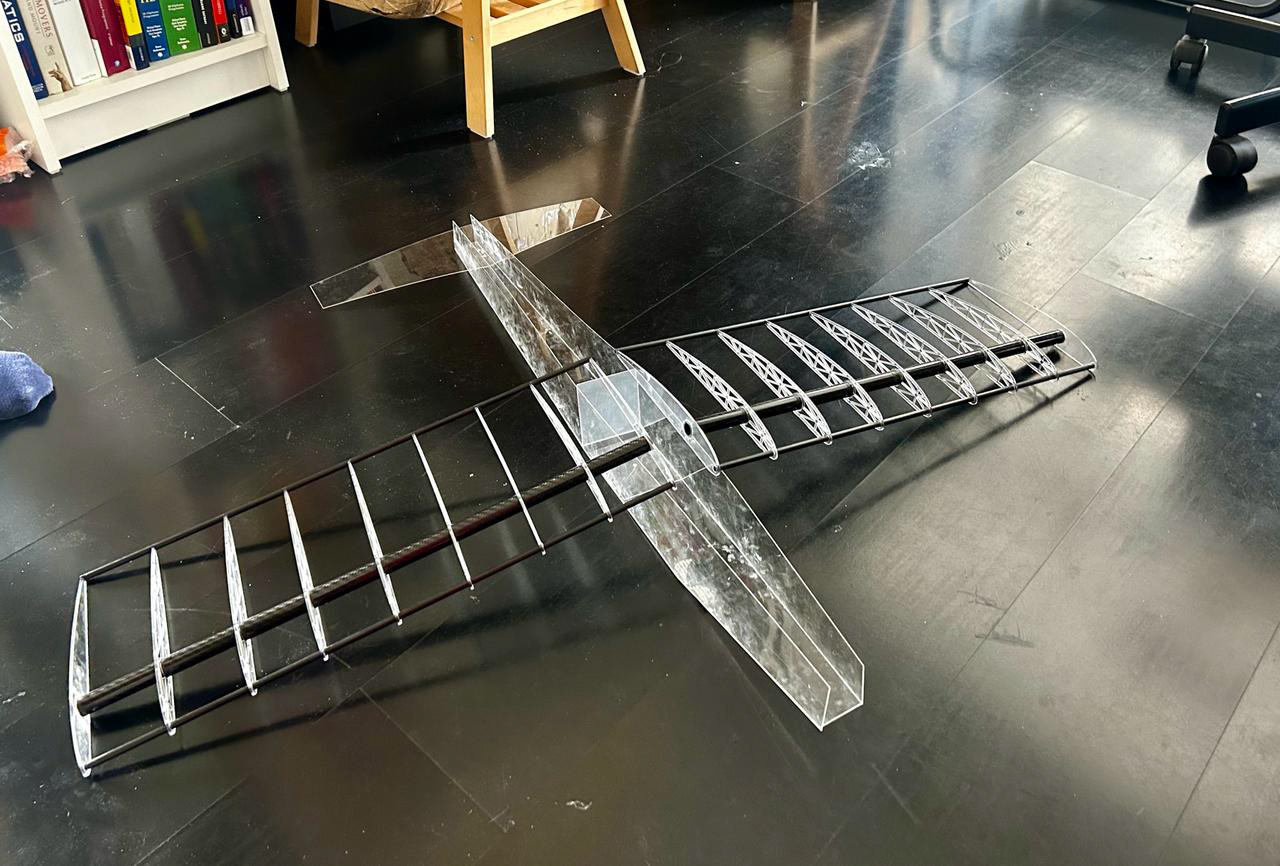