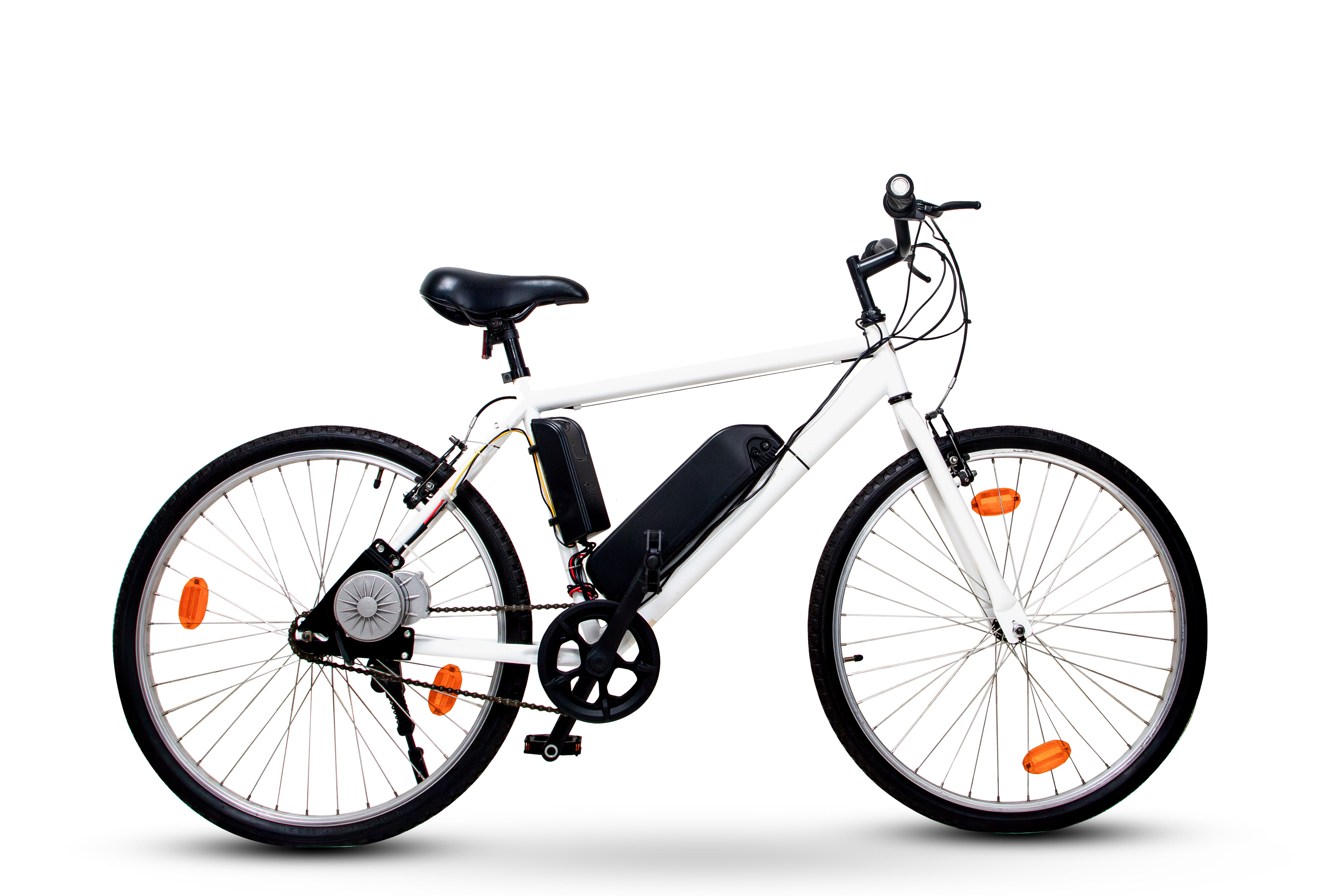
I converted a standard bicycle into an electric cycle, targeting a maximum speed of approximately 50 km/h. This project focused on understanding the integration of electrical and mechanical subsystems within a minimal-cost framework. The main technical goals included selecting an appropriate DC motor and transmission method, implementing a stable and efficient battery solution, and establishing reliable control electronics. By combining these systems, I aimed to develop a functional and durable electric cycle that could serve as an educational platform for learning about propulsion, battery management, and electronic control.
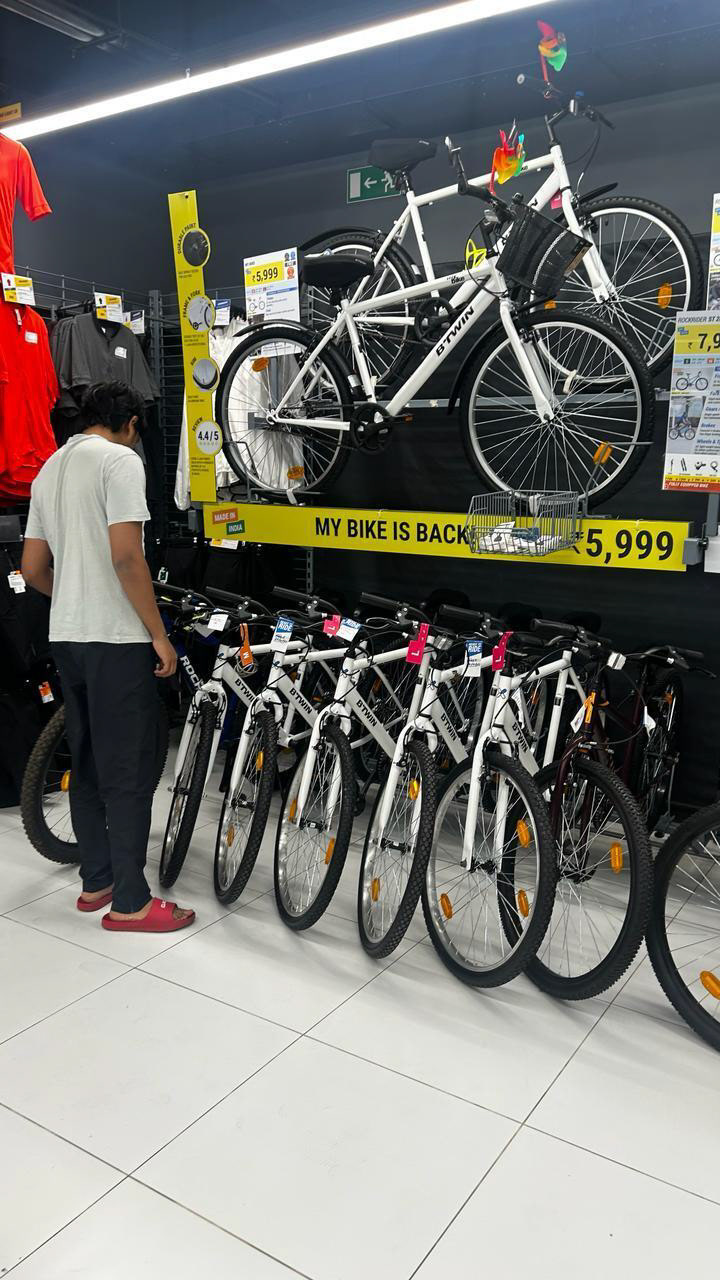
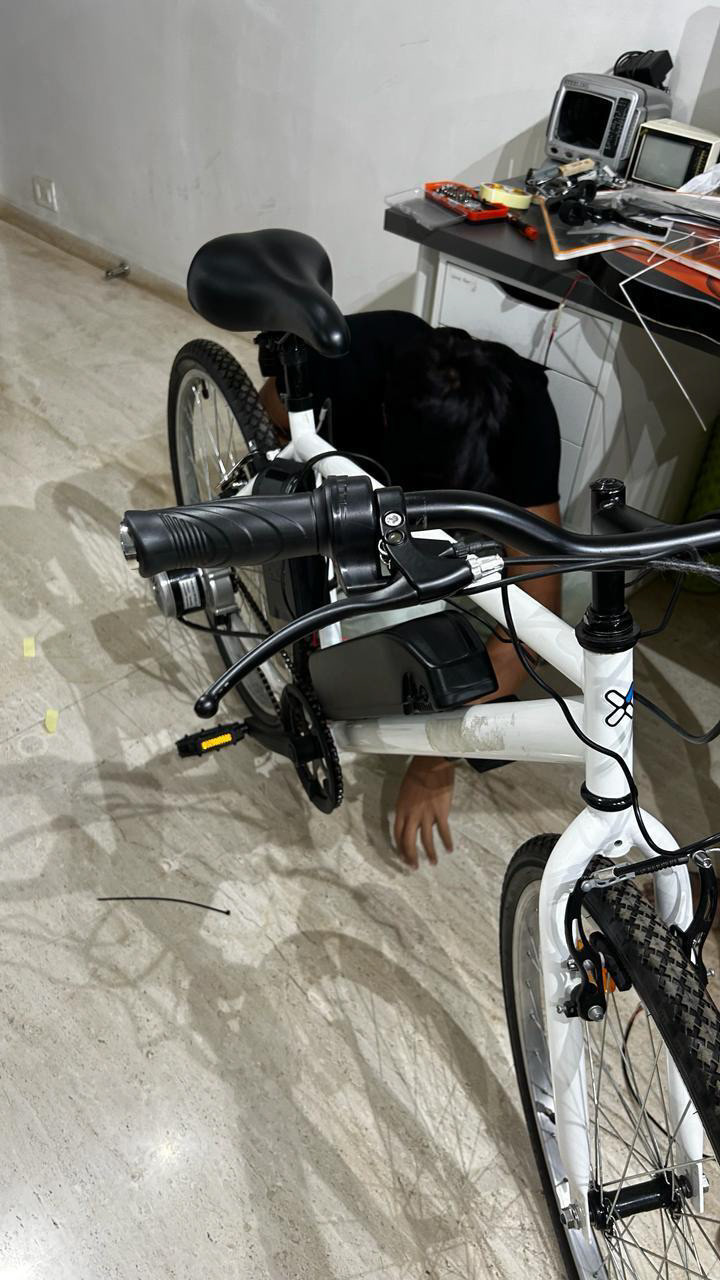
Mechanical Integration and Power Transmission
The selected motor was a 250 W DC unit designed for low-voltage operation and moderate torque output, widely available through standard electronics and hobby suppliers. A suitable gear ratio, implemented via a separate sprocket and chain assembly, transferred power from the motor shaft to the rear wheel. This configuration offered a balance of acceleration and cruising speed, allowing the cycle to reach approximately 50 km/h under favorable conditions.
Chain specifications matched the motor’s output shaft and the rear sprocket’s pitch, resulting in stable, slip-free engagement. Basic tensioners and alignment tools ensured the chain remained correctly tensioned, reducing wear and improving efficiency. Minor frame modifications were necessary to accommodate the motor mount, with custom brackets bolted to existing frame points and reinforced where needed. This approach maintained overall structural integrity and minimized unwanted vibrations or flex during operation.
Battery Pack and Mounting Solutions
A lithium-ion battery pack of moderate capacity (e.g., 24–36 V nominal, around 10–15 Ah) was sourced as a complete unit suited for e-cycle applications. This pre-assembled pack featured an integrated battery management system (BMS) and a protective enclosure. The chosen form factor allowed direct mounting onto the frame’s bottle-cage bosses using a dedicated bracket, ensuring secure attachment and balanced weight distribution along the bicycle’s centerline. This mounting strategy contributed to stable handling and simplified daily operation, as the battery could be easily removed or serviced without disassembling other components.
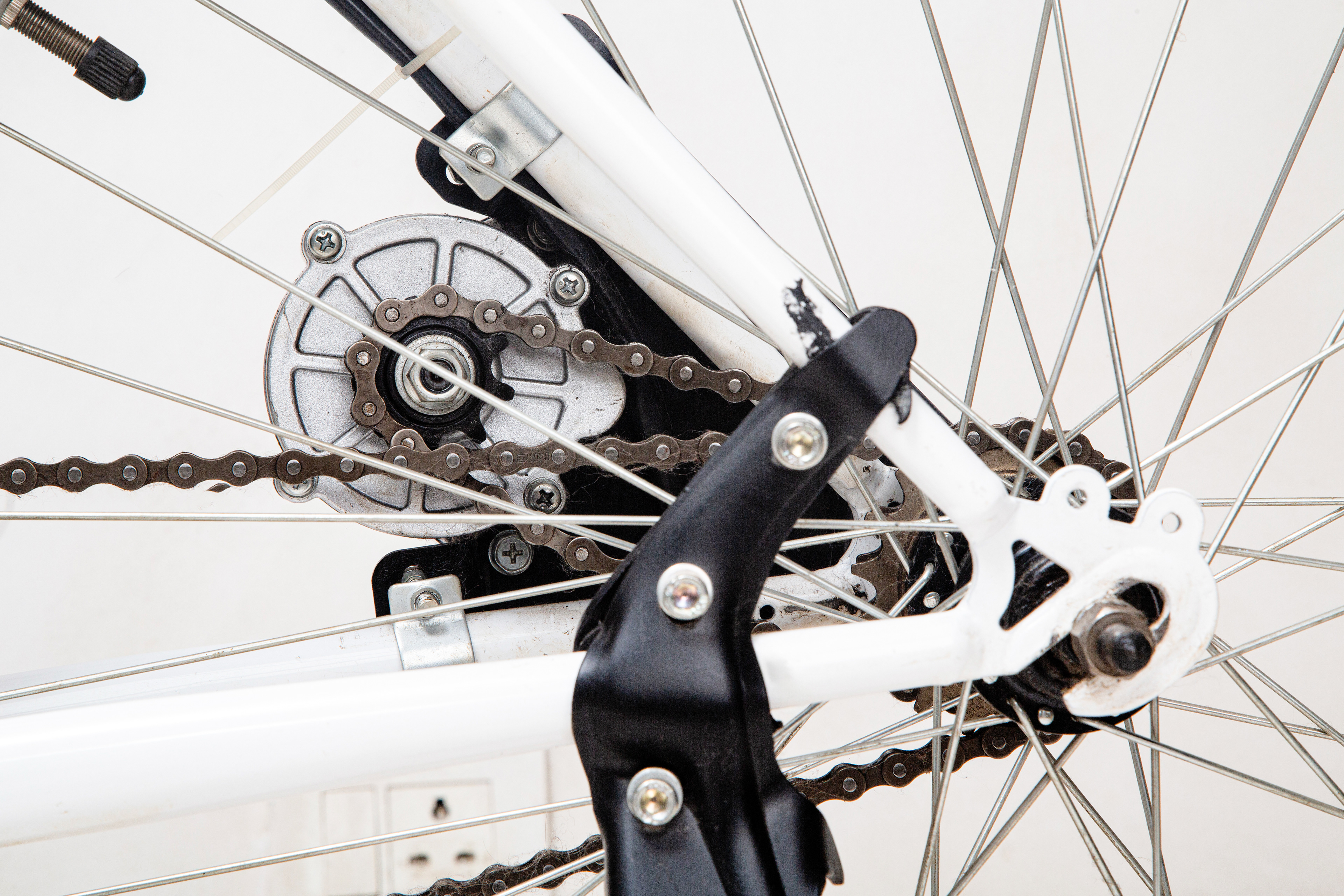
Control Electronics and Sensor Integration
A standard brush DC motor controller provided the interface between the battery and the motor, regulating current flow to maintain stable operation and protect against over-current conditions. The controller’s default parameters, typically optimized for small electric vehicles, were retained, striking a practical balance between responsiveness and battery life. An integrated throttle interface gave the rider direct control over acceleration and speed.
Pedal assist functionality was introduced with a basic cadence sensor mounted near the bottom bracket. This sensor detected pedal rotation and signaled the controller to deliver proportional power, supplementing human effort. This arrangement improved overall efficiency and ride comfort, reducing rider fatigue on inclines and at cruising speeds.
Regenerative Braking and Additional Features
While advanced regenerative braking can be complex, a basic arrangement was explored by incorporating a controller capable of limited energy recovery. During deceleration, the controller allowed a small amount of current to flow back into the battery. Although the net gain in efficiency was modest, it demonstrated the concept of harnessing kinetic energy and reinjecting it into the storage system. Fine-tuning these features would require further testing and custom controller firmware, but initial results suggested that incremental gains were achievable.
Testing, Adjustments, and Practical Considerations
Initial testing involved short runs on smooth and uneven surfaces to evaluate handling, energy consumption, and mechanical robustness. Adjustments included refining cable routing with additional zip ties and improved solder joints to ensure stable electrical connections. Slight modifications to chain length prevented interference with the frame, and securing all components with proper fasteners minimized rattling or unintended movement at higher speeds.
Informal measurements using a multimeter and tachometer provided insight into the current draw, voltage stability, and motor performance under load. These measurements guided incremental improvements, ensuring the system operated safely within the motor and battery’s specified limits.
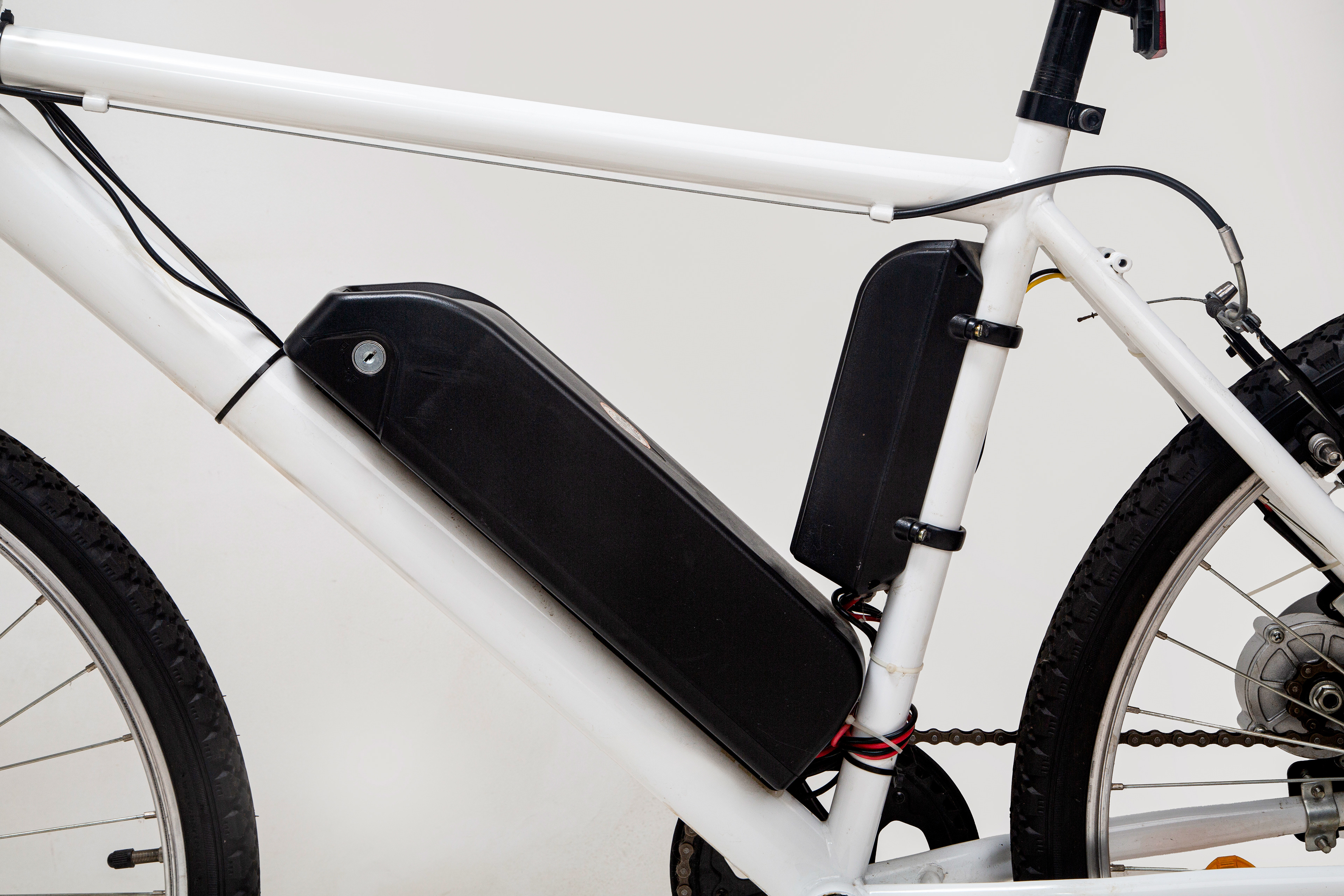
Converting a conventional bicycle into a functional electric cycle gave me insights into selecting and integrating motors, choosing appropriate battery systems, and implementing basic control electronics. Balancing cost constraints with performance requirements required careful consideration of available components and incremental optimization. In tackling each challenge—motor mounting, battery management, chain alignment, and sensor integration—I developed skills in diagnosing problems and applying critical thinking to achieve practical engineering solutions.
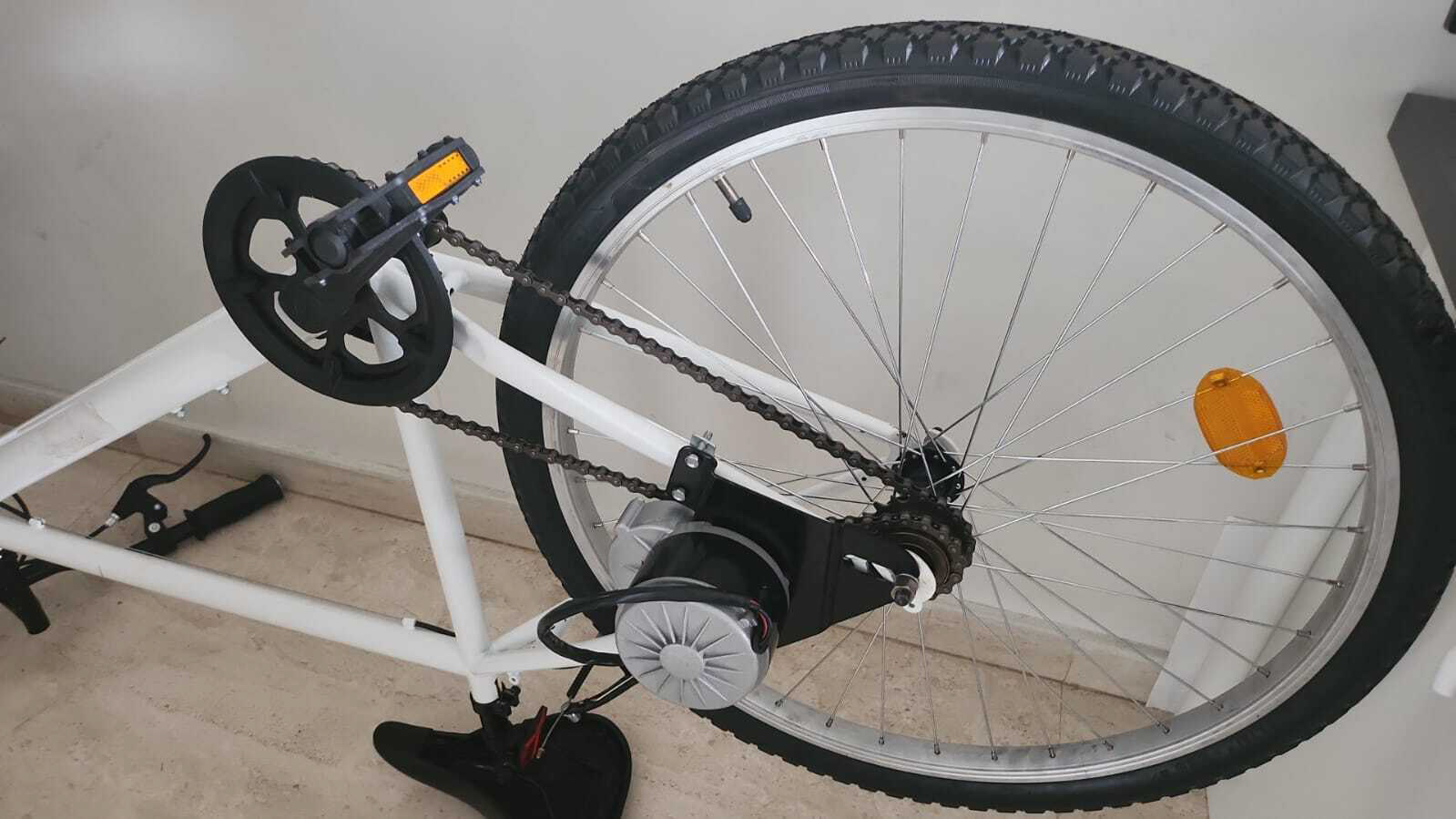
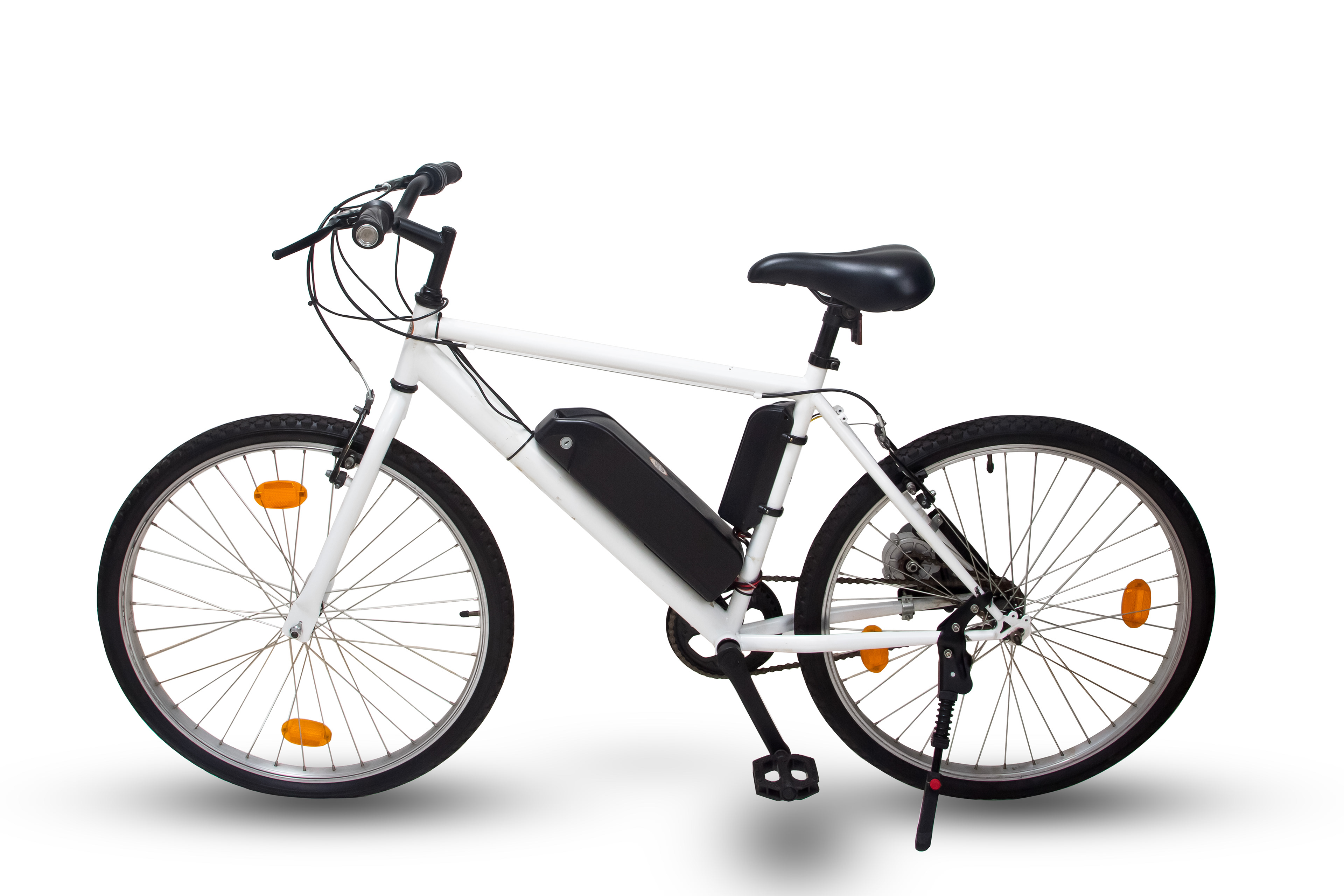
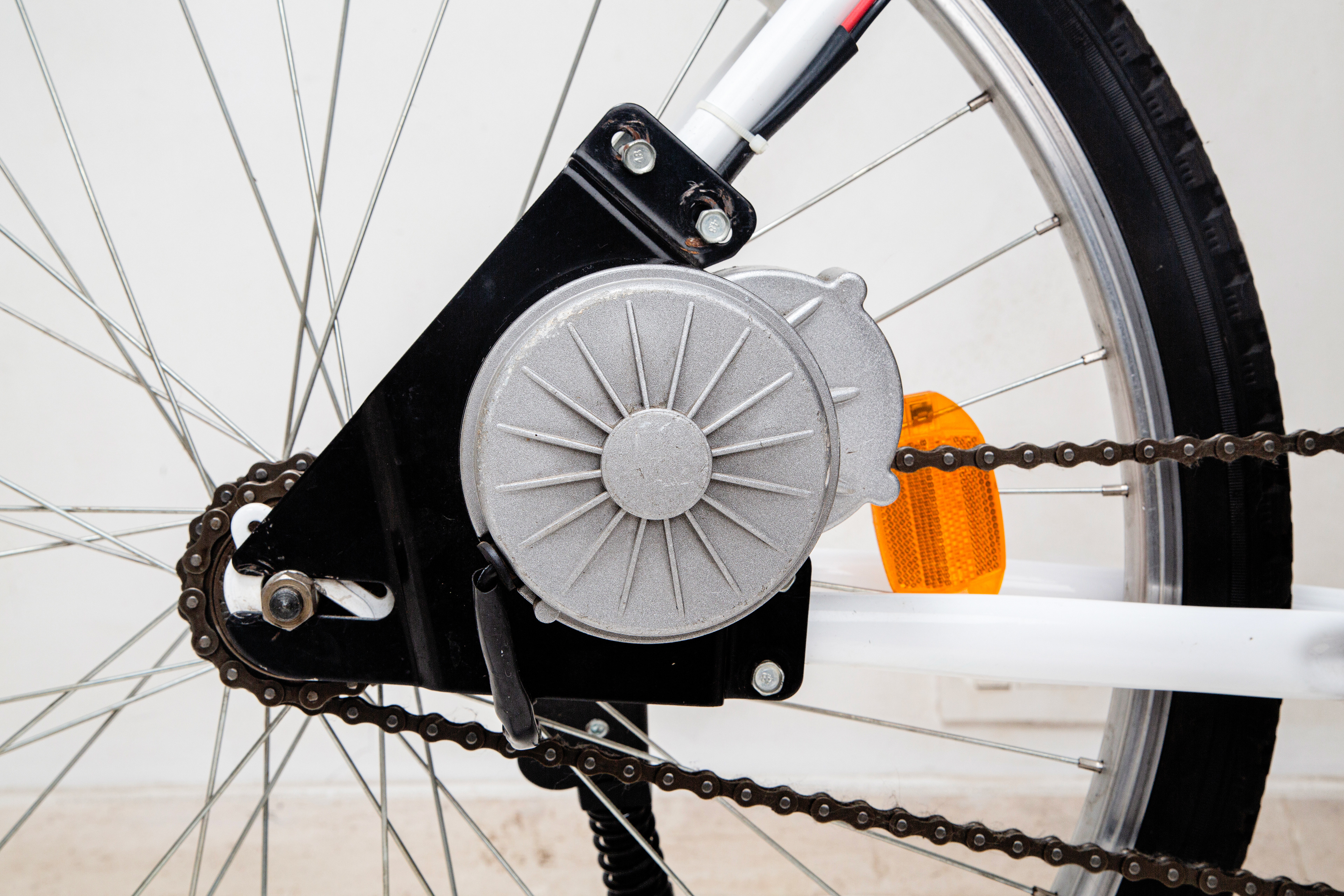
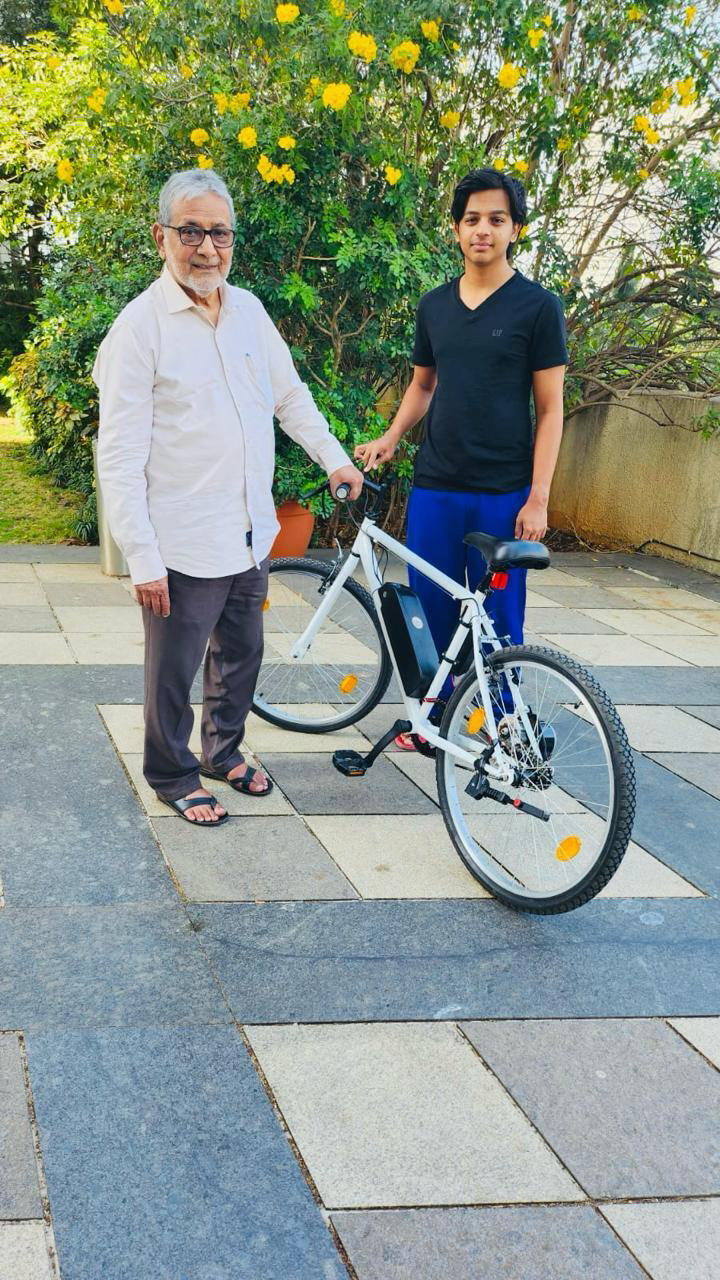