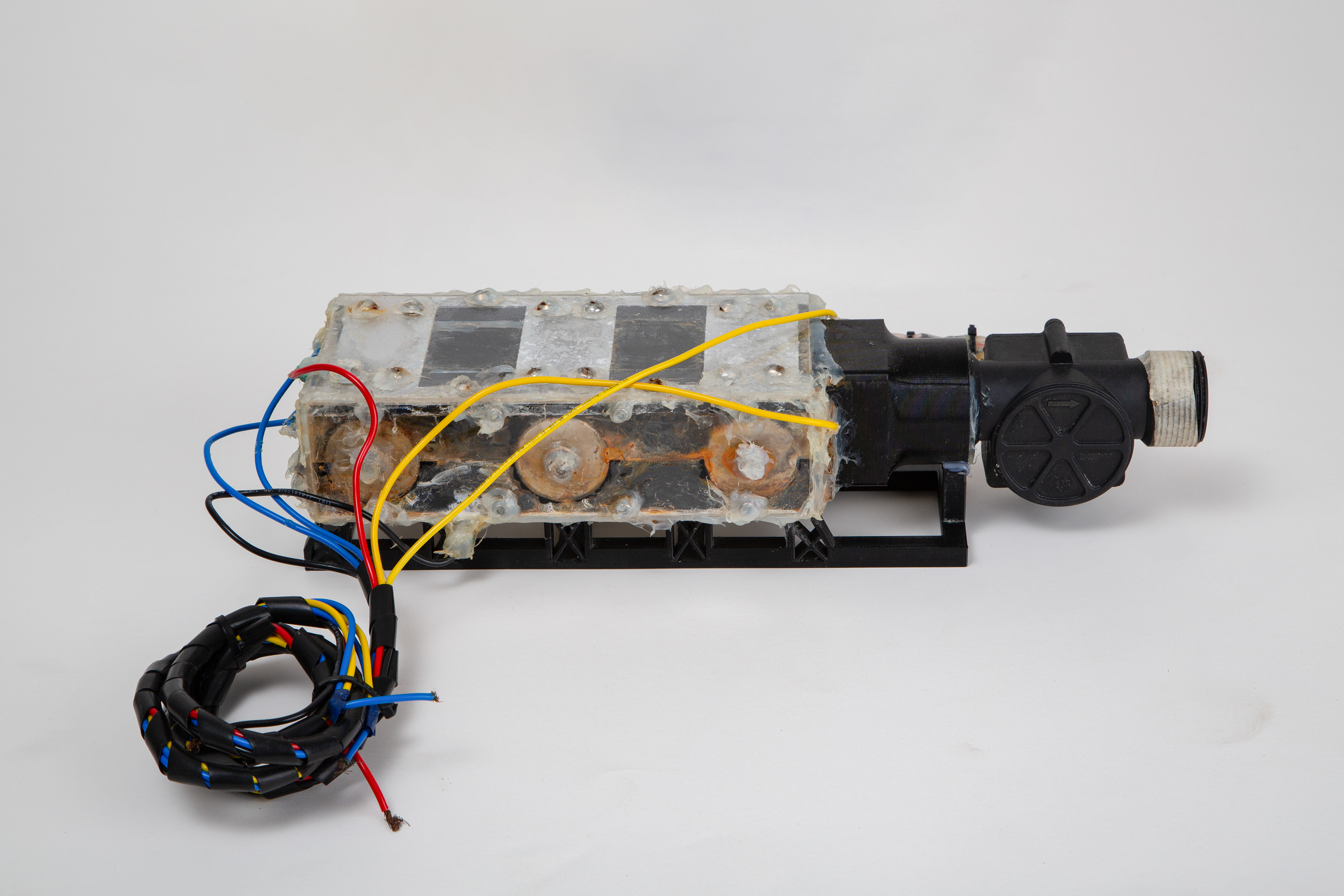
I developed a magnetohydrodynamic (MHD) thruster designed to generate fluid flow without moving parts, relying solely on the interaction of electric and magnetic fields. The device’s core objective was to induce measurable liquid motion in a conductive medium, such as salt water, under controlled laboratory conditions. Meeting this goal required careful attention to electrode configuration, magnetic field generation, fluid conductivity, and data acquisition. Initial prototypes and iterative testing cycles guided refinements in materials, assembly techniques, and operational parameters to improve overall system performance.
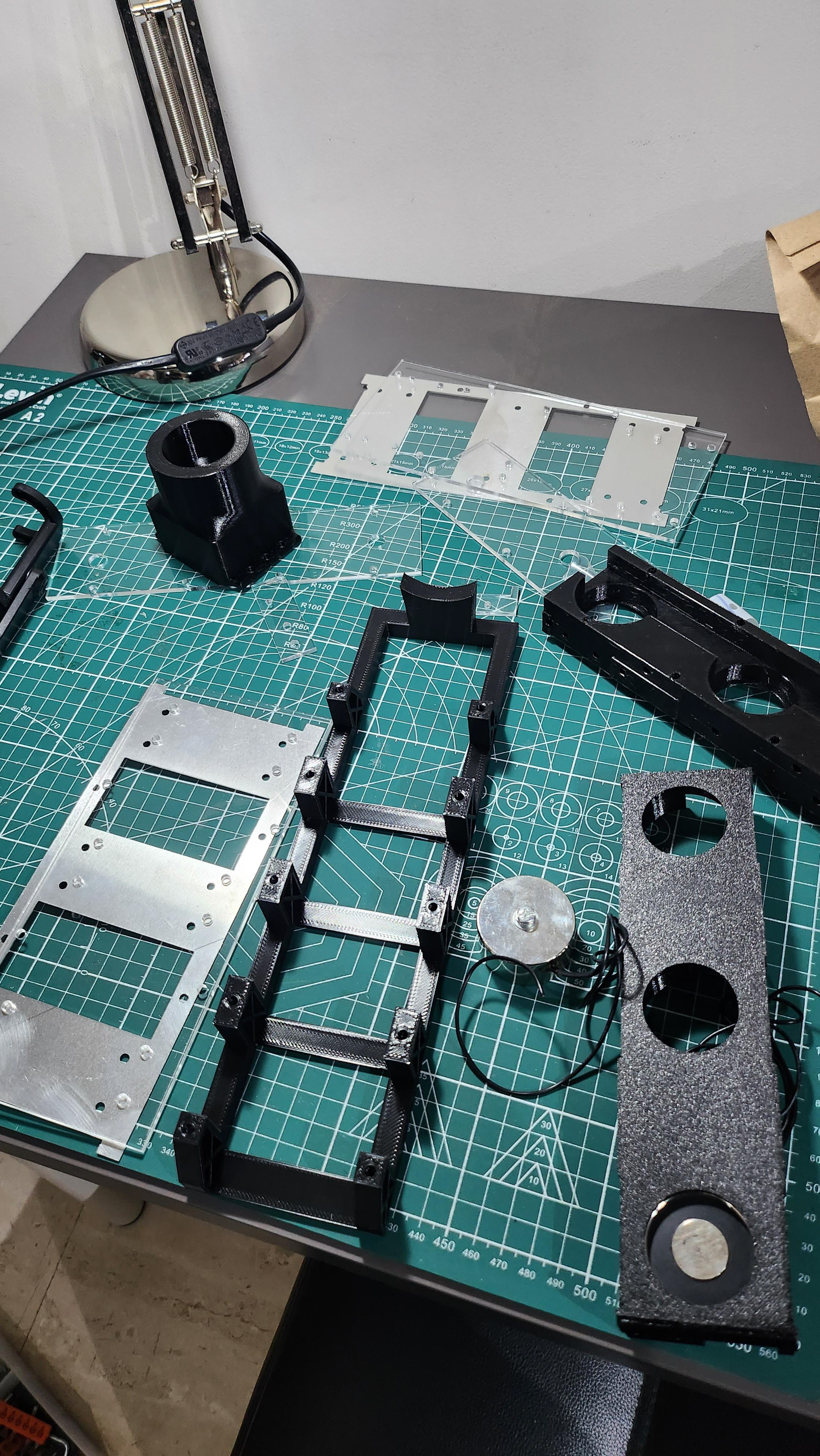
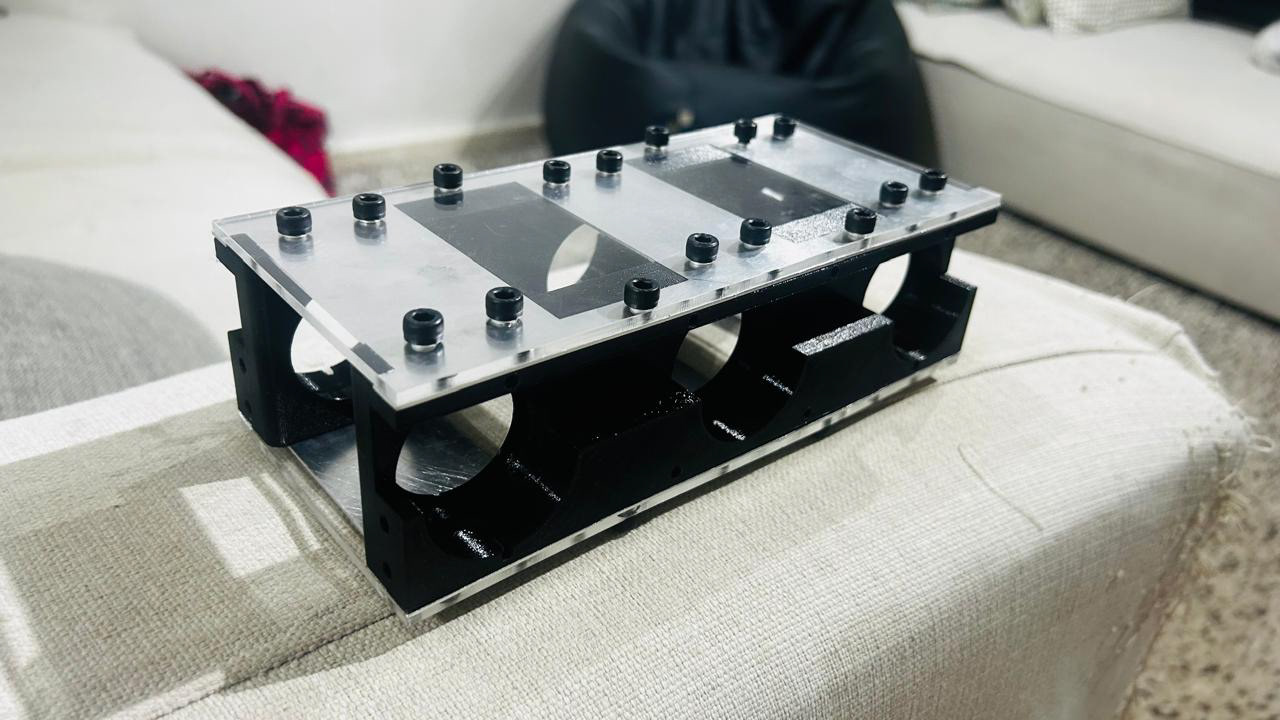
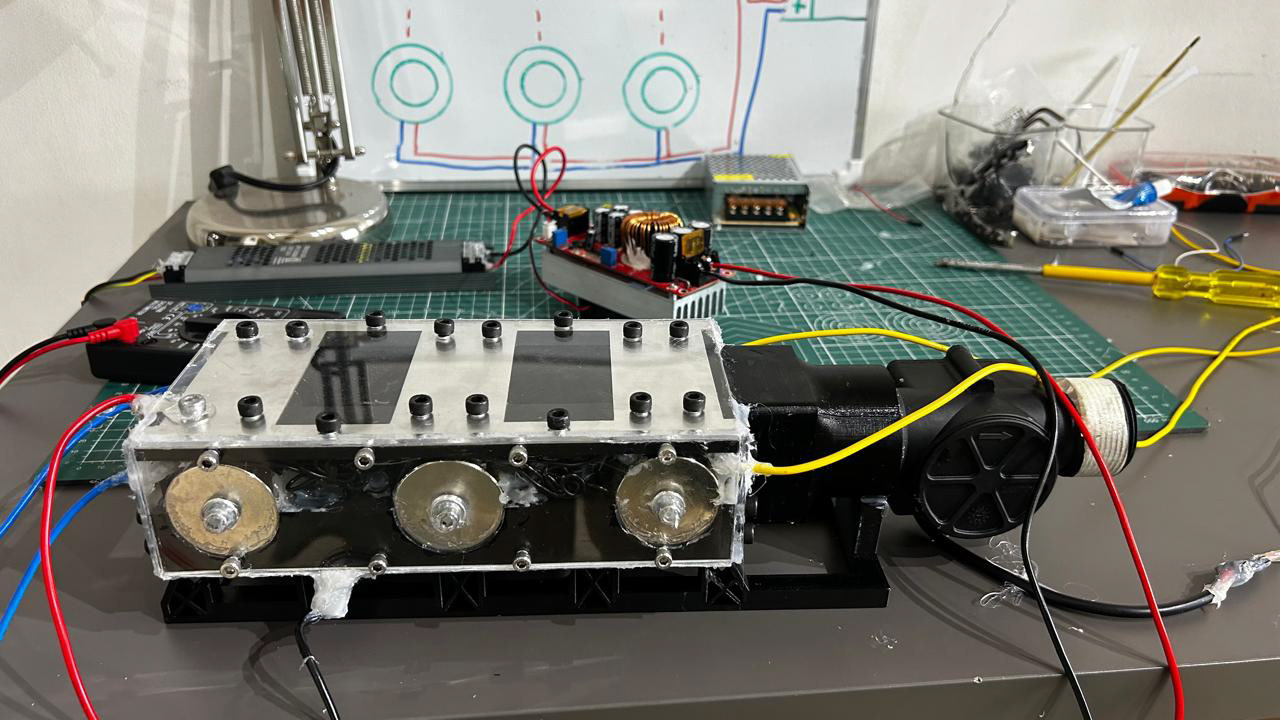
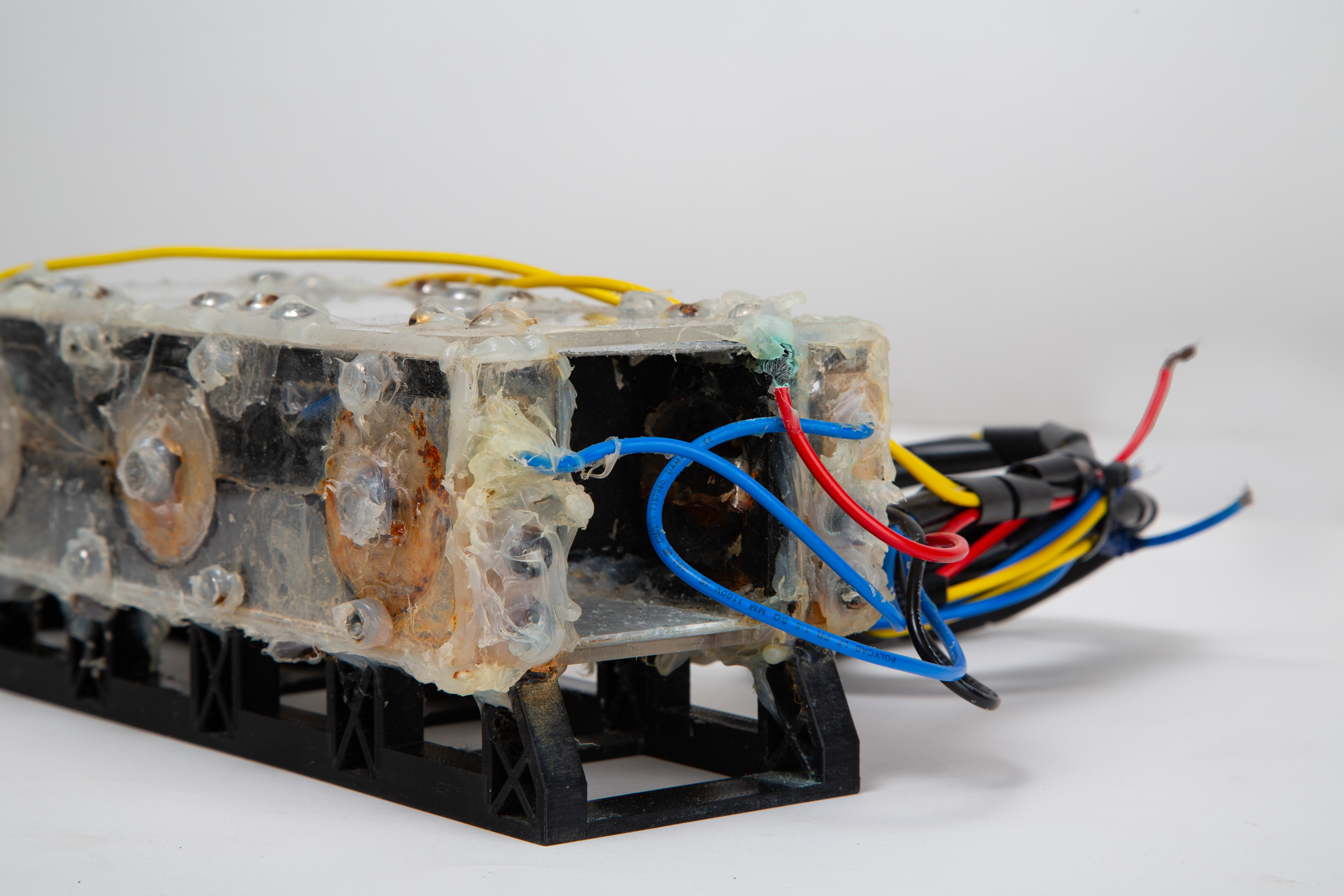
Channel Geometry and Electrode Arrangement
The thruster’s primary flow channel measured approximately 50 x 52 cm, with an additional 50 cm of lateral space on each side to accommodate electromagnet assemblies. Electrodes fabricated from corrosion-resistant, non-ferromagnetic metals were mounted along the interior walls to maintain uniform current distribution across the fluid. These electrodes were sealed with silicone and acrylic interfaces, preventing leaks and ensuring stable electrical connectivity. Parallel electrode configurations, rather than single large plates, proved more efficient at distributing current and reducing localized polarization effects. Adjustments to electrode spacing were informed by early trials, during which improper alignment led to erratic field conditions and reduced thrust generation.
Magnetic Field Generation and Coil Integration
Achieving the necessary magnetic field strength presented a key engineering challenge. Initial attempts with neodymium permanent magnets demonstrated insufficient flux density, prompting the integration of custom electromagnets. W wound with copper wire selected for appropriate gauge and current capacity, these coils were arranged around the channel’s perimeter. Wiring coils on the same side in parallel and opposing pairs in series made obtaining more uniform and tunable field configurations possible. The assembly was housed within a robust support structure, accommodating thermal expansion and ensuring reliable insulation under elevated current loads. Although precise Gauss readings were unavailable, incremental testing and literature benchmarks guided the electromagnet’s design to approach field strengths necessary for noticeable MHD effects.
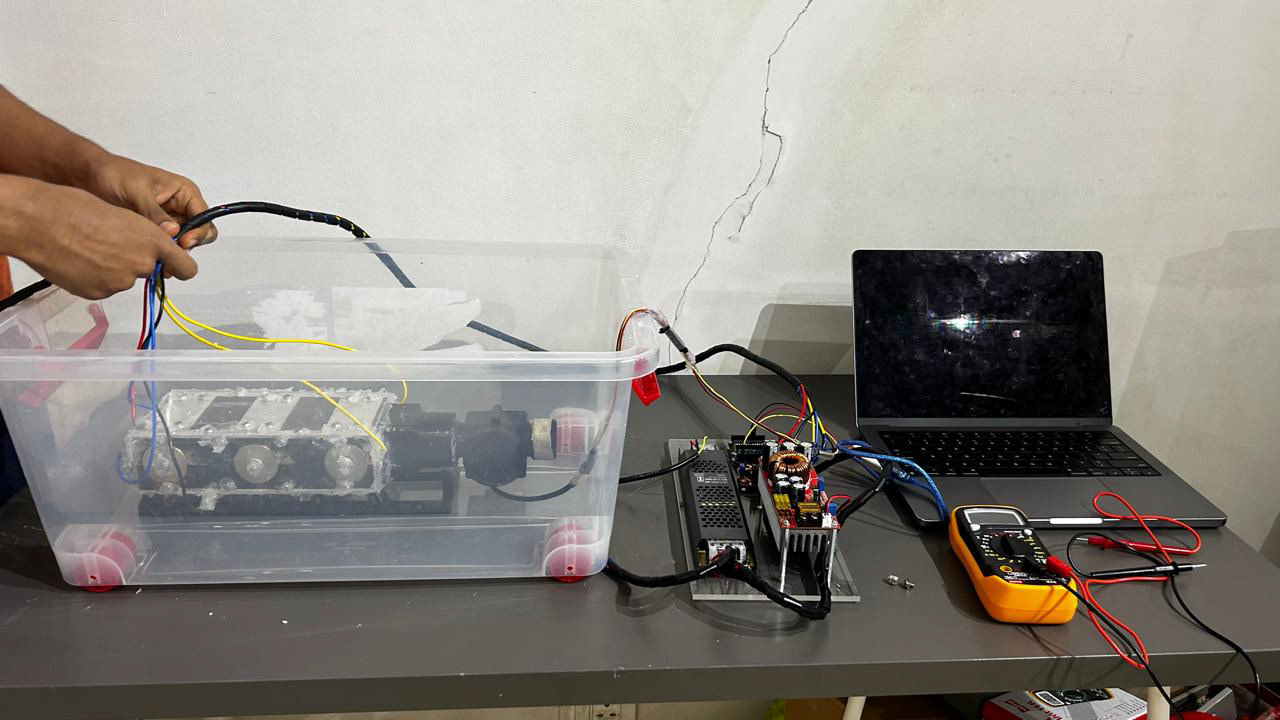
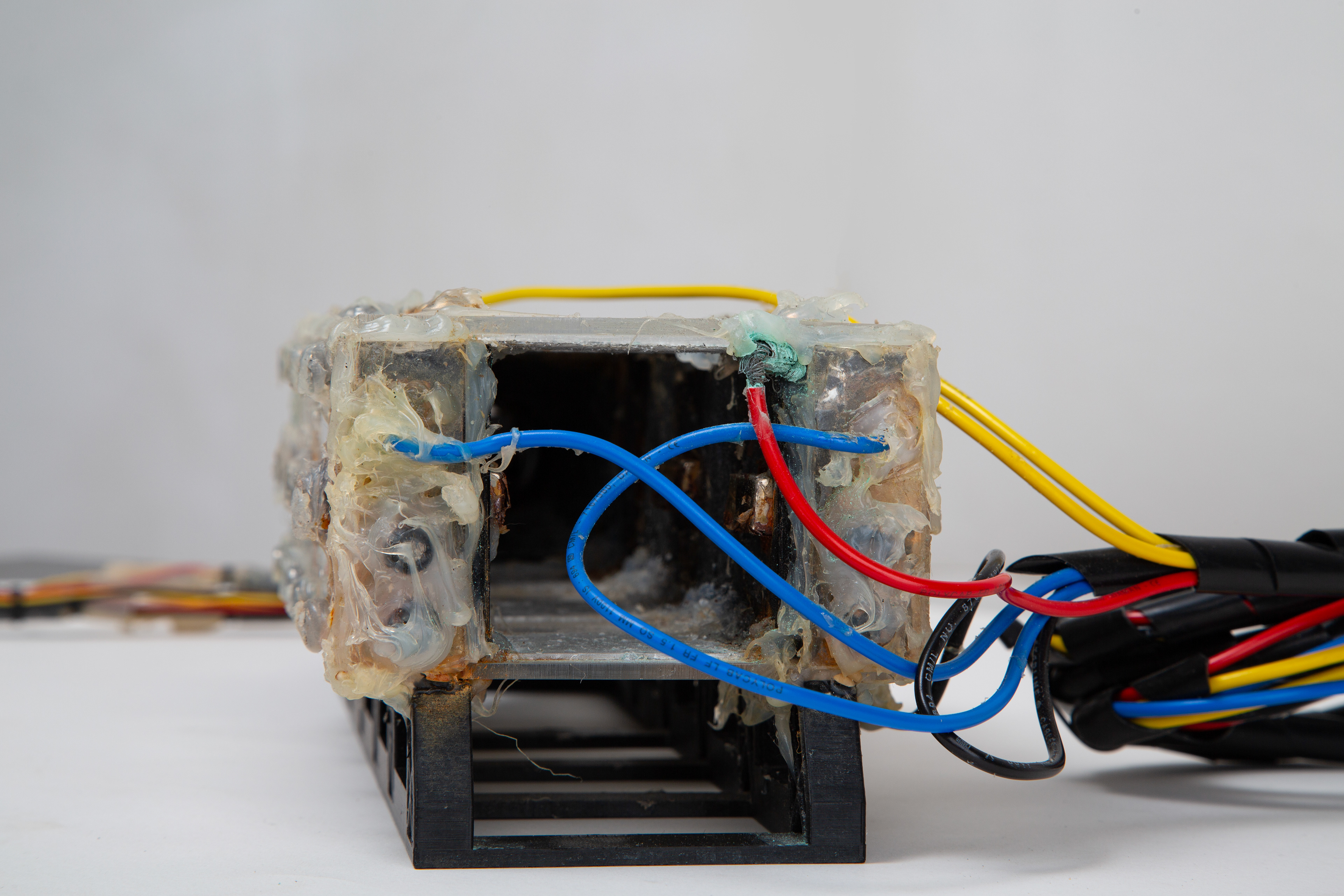
Power Supplies and Electrical Safety
Separate DC sources powered the electrodes and electromagnets. This arrangement allowed independent optimization of current and voltage levels for each subsystem. Wiring strategies were devised to prevent accidental short circuits, especially after early tests revealed that conductive fragments or misaligned magnets could create unintended current paths. Proper strain relief, sealed junction points, and careful cable management mitigated these risks. The electrode supply was chosen to support adjustable output voltages, accommodating varying salinity levels. The electromagnet supply delivered stable current to drive the coils at higher loads for short durations, enabling brief tests at elevated field strengths.
Fluid Conductivity and Flow Measurement
Saltwater functioned as the working fluid, with salinity levels tuned to achieve the desired conductivity. Adjusting ion concentration significantly influenced current density and, by extension, thrust potential. Higher conductivity increased current flow but accelerated electrode corrosion and altered fluid properties over repeated trials. A flow meter, integrated downstream and connected to an Arduino-based data acquisition system, provided quantitative insight into fluid velocity. The meter’s operational threshold guided the selection of operating conditions to ensure detectable flow rates. At the same time, the flow meter’s range was limited, and consistent calibration and resistor tuning improved measurement accuracy. Slow-motion video recordings supplemented these readings, offering visual evidence of bubble trajectories and subtle fluid disturbances.
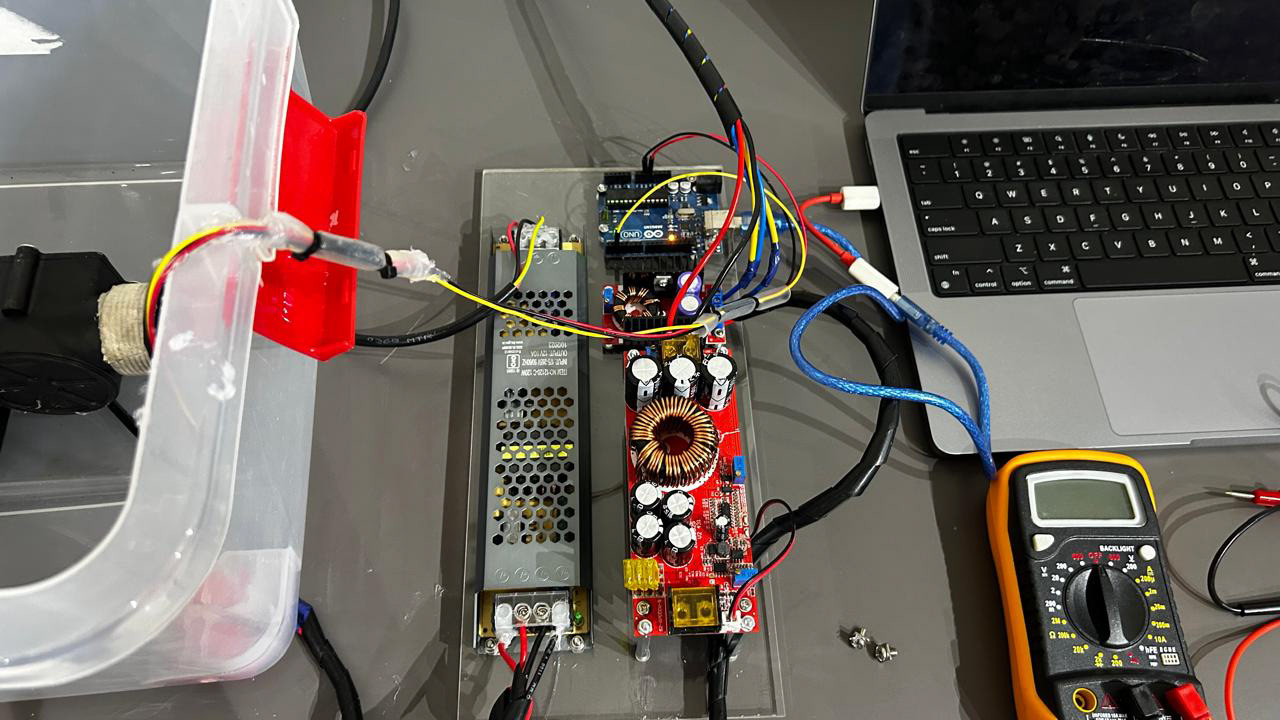
Performance Evaluation and Iterative Refinement
Initial tests focused on essential electrode operation and confirmed electrolysis effects, evidenced by hydrogen bubble formation. Subsequent runs introduced the electromagnets, resulting in a modest but discernible fluid motion. Although the induced flow velocities were often minimal, each iteration clarified dependencies between electrode spacing, field strength, and fluid conductivity. Fine-tuning chain-of-custody measures—such as applying foam board plates to guide fluid paths or adjusting the coil drive currents—yielded incremental performance gains. The testing sequence validated the underlying principles of MHD propulsion while underscoring the complexity of achieving robust, measurable thrust in a laboratory-scale apparatus.
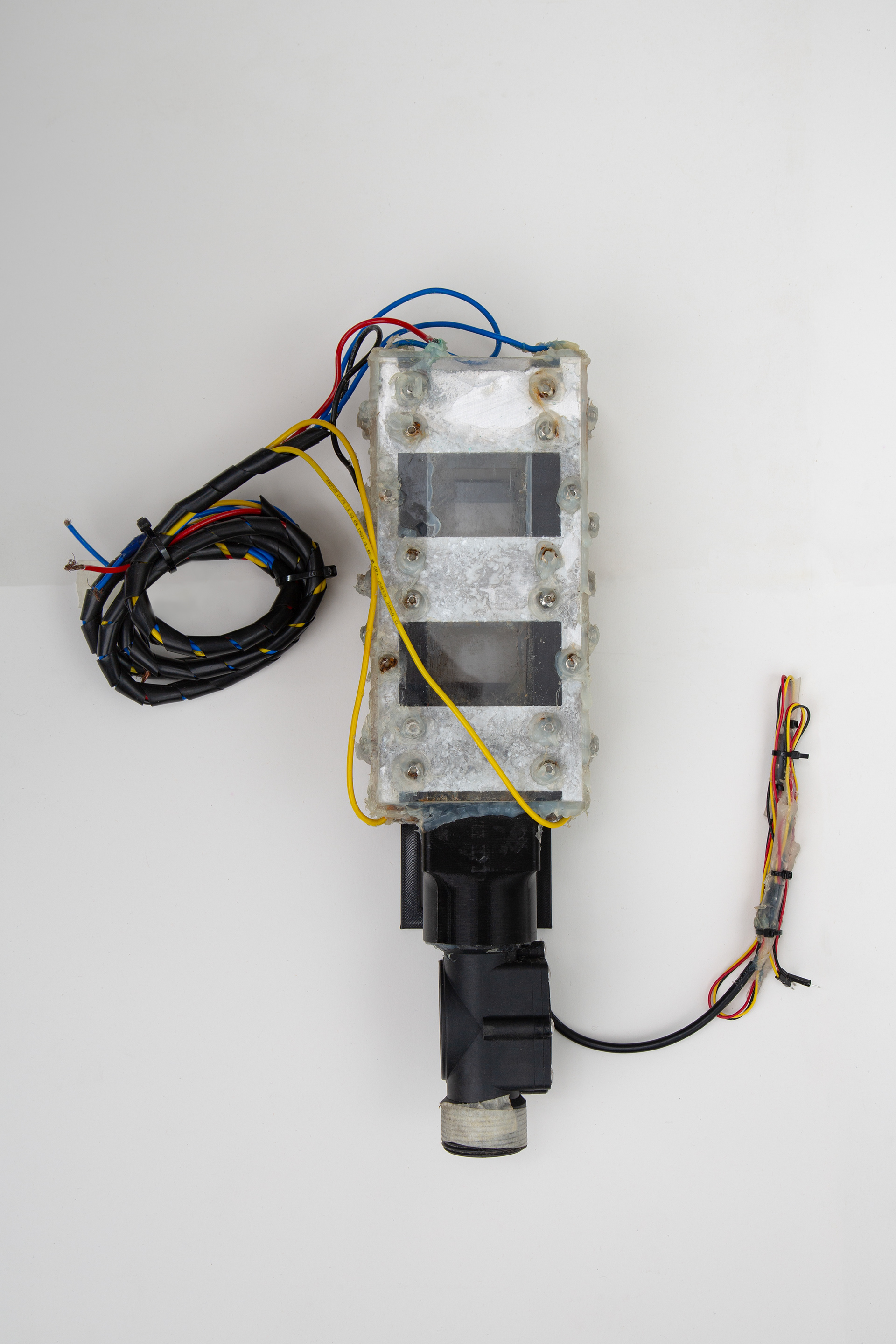
In developing and testing this MHD thruster, I navigated a broad set of engineering variables: electrode geometry, magnetic coil design, fluid conductivity, and instrumentation techniques. This experience reinforced the importance of systematic testing, careful material selection, and stringent quality control measures. Future work may involve stronger magnetic fields, more sophisticated sensors, or computational modeling to guide design improvements. By refining these parameters, subsequent designs stand to achieve more excellent stability, enhanced efficiency, and a deeper understanding of MHD propulsion’s practical potential.
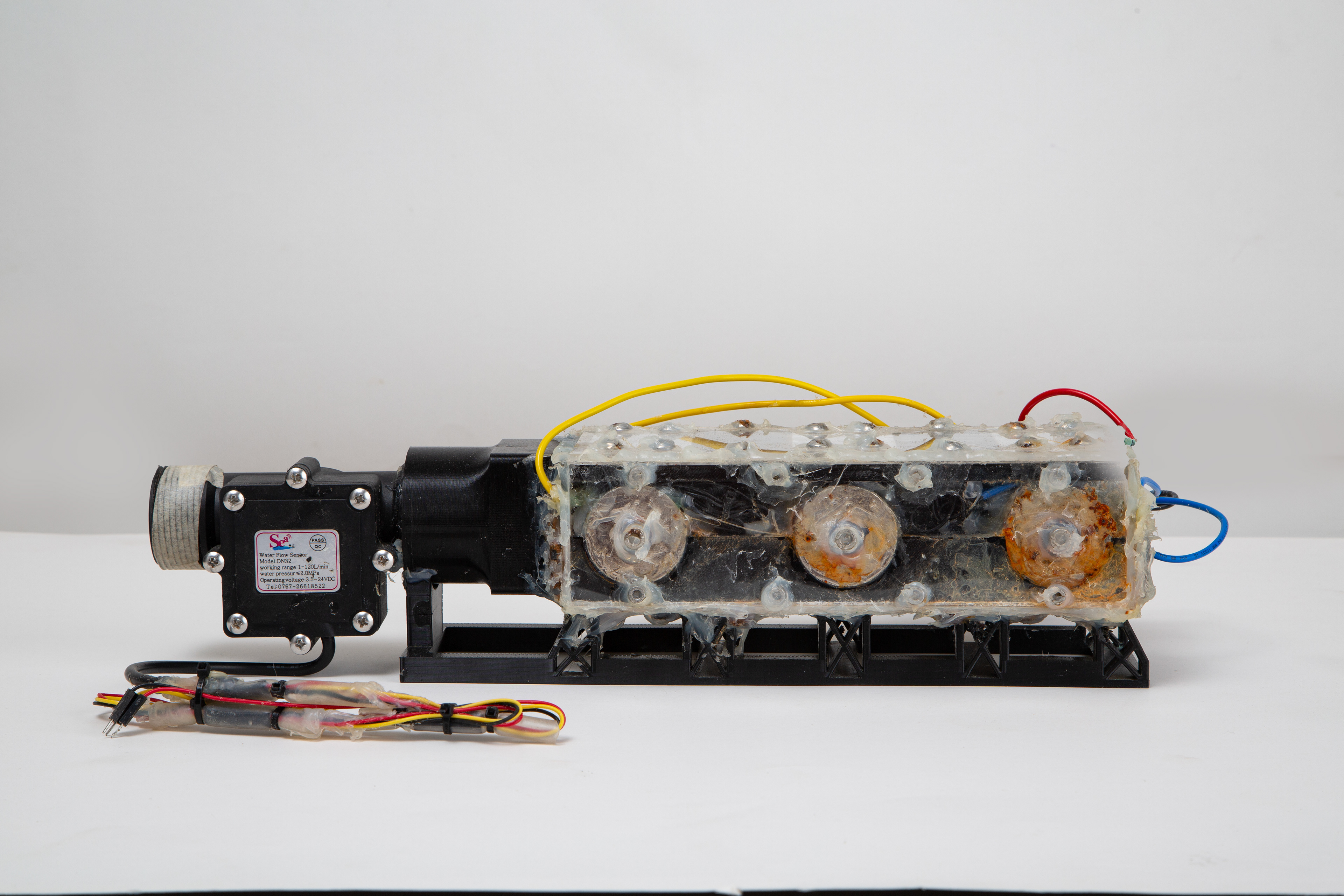
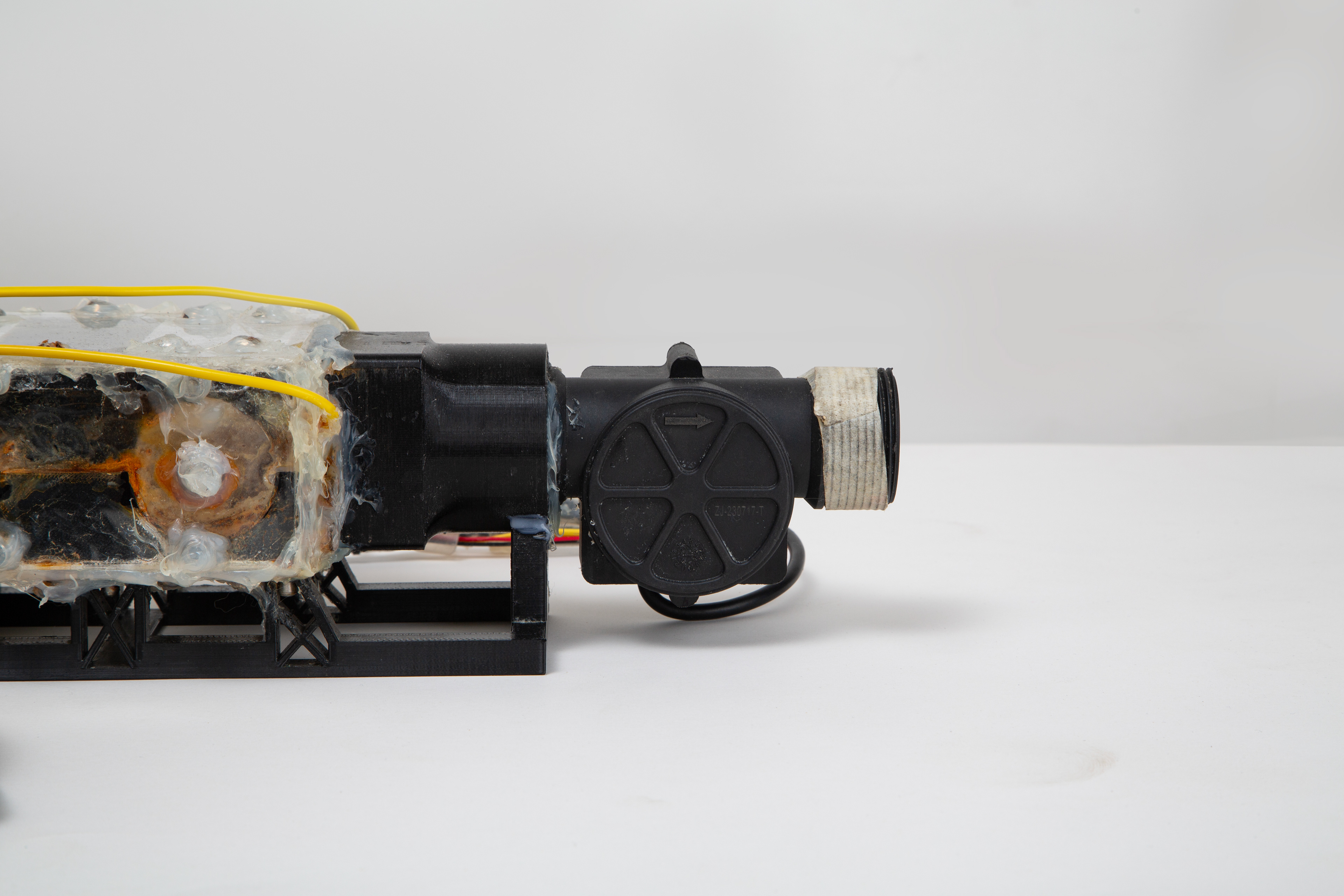
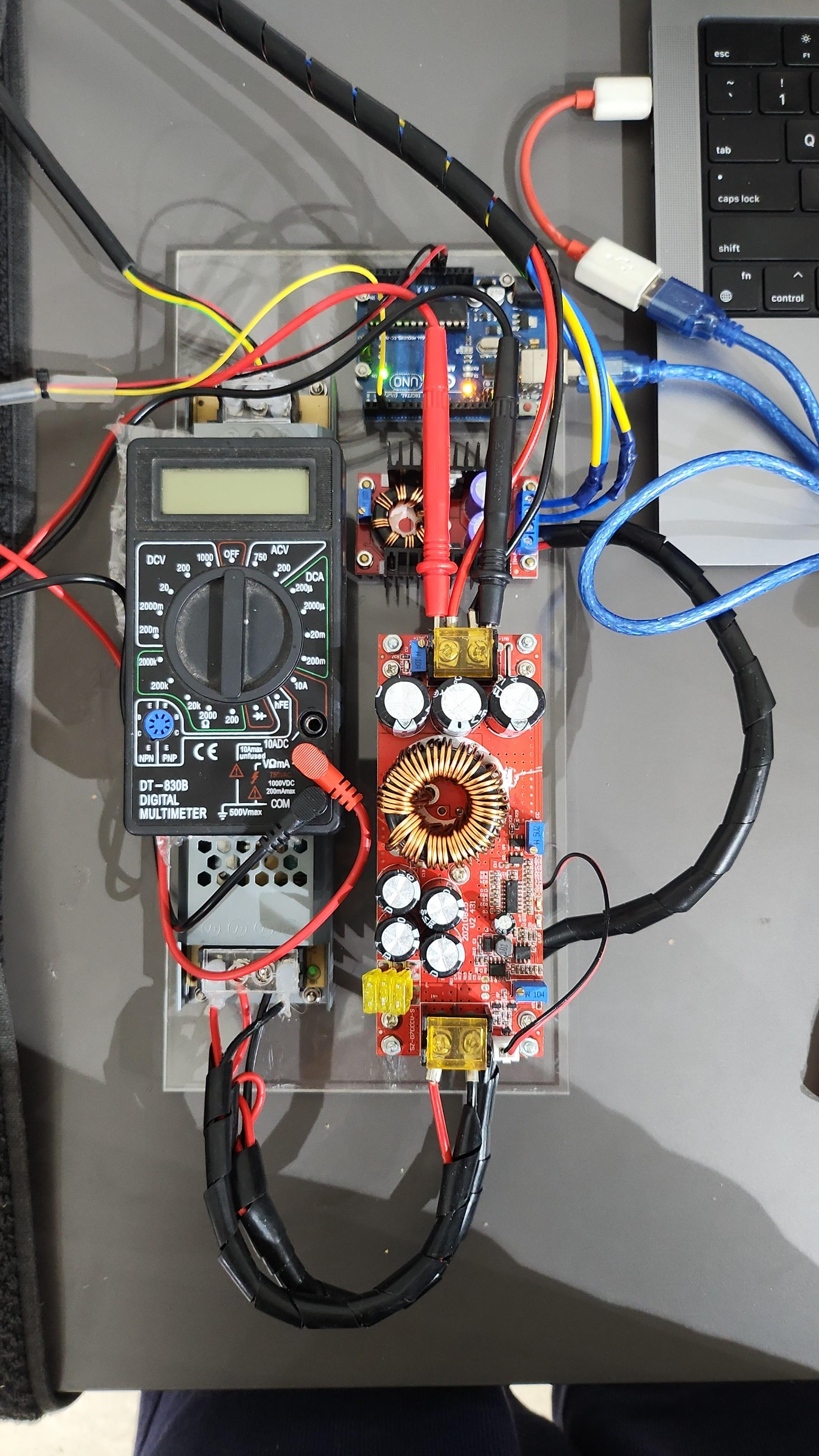