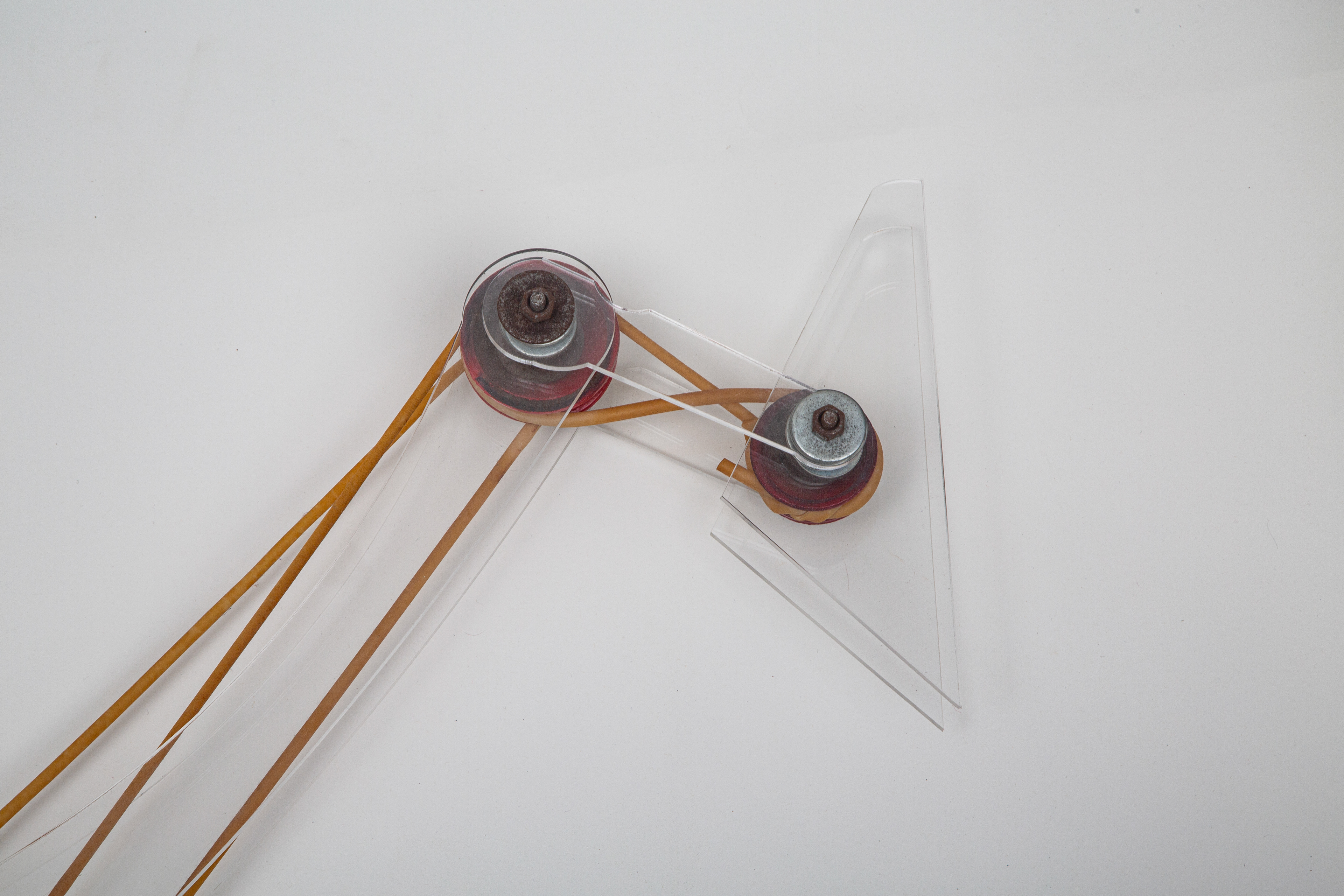
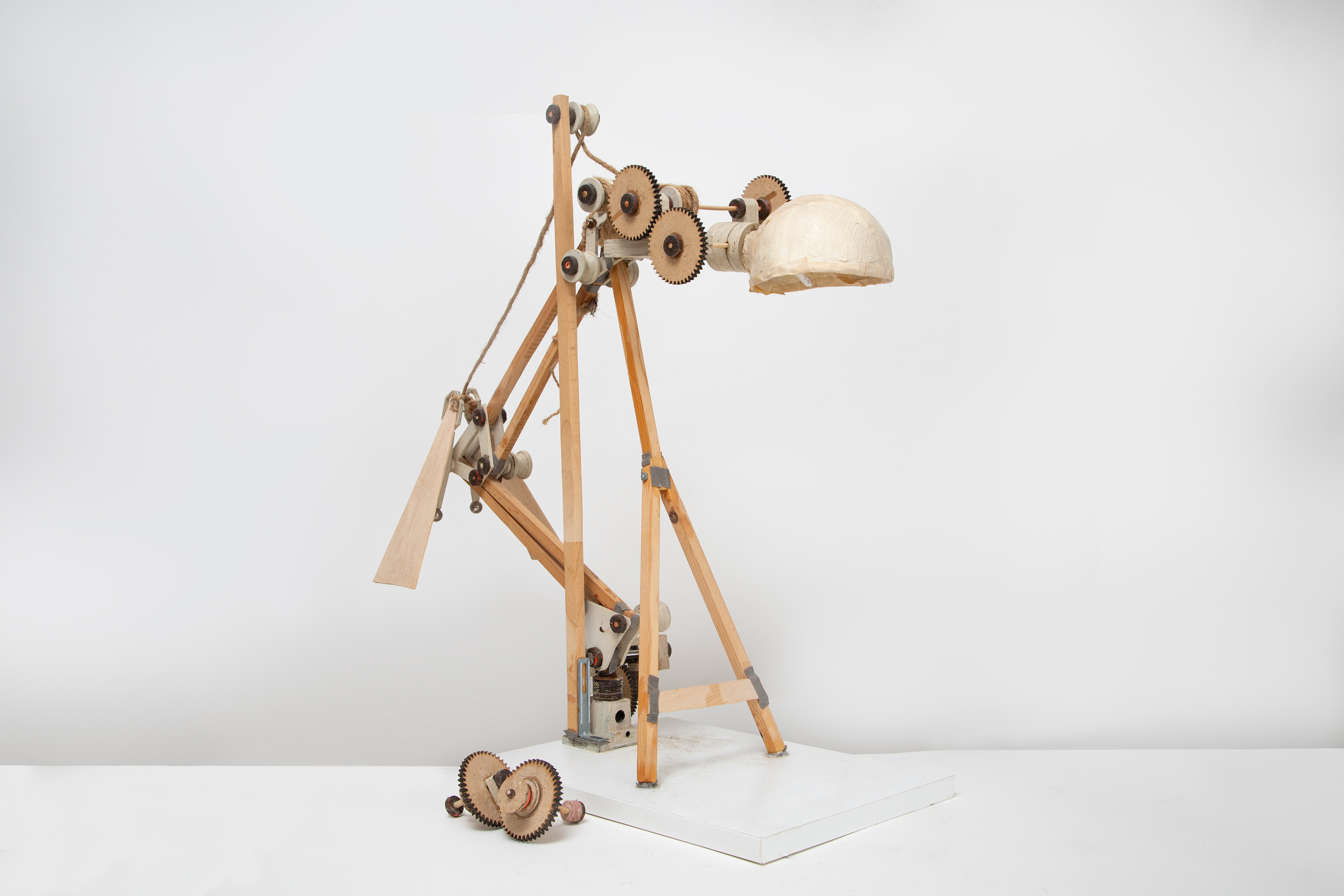
HORSE LEG
In this project, I researched and designed a bioinspired robotic structure modeled after the anatomy of a horse’s leg. While the physical prototype focused on a single-leg segment constructed primarily from laser-cut acrylic components and surgical tubing, my overarching design envisioned a full-body quadrupedal system. The intent was to explore how the complex interplay of tendons, ligaments, and joints in a horse’s limb could inform the creation of a mechanically coupled robotic mechanism. Although the final model did not directly find an external application, the process significantly advanced my understanding of the fundamentals of bioinspired robotics, from replicating the biomechanics of natural structures to refining mechanical stability and load distribution strategies.
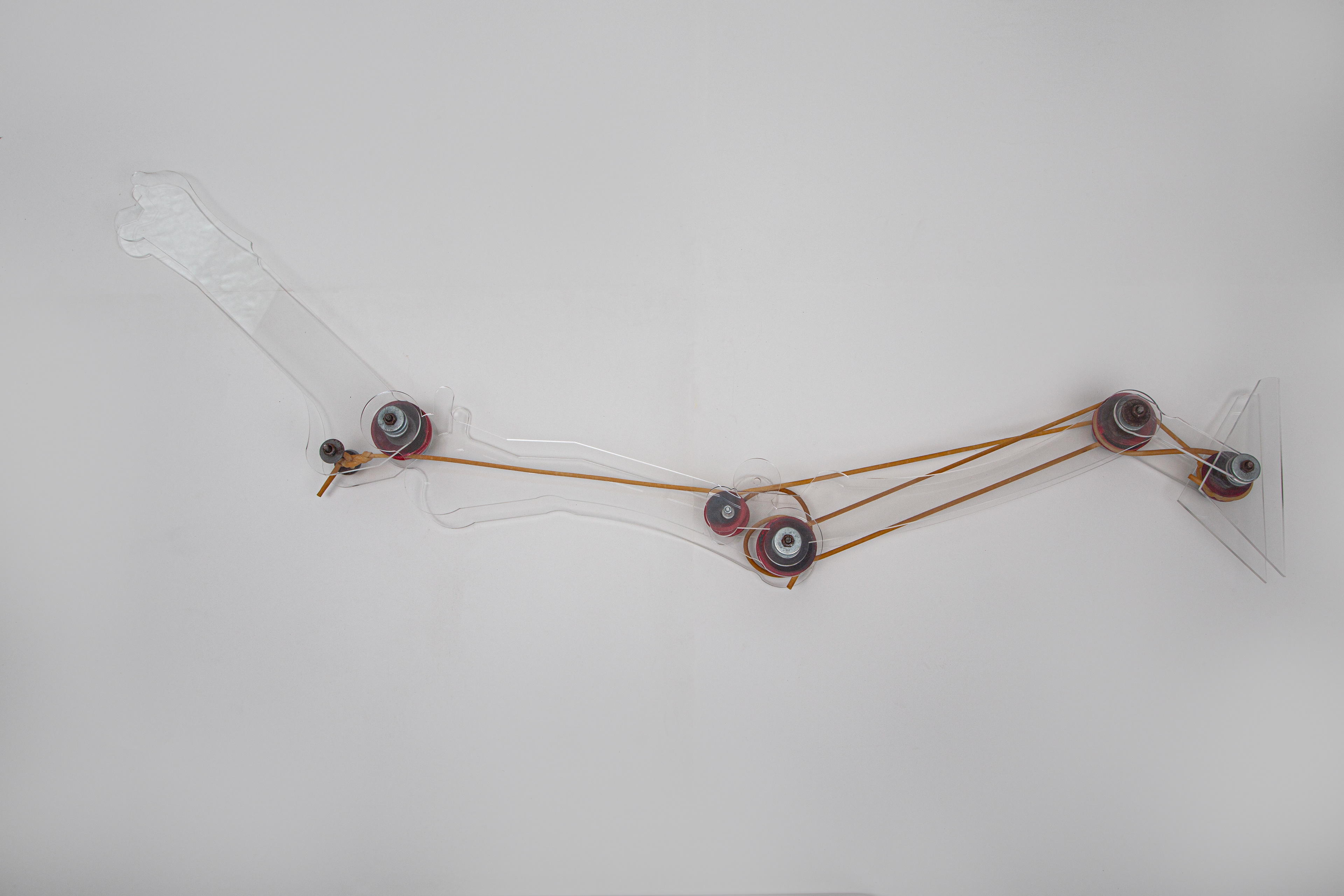
Conceptual Design and Material Selection
The initial design goal was to replicate key features of equine locomotion: the capacity for weight-bearing and efficient load transfer, along with the spring-like energy storage and release capabilities of tendons. Drawing inspiration from research on poly-articular elastic mechanisms and tendon arrangements, I sought to replicate the core functionality of a horse’s lower limb. Given practical constraints, acrylic was chosen as the primary building material due to its availability, uniform thickness, and compatibility with laser cutting—factors that allowed for precise, rapid prototyping despite the material’s tensile strength and flexibility limitations.
Surgical tubing was a stand-in for tendons and ligaments, stretched across pulleys to simulate elastic energy storage. This conceptual substitution allowed me to illustrate how interconnected pulleys, guided by carefully placed “extends,” could transmit force from one joint to another. Although these elements worked only to a limited extent—partly due to suboptimal material elasticity and friction—they proved how strategically routed cords could mimic natural joint coupling, even on a smaller, more rudimentary scale.
Joint Configuration and Mechanical Challenges
A central challenge lay in achieving both range of motion and structural rigidity. Horses can stand for extended periods by locking their limbs in place due to their unique musculoskeletal system. Translating this into a mechanical model required careful attention to the number and positioning of pulleys, joint angles, and pivot points. The chosen pulley count and joint placement were guided by equine anatomy, focusing on replicating the angular motion of key leg segments. However, constraints imposed by the acrylic material and the simplistic pulley-tendon system limited the range of motion. This trade-off was deliberate, favoring stability and structural integrity over the entire biomimetic movement.
One of the most informative aspects of the project was ensuring that the leg could bend to some degree but also remain rigid enough to bear hypothetical loads. The final prototype offered only a modest approximation of a horse’s gait cycle and load-bearing capacity. However, even this partial success clarified how mechanical properties and material selections directly impact the performance and realism of bioinspired robotics.
Lack of Empirical Testing and Practical Application
Due to time, material, and resource limitations, I did not conduct formal testing or quantify the leg’s load-bearing capacity. Without dedicated instrumentation or comparative analysis against actual biomechanical data, the prototype remained conceptual, serving more as an investigative platform than a field-ready solution. No direct operational scenarios were simulated, and the model did not evolve into a product applicable for military or logistical use cases—initially considered a motivating factor in the design concept. Instead, the outcome was purely exploratory, providing a valuable learning experience and design insight rather than a marketable engineering solution.
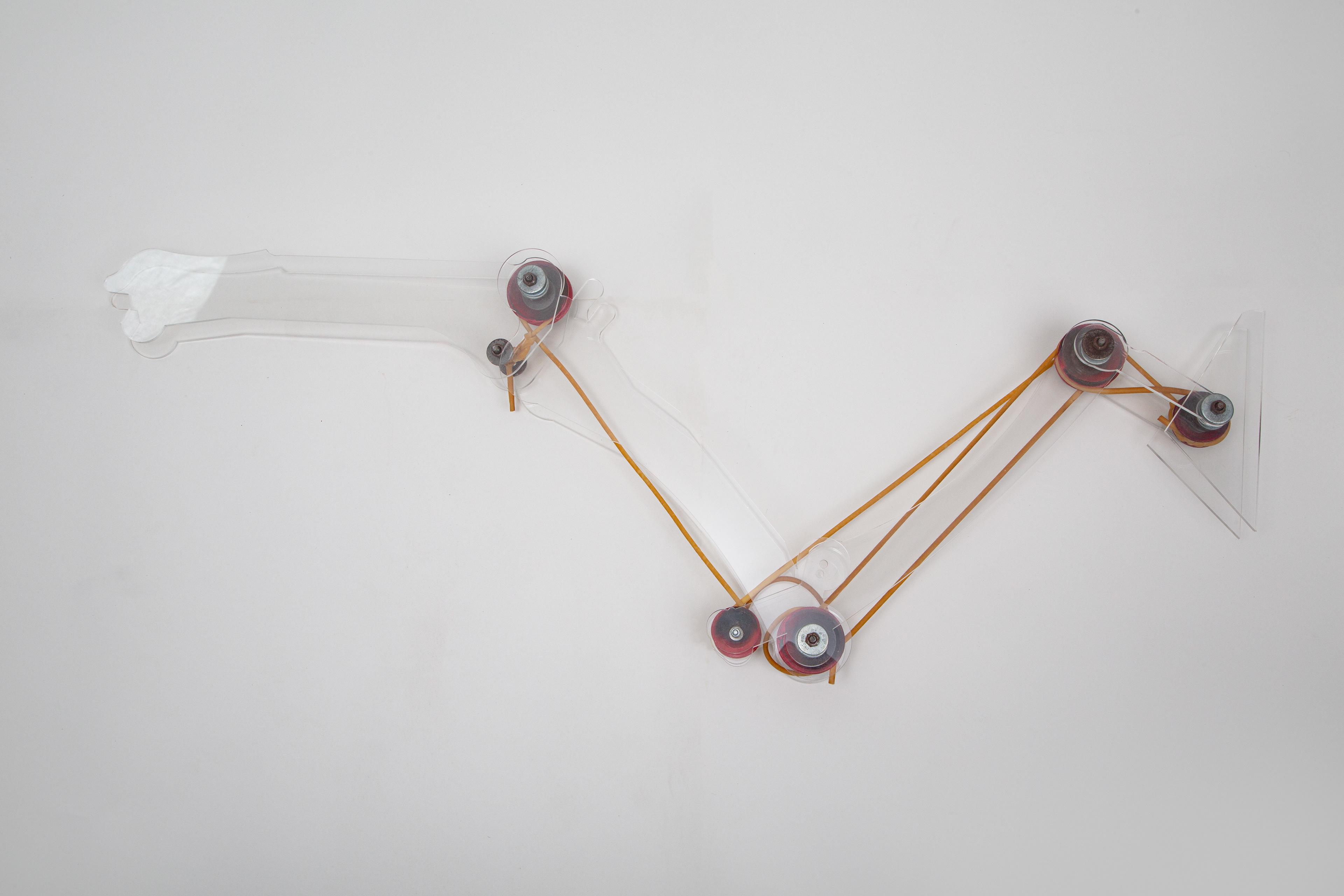
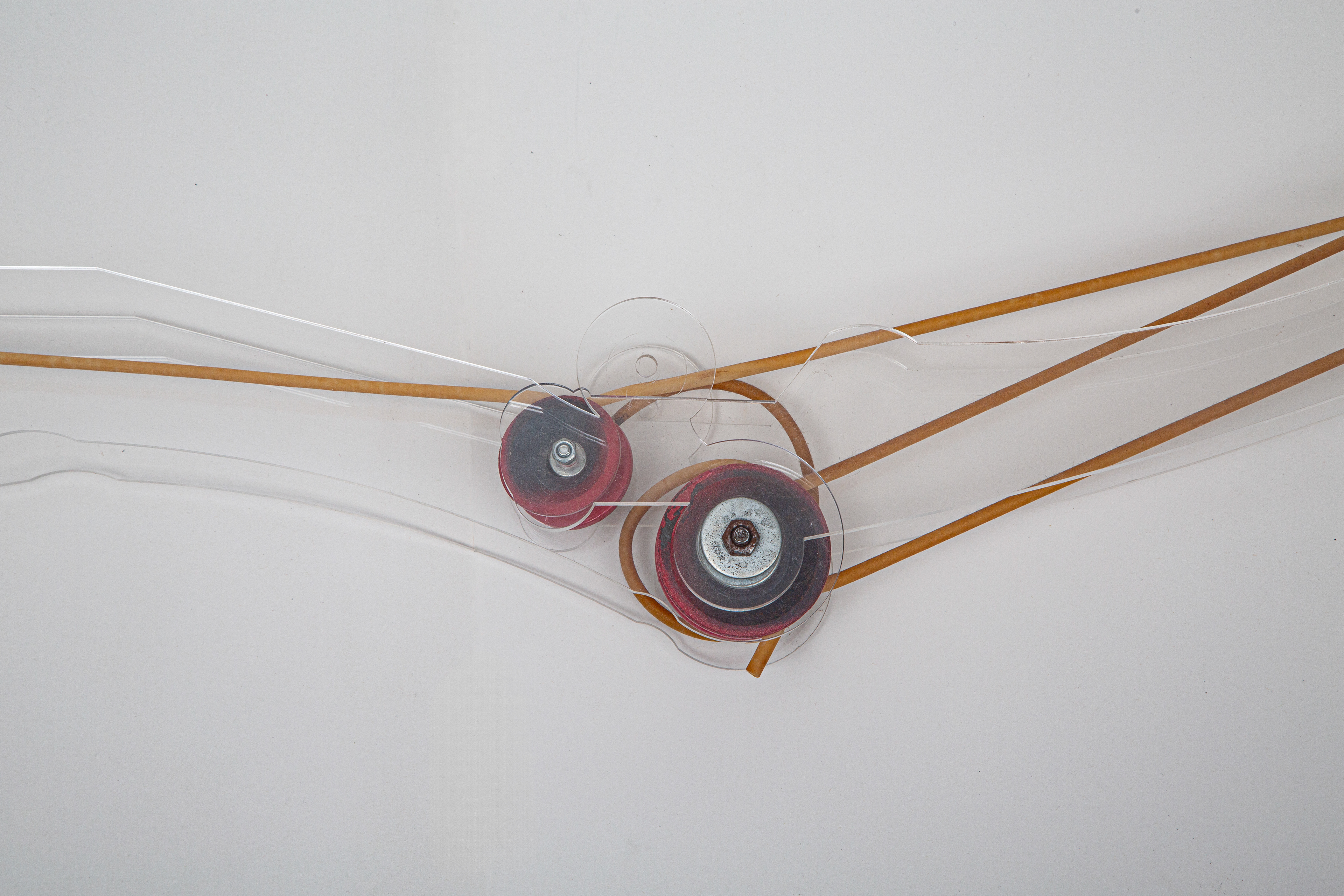
Though the final model only progressed beyond a conceptual proof of concept, the project offered invaluable lessons. In the future, I would consider integrating more advanced materials or introducing lightweight sensors and actuators to approximate a horse’s biomechanics better. Enhanced materials, 3D-printed joints with higher tensile strength, and improved elastomeric cords could yield a leg mechanism that faithfully replicates natural motion. Applying precise testing methods and engineering metrics would transform conceptual insights into data-driven refinements. While the acrylic prototype and surgical tubing tendons fell short of producing a fully functional, load-bearing robotic limb, the venture provided key insights into the nature of equine locomotion. Most importantly, it expanded my technical skill set and conceptual framework, setting the stage for more informed, sophisticated approaches to bioinspired design in future projects.
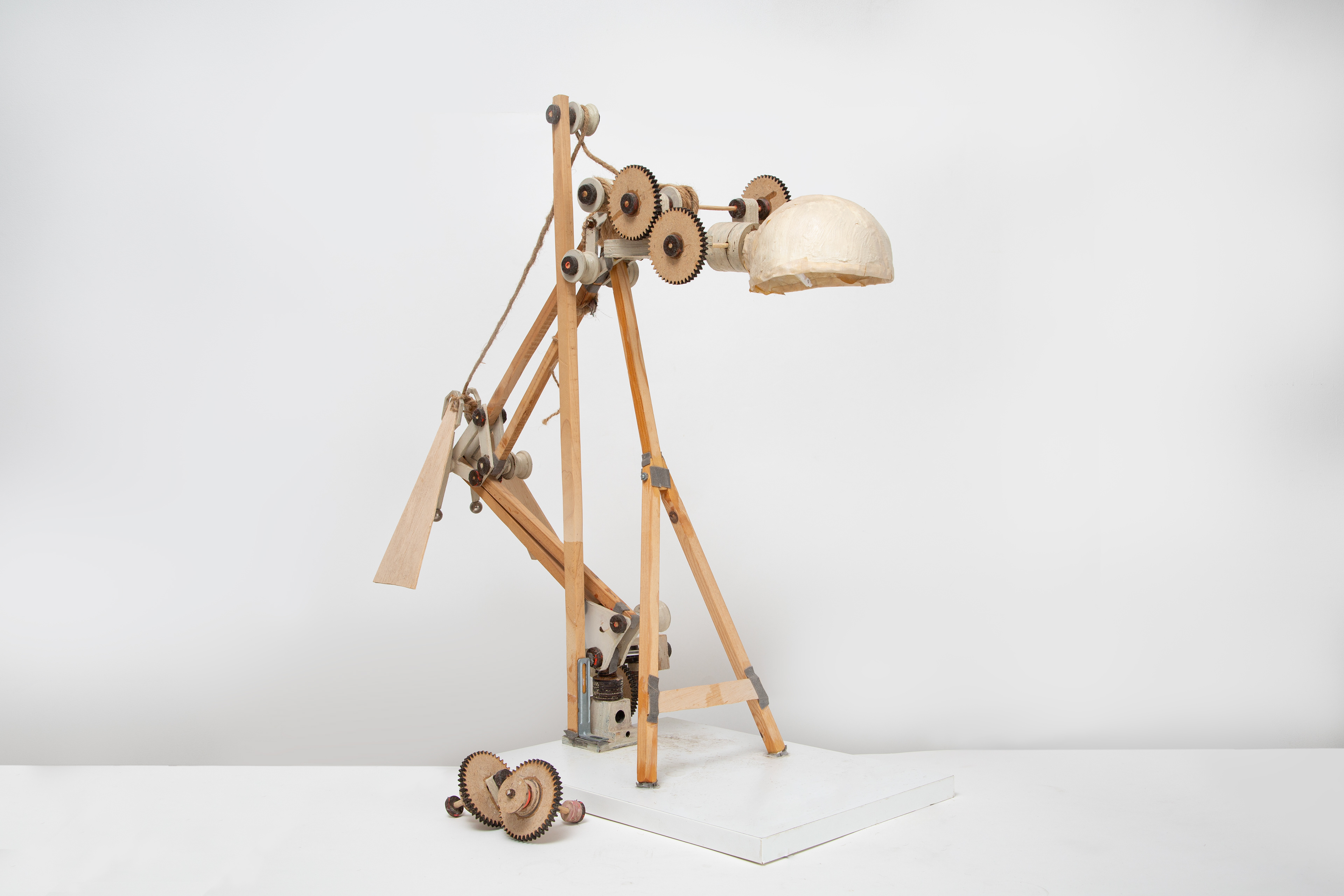
LEONARDO DA VINCI LAMP FOR SLANTED DESKS
I developed a concept for a Renaissance-inspired task lamp explicitly designed for slanted desks. My primary goal was to address the ergonomic and visual challenges encountered when working at inclined surfaces—particularly for activities like illustration, drafting, and reading. While modern flat desks are well-served by conventional desk lamps, the unique geometry of a slanted desk complicates achieving consistent, comfortable lighting. Drawing inspiration from Leonardo da Vinci’s inventive spirit, I aimed to create a lamp capable of automatically adjusting its light angle as the desk’s inclination changed, maintaining an ideal relative orientation without constant manual repositioning.
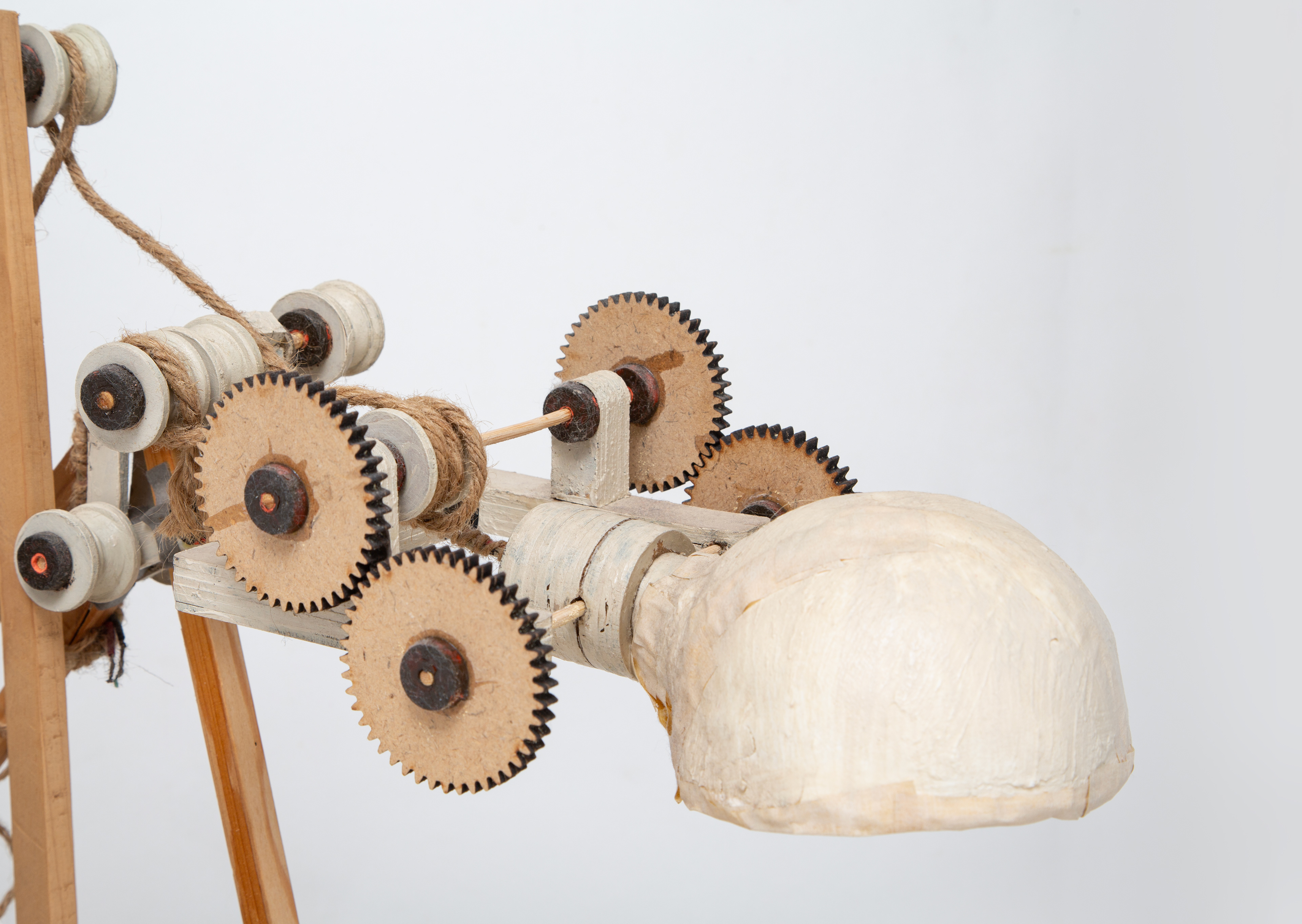
Concept and Historical Inspiration
The idea originated from the problem of inadequate illumination at inclined work surfaces. Slanted desks benefit activities that rely on proper visual alignment—such as architectural drawing, sketching, and handwriting—yet often lack proper, easily adjustable lighting solutions. Conventional lamps offer limited versatility: users must frequently readjust them to maintain optimal illumination and prevent eye strain. By studying Renaissance-era mechanical principles and Leonardo da Vinci’s approach to modular, gear-driven inventions, I sought to blend timeless aesthetics with an adaptive lighting mechanism. Incorporating wooden components, rope-covered wiring, and pulley-based adjustments, the final concept aimed to evoke the appearance and ingenuity of a Renaissance workshop while fulfilling modern functional requirements.
Mechanical Design and Adaptive Illumination
Central to the design was integrating a mechanically coupled system that adjusted the lamp’s head angle in response to changes in desk inclination. Instead of manually re-aiming the lamp each time the desk was raised or lowered, the pulleys, gears, and shafts system would automatically maintain a predefined light orientation. Multiple arm segments, connected via quadrilateral and trapezoidal joints, allowed the lamp to extend, retract, and pivot with minimal user intervention. This arrangement required careful consideration of weight distribution, friction, and mechanical stability. The goal was a lamp that could support a focused LED light source over an inclined surface and retain its relative position as the desk angle changed—improving comfort, reducing eye strain, and eliminating repetitive adjustments.
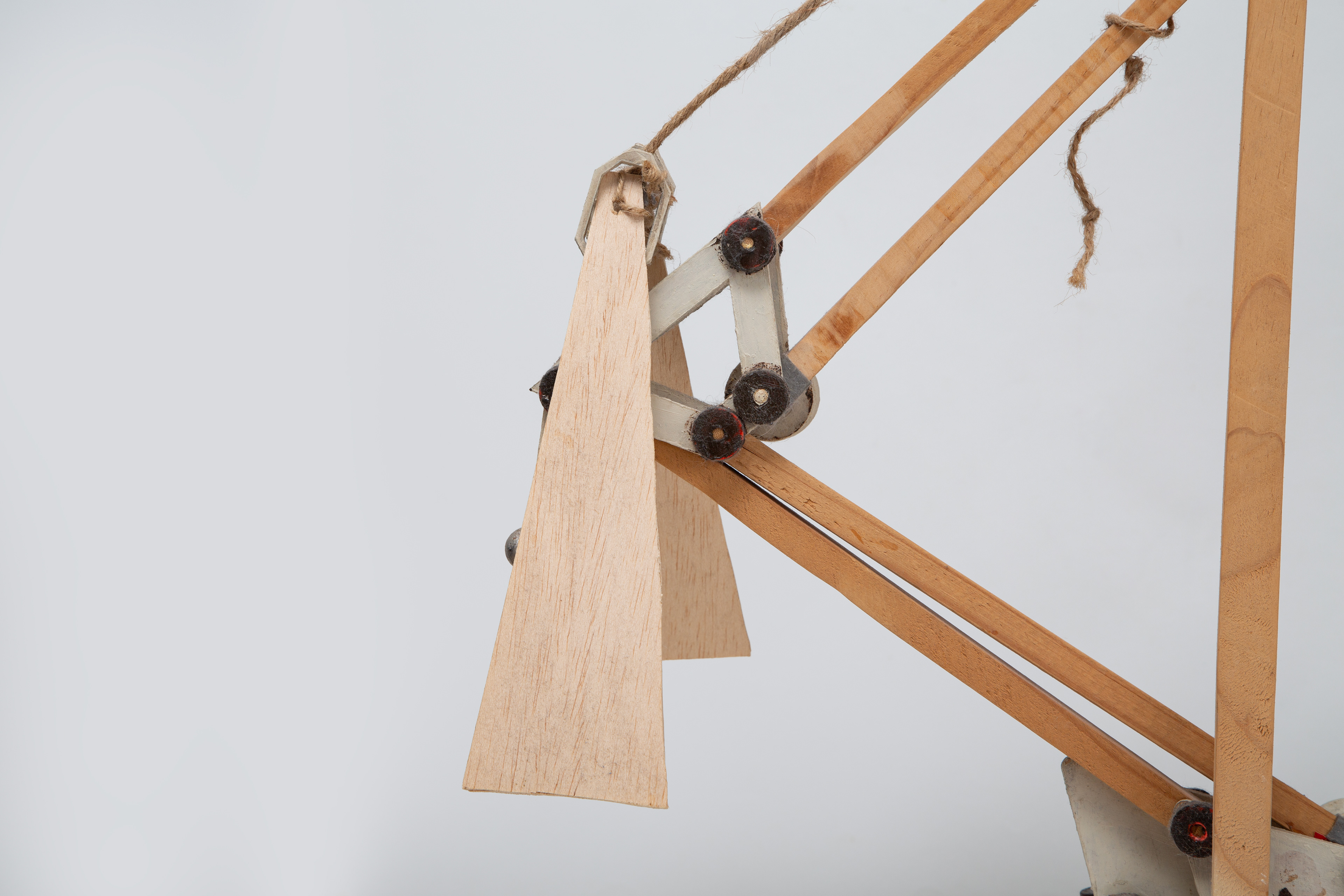
Materials, Aesthetics, and Renaissance Elements
A key design objective was to reflect the ingenuity and visual language of the Renaissance era. Instead of modern plastics or metals, I used wood for the structure and rope-covered wiring to conceal the electrical elements. A warm brown color scheme and small aesthetic details—such as a pulley arrangement reminiscent of da Vinci’s early flying machine sketches—reinforced the historical theme. This approach suited the conceptual narrative and influenced material choices and assembly methods. While acrylic or steel might have provided more excellent durability, wood and MDF were selected for their ease of fabrication, alignment with historical aesthetics, and compatibility with the available cutting and drilling tools. Though these materials introduced limitations in load-bearing capacity and friction management, they provided an authentic, tactile quality consistent with the project’s conceptual roots.
Implementing the Mechanisms and Adjustability
The lamp’s adjustable nature hinged on carefully arranged pulley systems and gear assemblies. I conceived multiple pulley diameters and complex linkages to balance the load and ensure fluid motion. However, practical considerations led to standardizing pulley sizes and using washers to achieve stable rotations. While simplifying production, these design changes influenced the degree of achievable automatic adjustment. The final prototype allowed the user to manipulate height, reach, and angle through manual adjustments and gear-driven movements. Though the lamp did not achieve a perfectly seamless automatic orientation—due to material friction, weight distribution challenges, and the complexity of the rope-and-gear interplay—it successfully demonstrated the feasibility of a mechanically adaptive lighting concept.
Testing and Limitations
Due to time and resource constraints, formal load testing and precise biomechanical comparisons were not conducted. Qualitative evaluations showed that the lamp could be clamped to an inclined surface and, within a limited range, maintain its intended lighting orientation as the desk angle shifted. However, some drawbacks emerged. The system struggled with weight distribution at extreme angles, and rope slack occasionally impeded smooth transitions. While the lamp remained functional as a task light and offered improved positioning control compared to a conventional lamp, it did not fully realize the ideal of effortless, automatic reorientation. This partial success nonetheless provided valuable insights into mechanical coupling strategies and material trade-offs.
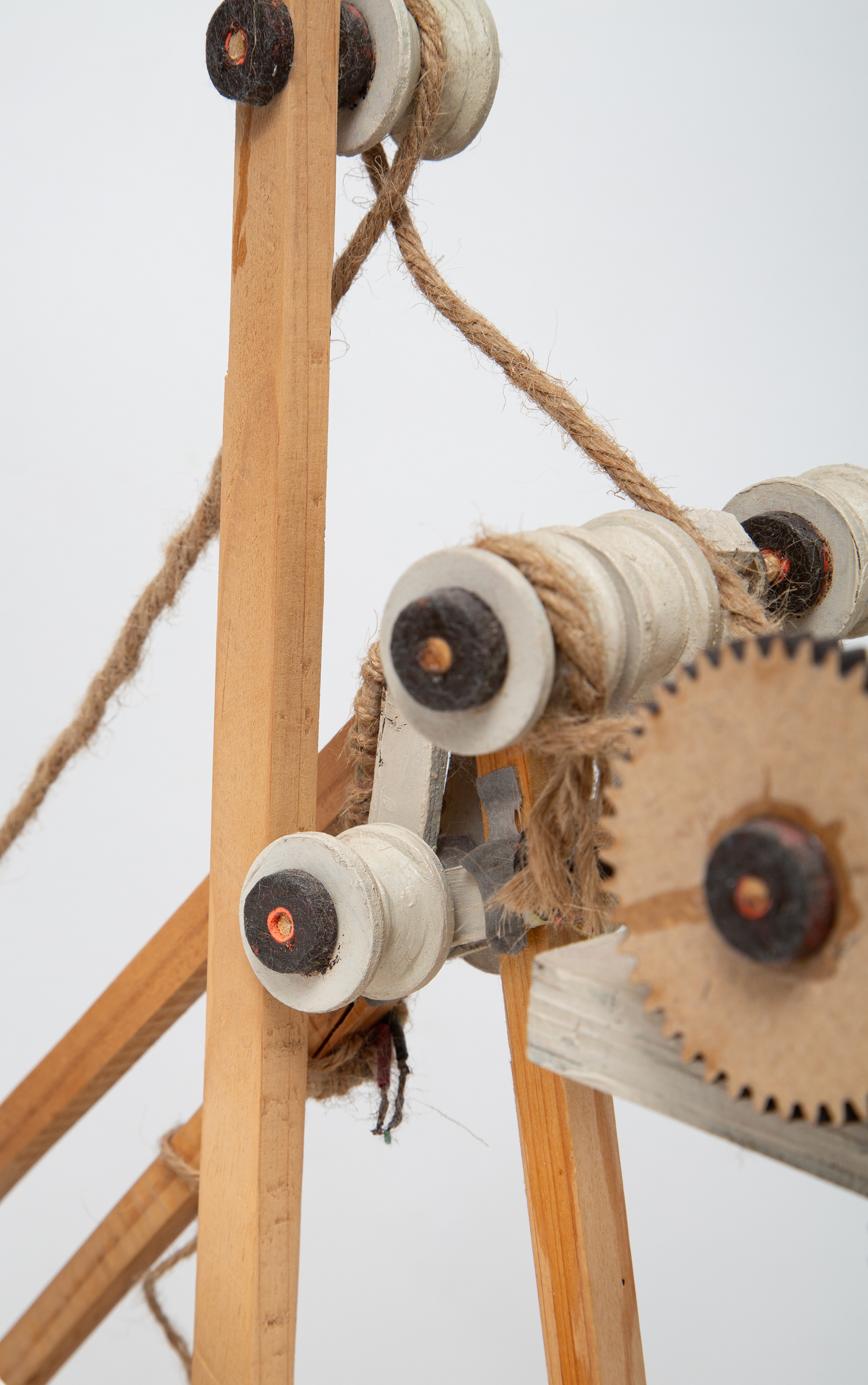
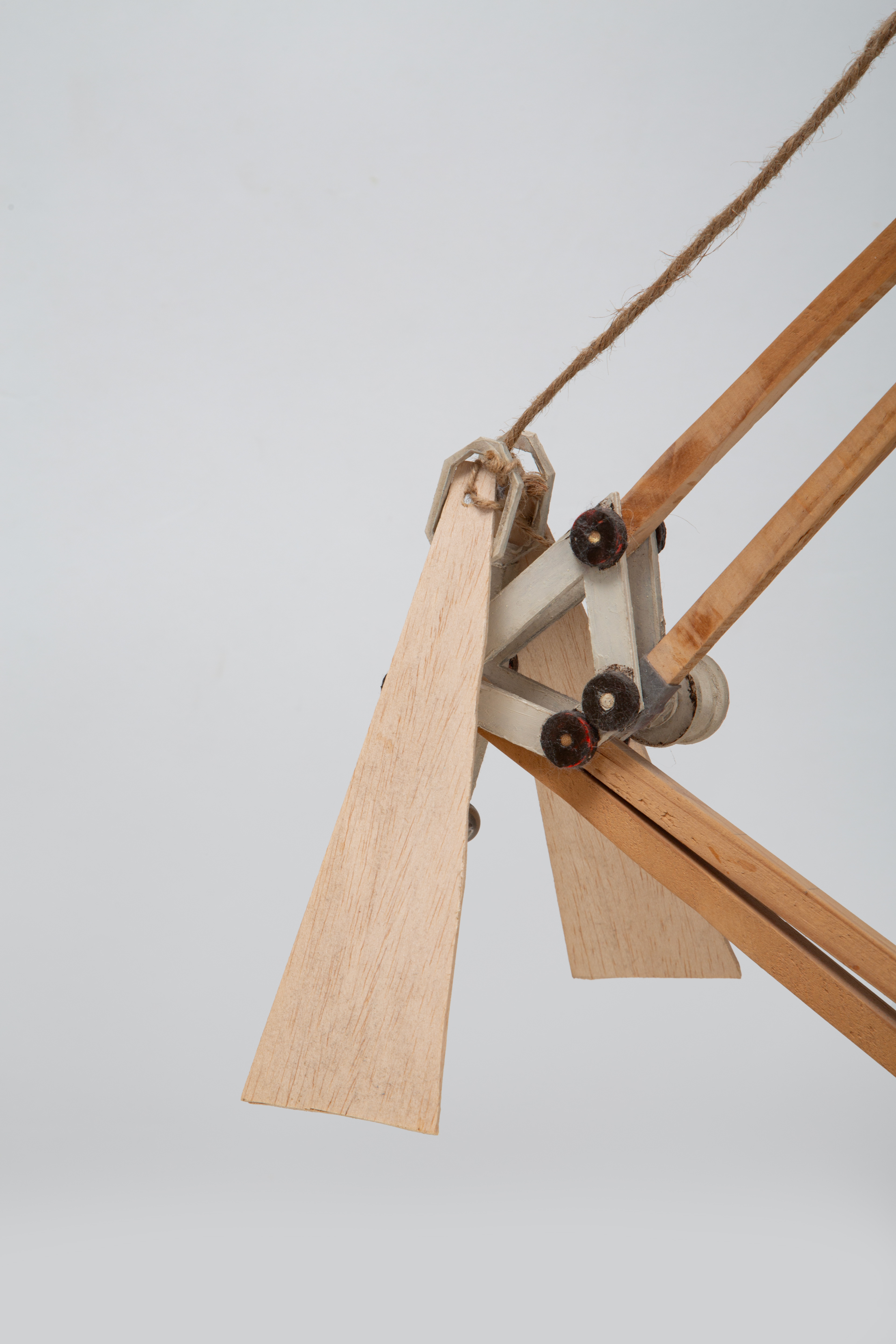
If allowed to iterate, I would integrate more robust mechanical solutions. Ball bearings and roller joints could reduce friction, and lighter materials or optimized joint geometry could improve load distribution. Introducing sensors and servo motors might automate adjustments more reliably—blending Renaissance aesthetics with subtle modern electronics hidden behind wooden housings. Refining the pulley system to minimize rope slack and employing more precise gearing would allow the lamp to respond smoothly to desk inclination changes.