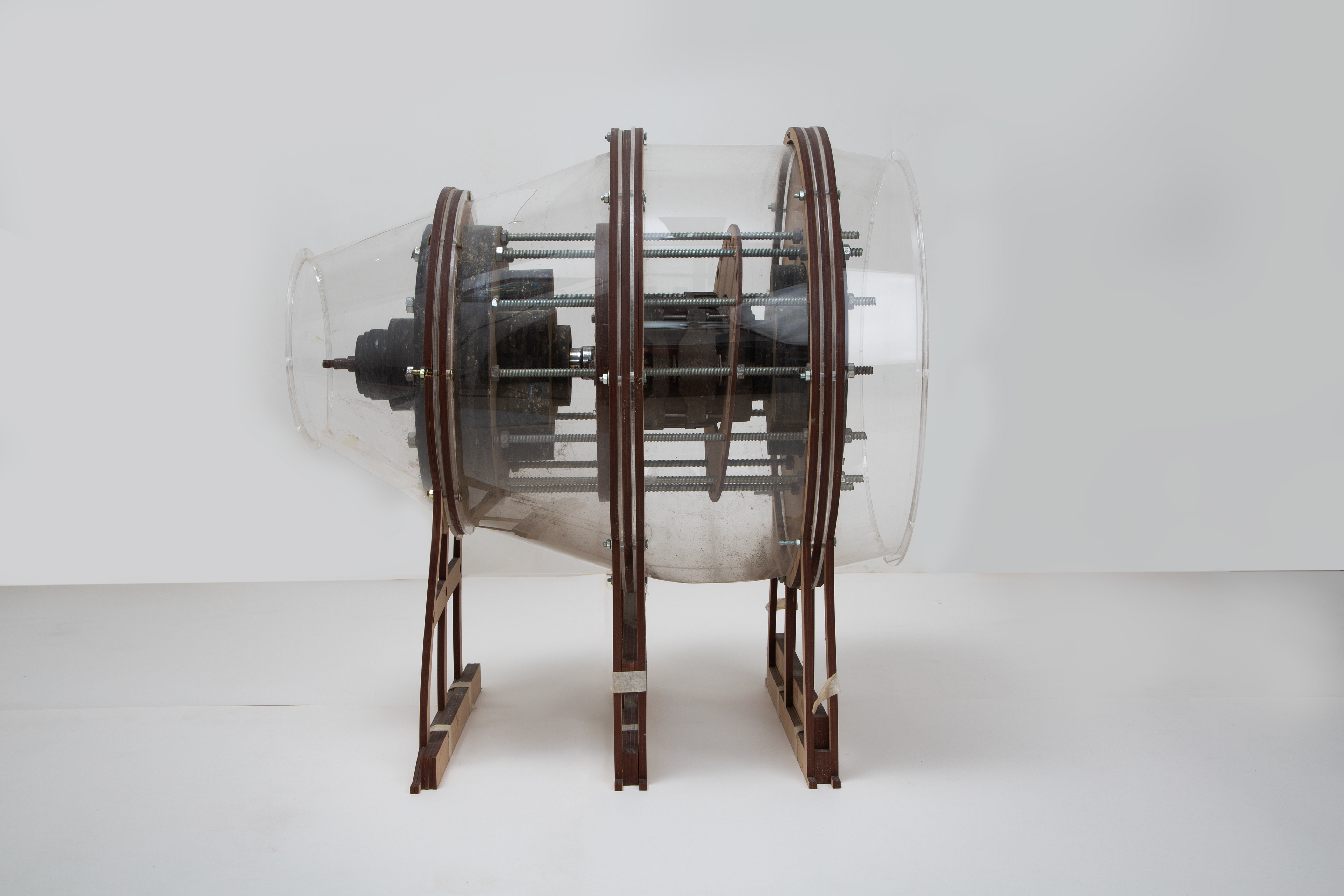
I researched and developed a small-scale hydropower turbine concept tailored to some rural regions' low-head, high-flow conditions. The objective was to provide a reliable, cost-effective solution to energy poverty by offering continuous power generation during seasonal flows. This effort required extensive investigation into turbine configurations, fluid dynamics, mechanical structures, and direct engagement with manufacturers and suppliers. Ultimately, the project aimed to create a system that could be efficiently assembled, sealed, and installed with minimal civil work, delivering a practical and ethically sound approach to sustainable energy in off-grid regions.
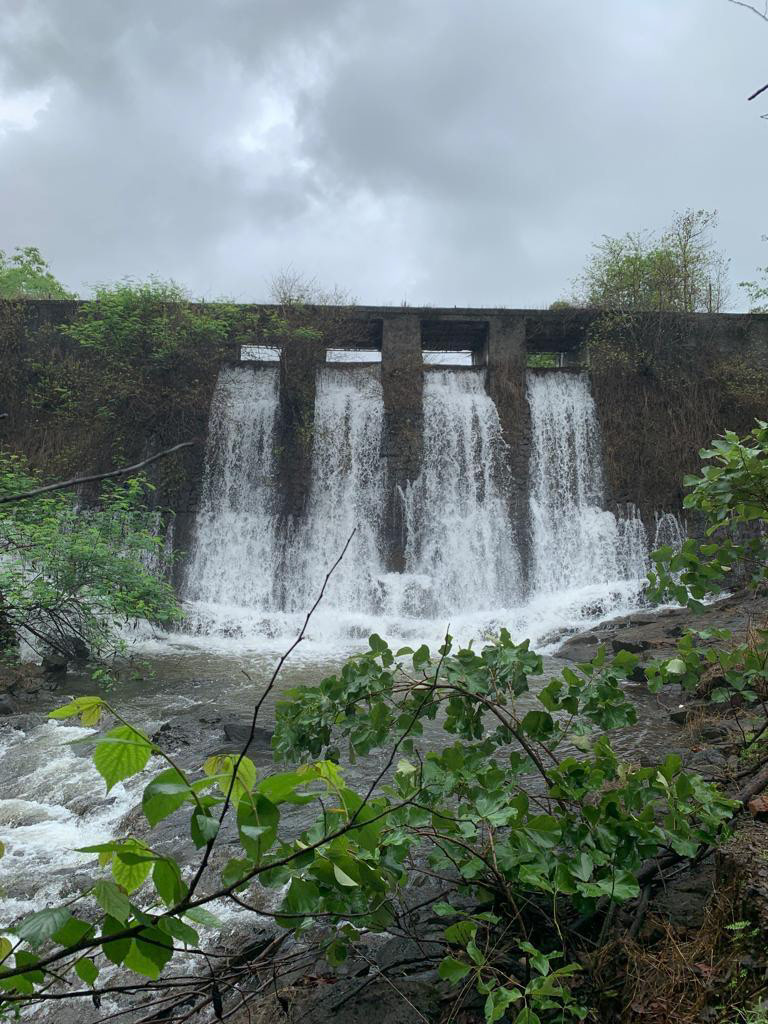
Site Assessment and Conceptual Design
The initial phase involved assessing potential installation sites, notably in the Raigad district, to determine suitable head and flow conditions. Although the final implementation depended on seasonal measurements and monsoon patterns, preliminary surveys guided key design choices. Investigating established turbine types (Kaplan, Francis, Pelton) and scaling their principles to a pico-scale system, I concluded that an axial-flow Kaplan configuration would best accommodate the low head and high flow scenario. This decision balanced efficiency, simplicity in external structures, and compatibility with locally available materials while allowing the turbine to operate as a largely self-contained unit requiring minimal external civil engineering.
Structural Prototype and Assembly Feasibility
To validate the practicality of component integration, I constructed a non-water-tested structural prototype from laser-cut MDF segments. The prototype was a tangible reference for verifying how well the generator, turbine shaft, and planetary gearbox could fit together within a bulb-shaped housing. While this model could not withstand immersion or measure hydrodynamic forces, it was instrumental in identifying assembly challenges—such as screw placement, shaft coupling, and alignment—that would influence the final design. The MDF layers, stacked to form the three-dimensional contours of the turbine body, offered valuable insights into clearances, internal support needs, and ease of future maintenance operations.
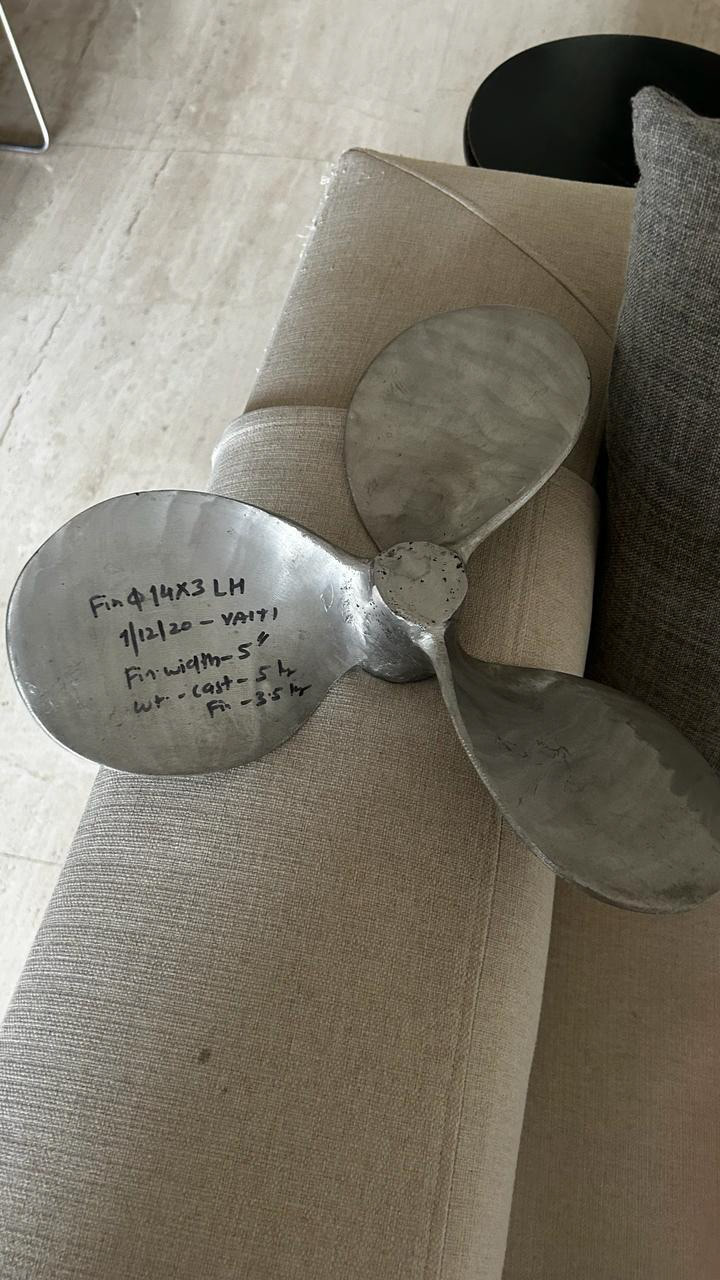
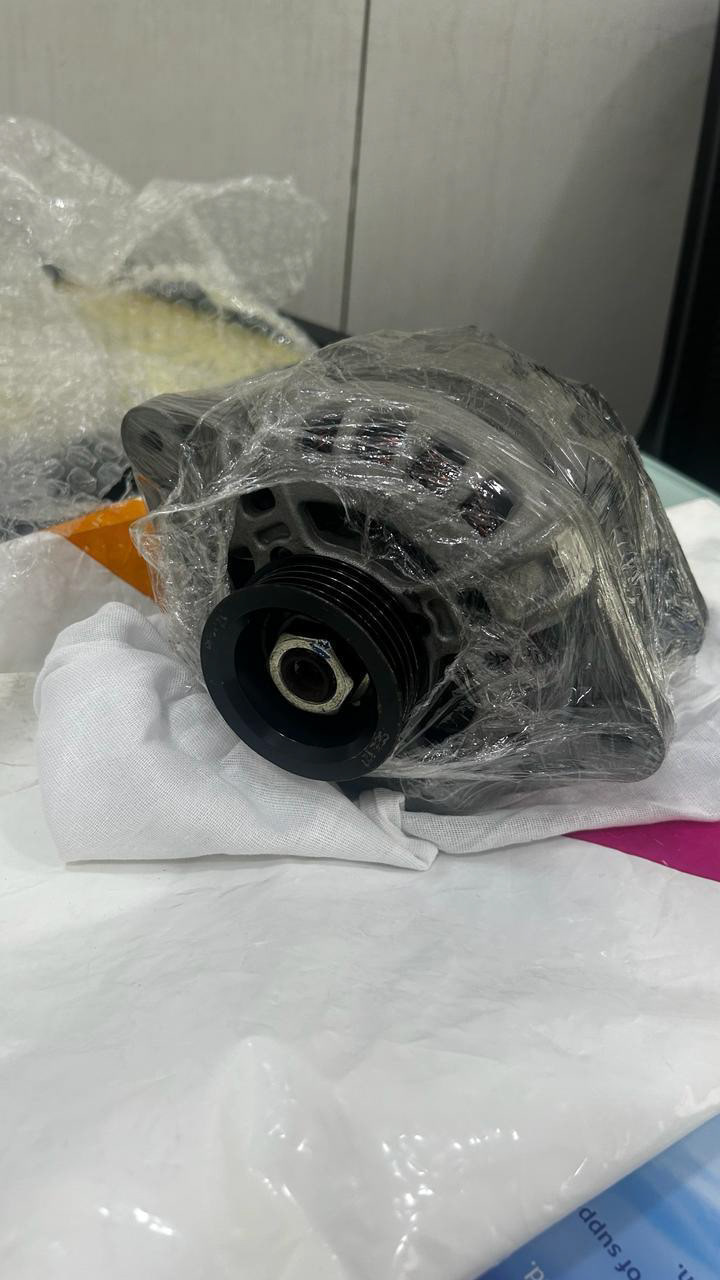
Analytical Methods and Flow Considerations
Although no direct water flow tests were performed at this stage, analytical methods and prior research guided key design refinements. For example, arranging components along the rotation axis would have introduced unnecessary drag, prompting a redesign into two symmetrical halves joined by a single horizontal flange. This approach improved manufacturing efficiency, structural strength, and simplified sealing surfaces. Simulated motion using a motor-driven belt and pulley system allowed me to approximate dynamic loads and identify potential vibration points. These findings will inform future iterations where actual water flow testing and torque measurements will confirm the turbine’s performance under operational conditions.
Revisions and Material Selections
Iterative redesigns simplified the turbine housing from multiple longitudinal segments to two symmetrical halves. This change reduced complexity, improved structural integrity, and minimized sealing points susceptible to leaks. While the prototype used MDF and acrylic for easy fabrication, subsequent versions will employ aluminum for the main body due to its suitability for shaping into the bulb form and stainless steel for internal supports to ensure precise shaft alignment and long-term durability. These material selections reflect lessons from the initial structural trials and lay the groundwork for a fully functional, water-exposed prototype.
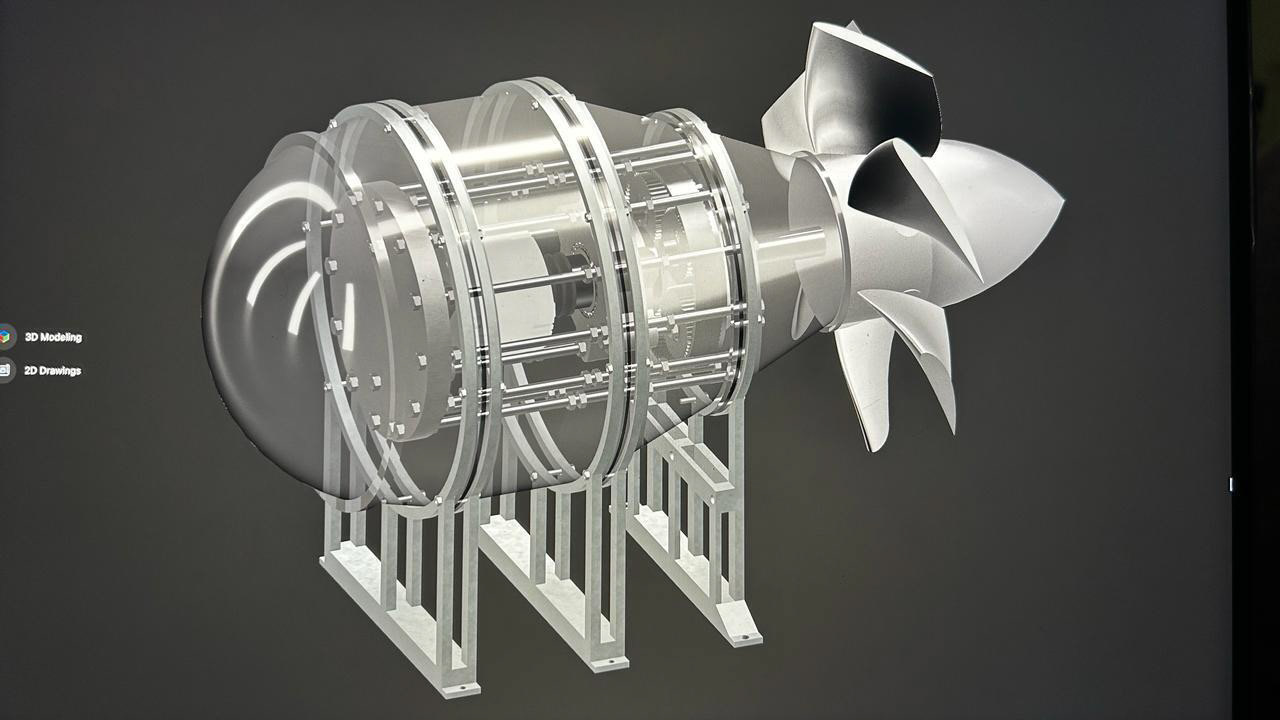
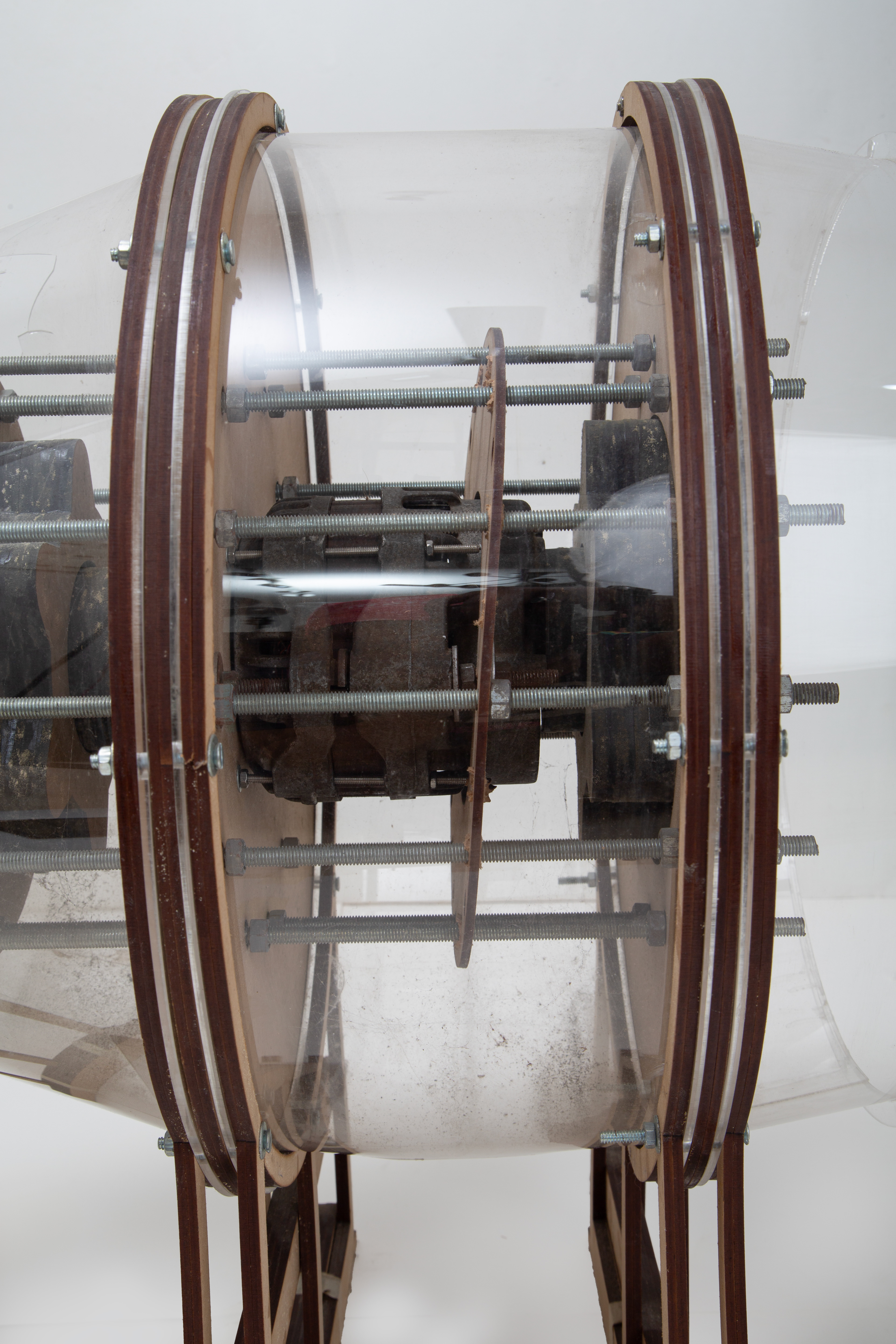
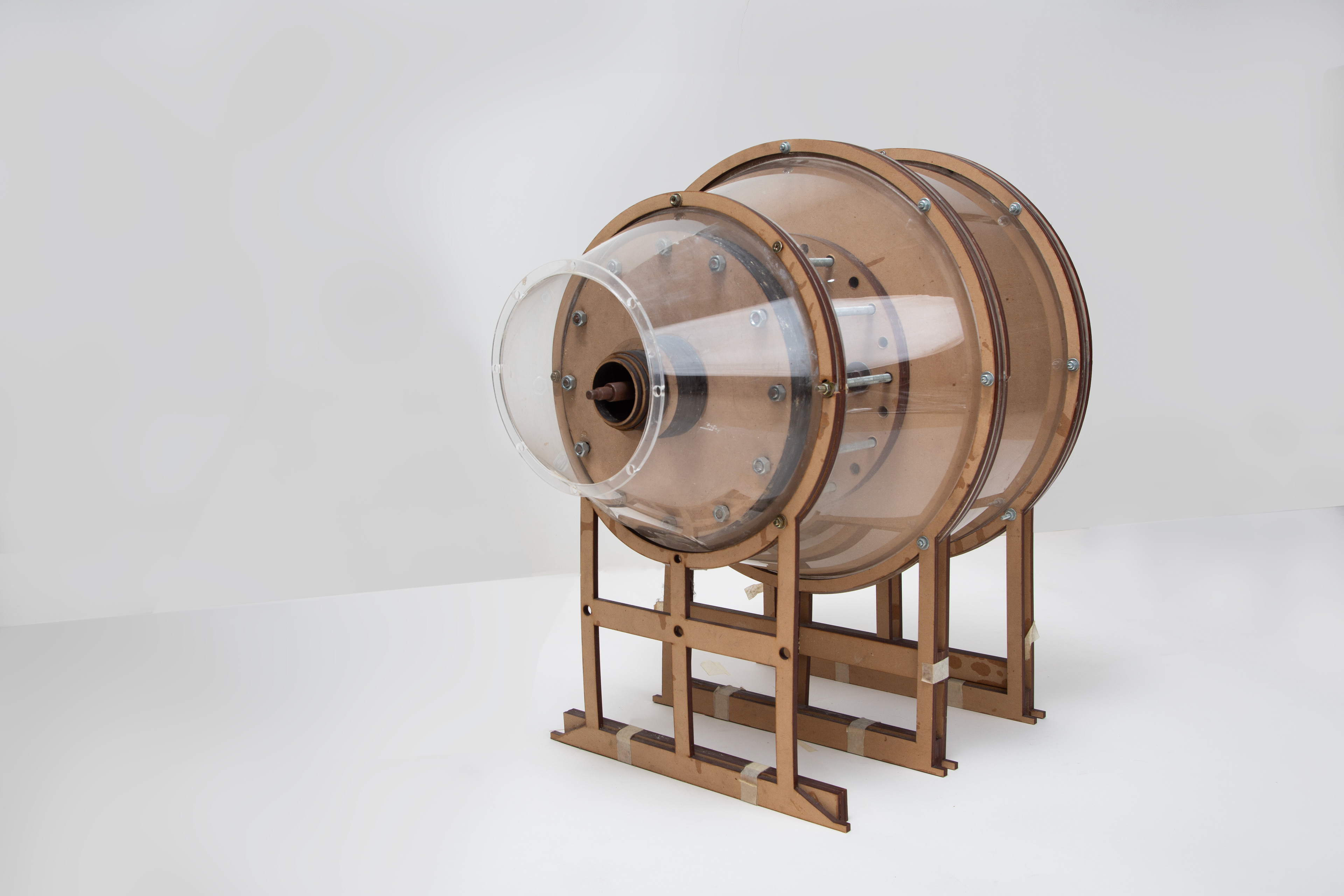
Supplier Engagement and External Feedback
Before finalizing the design, I consulted with specialists, including planetary gearbox manufacturers, mechanical seal suppliers, welding experts, boat propeller manufacturers, and CNC machinists. Their feedback highlighted potential manufacturing constraints, assembly techniques, and alignment strategies I had not considered initially. Incorporating their expert insights into the final design ensured the system could be feasibly produced and maintained in the field, strengthening the project’s viability and cost-effectiveness.
Next Steps and Deployment Plans
With complete structural validation and a clearer understanding of material requirements and assembly procedures, the next stage involves producing a second prototype suited for actual water exposure and flow testing. During this phase, I will evaluate performance metrics under controlled conditions, such as torque, efficiency, and power output. Concurrently, I plan to establish supply chains, streamline fabrication processes, and coordinate with local stakeholders to facilitate pilot installations. These steps will transition the project from concept to functional reality, ultimately delivering a modular and easily deployable hydropower solution for off-grid communities.
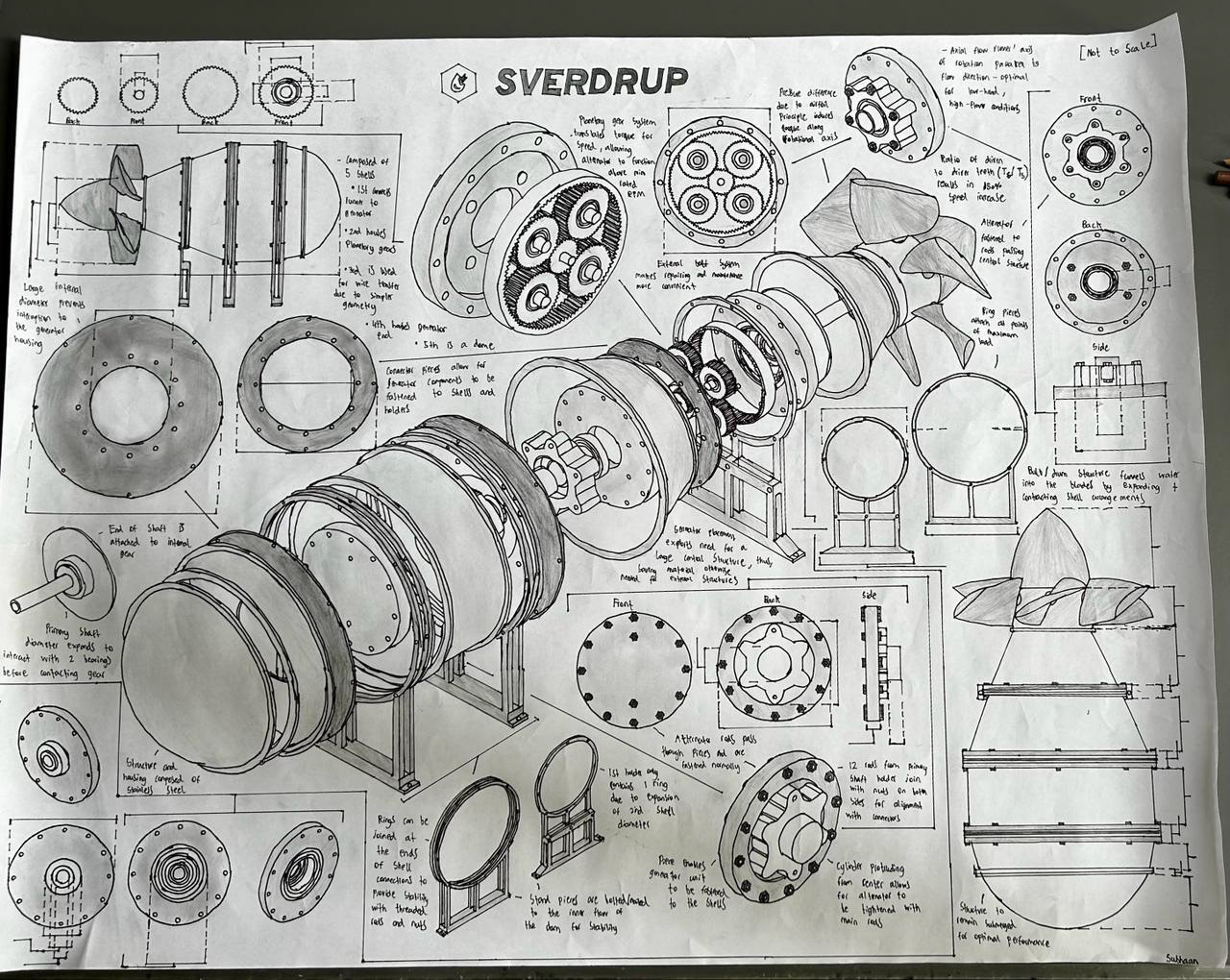
Developing the structural prototype and conducting preliminary analytical assessments allowed me to refine the hydropower turbine design before subjecting it to real-world operational conditions. By focusing initially on assembly feasibility and spatial integration, I identified potential pitfalls, adapted the shape and internal configuration, and documented best practices for future installers. The knowledge gained through this iterative process will guide the introduction of advanced materials, robust sealing methods, and efficient component sourcing. These improvements will support reliable electricity generation in rural areas, contributing to the global objective of alleviating energy poverty through sustainable engineering solutions.
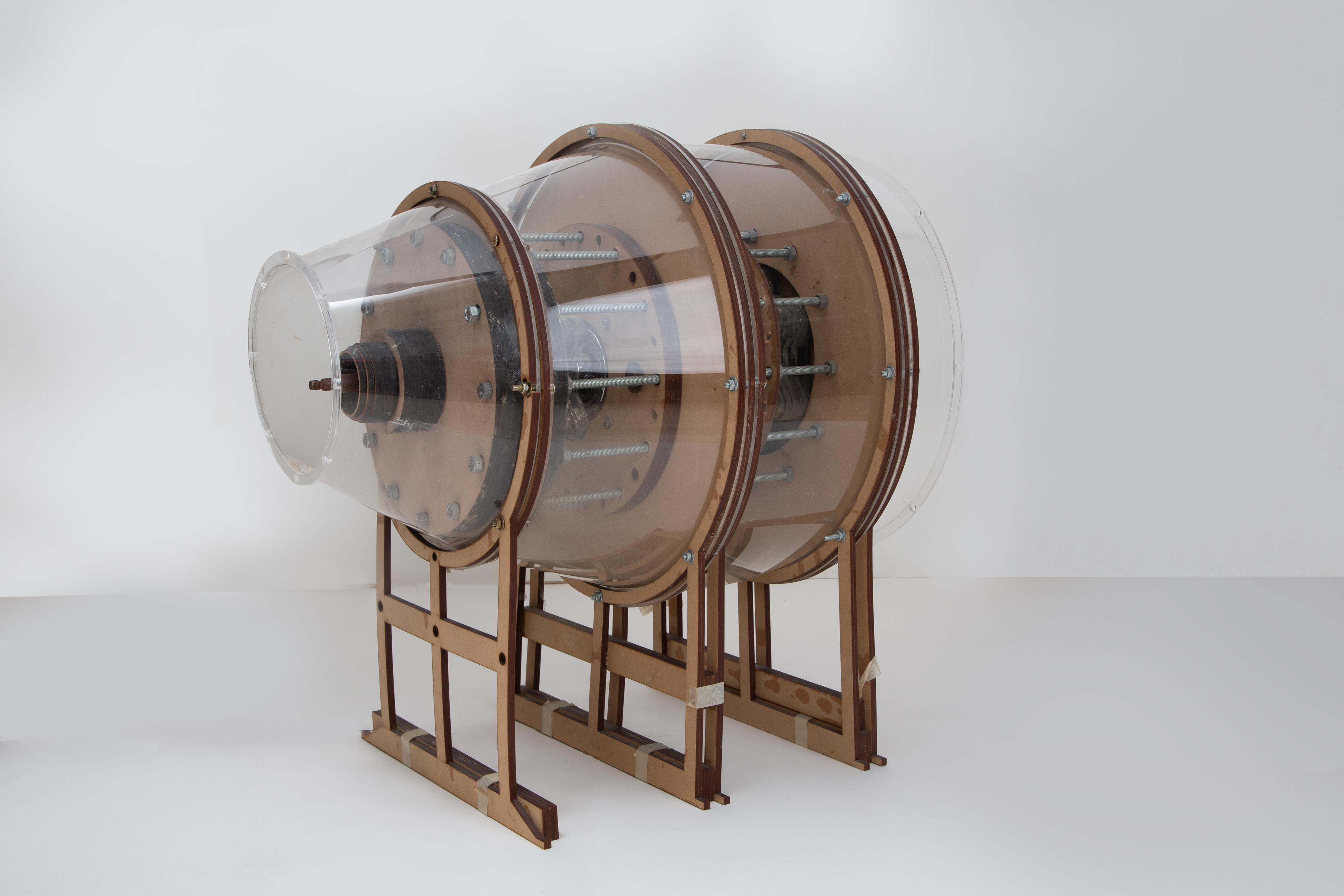
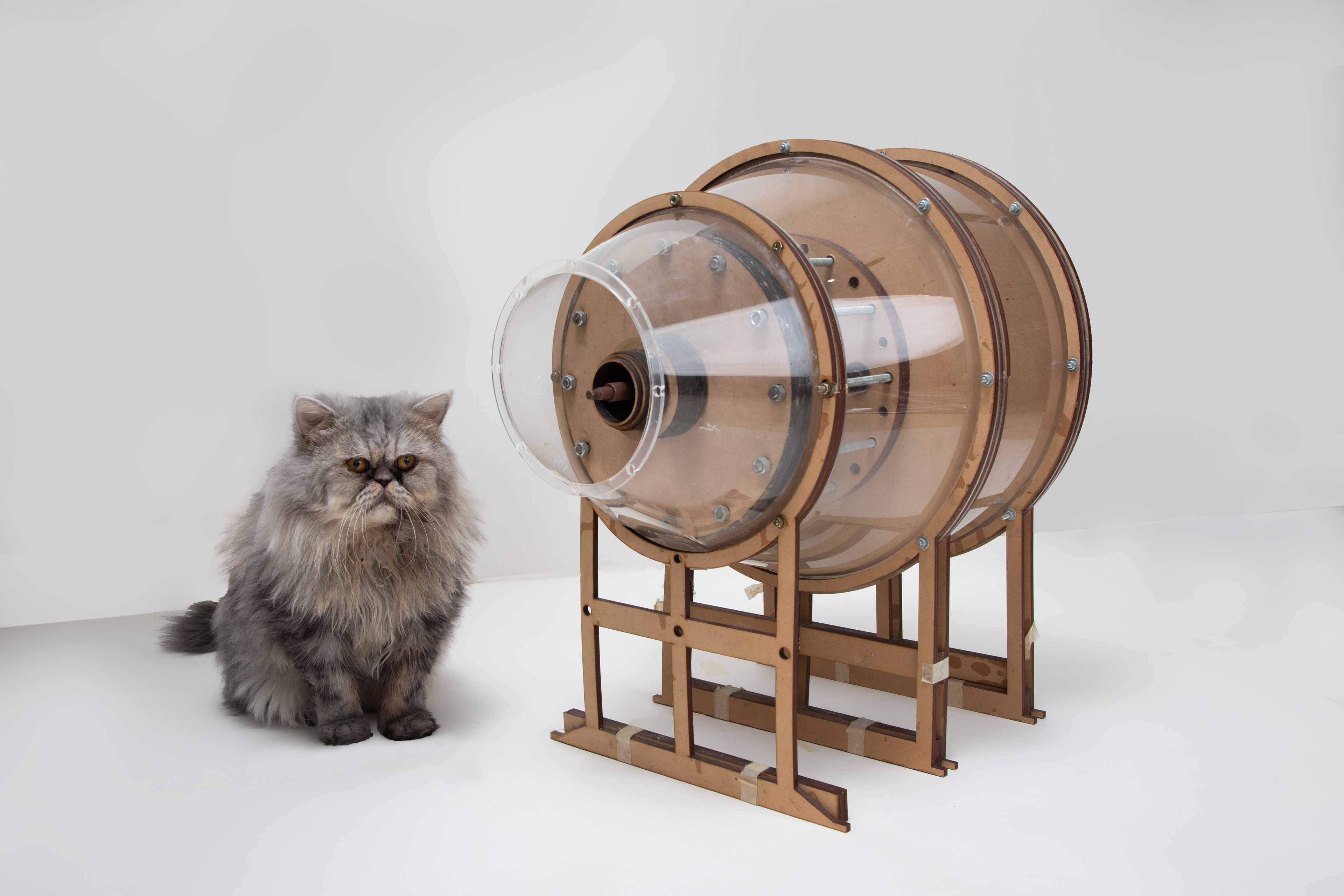